triple
Membre actif
salut DIY rc tx
tout est parti du Mmag de Juin 2015 et de ce post : NextStepRC : radio OpenTX DIY (MMag juin 2015)
utilisateur convaincu d'OpenTx depuis 3 ans , j'ai commandé le kit NextStepRC chez cncfilchaud
étant sur Mayotte , je ne récupère le kit ( + quelques options perso ) que dans quelques temps lors de mon passage en métropole et vu qu'il y a le boîtier en bois en " rescue " dans le kit , j'ai commencé un boîtier plexy
à s'y mettre , autant le faire aux dimensions perso " kivonbien " :
angle des bras
taille des mains
angle des manches
positions des inters - potars - encodeurs rotatifs par rapport à la longueur des doigts
épaisseur du boîtier...… ( au final : 43mm )
après quelques essais découpés dans du carton voilà les dimensions finales
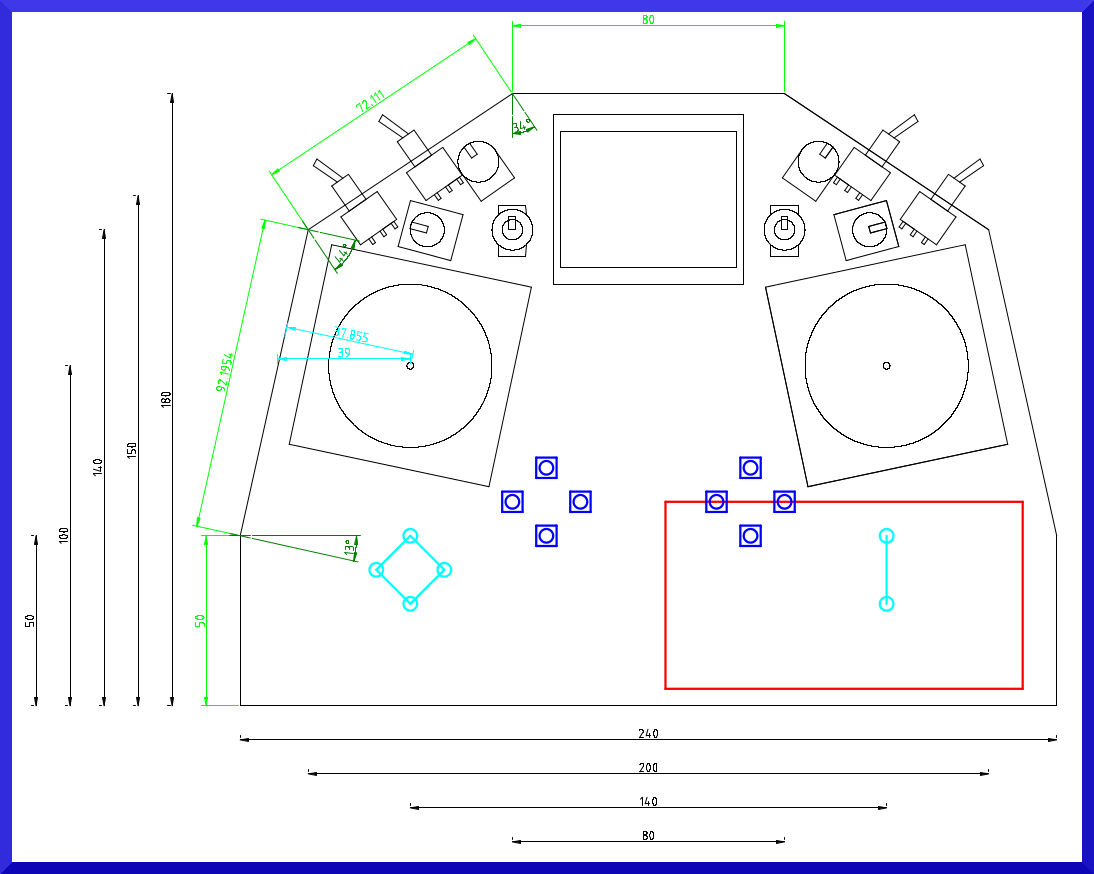
le Plexi de 3 mm est récupéré en démontant un écran LCD de Télé HS
vu sur des sites d'aquariophilie et de tuning PC ( boite pour le water-cooling ) , le plexi se colle au chloroforme………..
-----problèmes :
- il faut une ordonnance
- trouver une pharmacie qui en a encore ( surtout ici sur Mayotte )
- il semblerait que ça soit un poil dangereux à manipuler ( vu sur wikipédia , visiblement , on est pas dans un film ... )
- le + gênant : éventuellement finir endormit la tête dans le plexi
hi hi hi ! ! !
du coup , test à la cyano , ça colle mais c'est pas super costaud , et surtout ça laisse des traces blanches à l'évaporation du solvant
plus facile à trouver : l'acétone , ça fond les parties en contact = c'est costaud , par contre la préparation des pièces avant collage demande du temps et il ne faut pas se louper en déposant la goutte d'acétone sur la jonction
découpe des pièces à la Dremel - enfin , une mini-perceuse... - avec l'accessoire Dremel "kivabien" et une cornière en alu en " L " pour guide
il faut faire des tests pour trouver le bon compromis vitesse de rotation / vitesse d'avance par rapport à l'épaisseur du plexi : si la fraise force trop et-ou tourne trop vite , elle chauffe , le plexi fond , forme une "bourre" qui s'y colle et encrasse la fraise
le plexi est posé sur une plaque de polystyrène pour que la fraise traverse
usinage à la main + dremel des évidements circulaires pour les manches : prévoir un " certain temps "
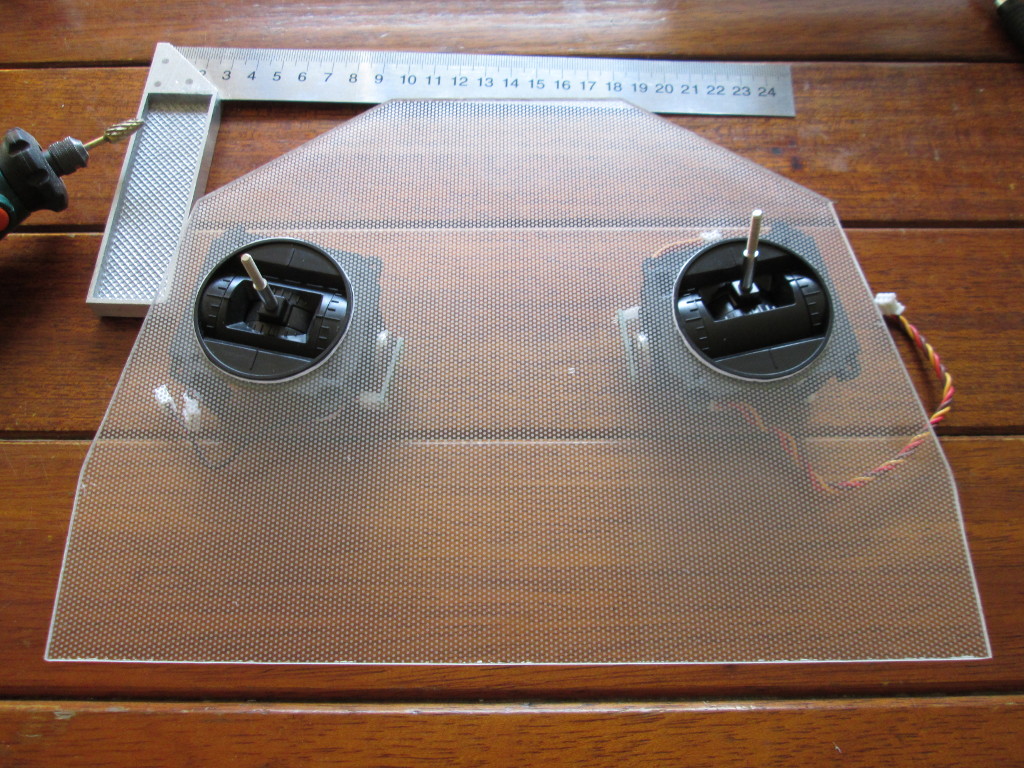
il faut préparer les pièces à réunir : le " collage " à l’acétone ne remplit pas les interstices , ça fait fondre localement les deux surfaces qui fusionnent
donc les deux pièces à joindre doivent présenter une surface en contact 100 % plane et très lisse pour être la plus grande possible
--> ponçage des champs au gros papier de verre posé sur une vitre jusqu'à arriver contre le tracé puis au papier très fin toujours posé sur une vitre , là , c'est long mais indispensable
il n'y a pas de n° sur mon papier de verre fin mais c'est celui utilisé en dernier pour la finition des gel-coat bateaux , il doit y avoir des équivalents chez Brico au rayon carrosserie
- caler les pièces avec du scotch <---> ne pas tenir à la main sinon ça va bouger vu le temps de séchage
- poser une goutte d'acétone pile-poil sur la jonction , si les pièces ont été bien poncées , on voit bien l'acétone qui se répand par capillarité entre les deux surfaces
>>> si une goutte tombe sur le plexi , c'est le drame
: l'acétone attaque la surface et laisse un vilain voile blanchâtre opaque
aucune idée du temps de séchage – évaporation - fusion , j’attends 10 min environ avant d'enlever le scotch , ça tient
là c'est un des mes nombreux essais sur des chutes , la goutte d'acétone est déposée avec une seringue
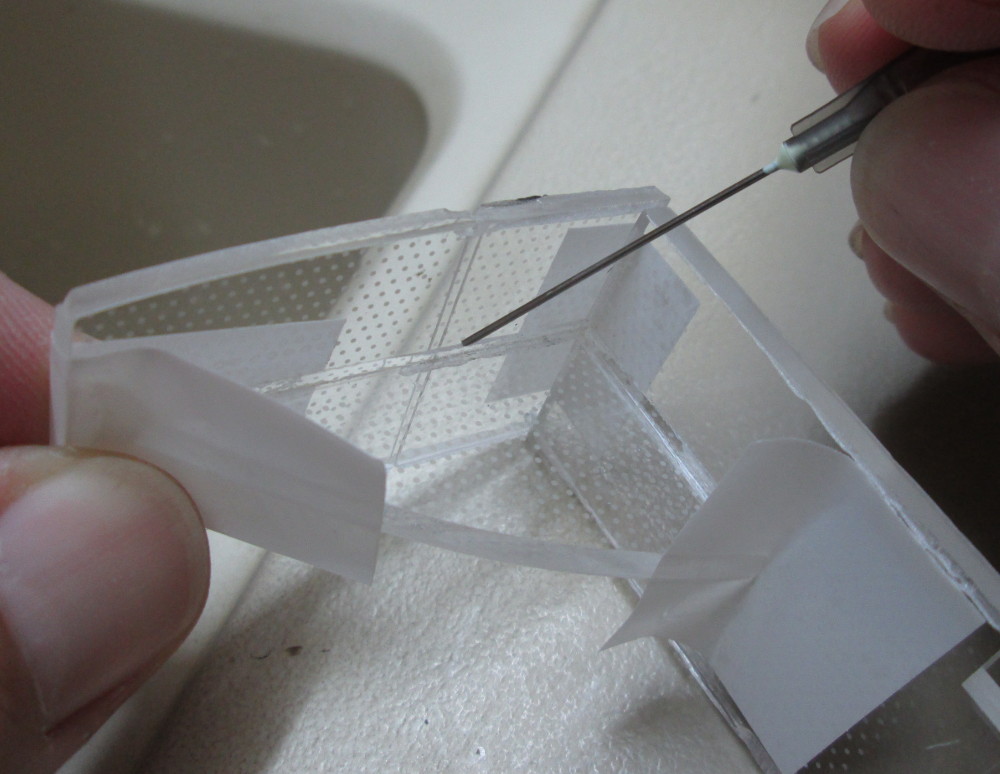
quand les surfaces en contact sont bien planes et lisses , la jonction devient quasi-transparente , les deux pièces " fusionnent " , la partie non-soudée est le futur passage du coaxial de l'antenne
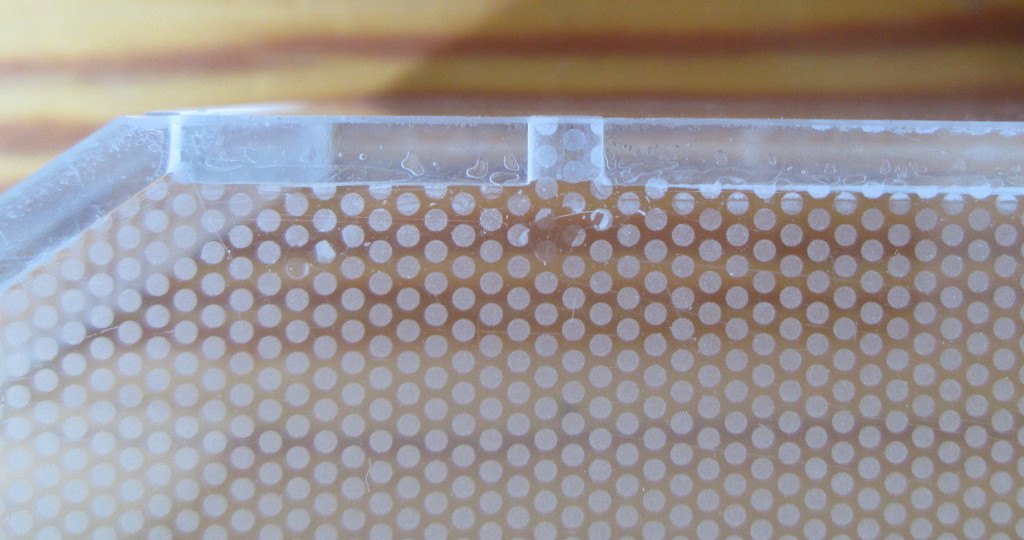
voilà le boîtier qui prend forme
évidement , il faut aussi poncer finement et aux bons angles les parois latérales pour qu'elles s'ajustent avant collage , là aussi prévoir un " certain temps "
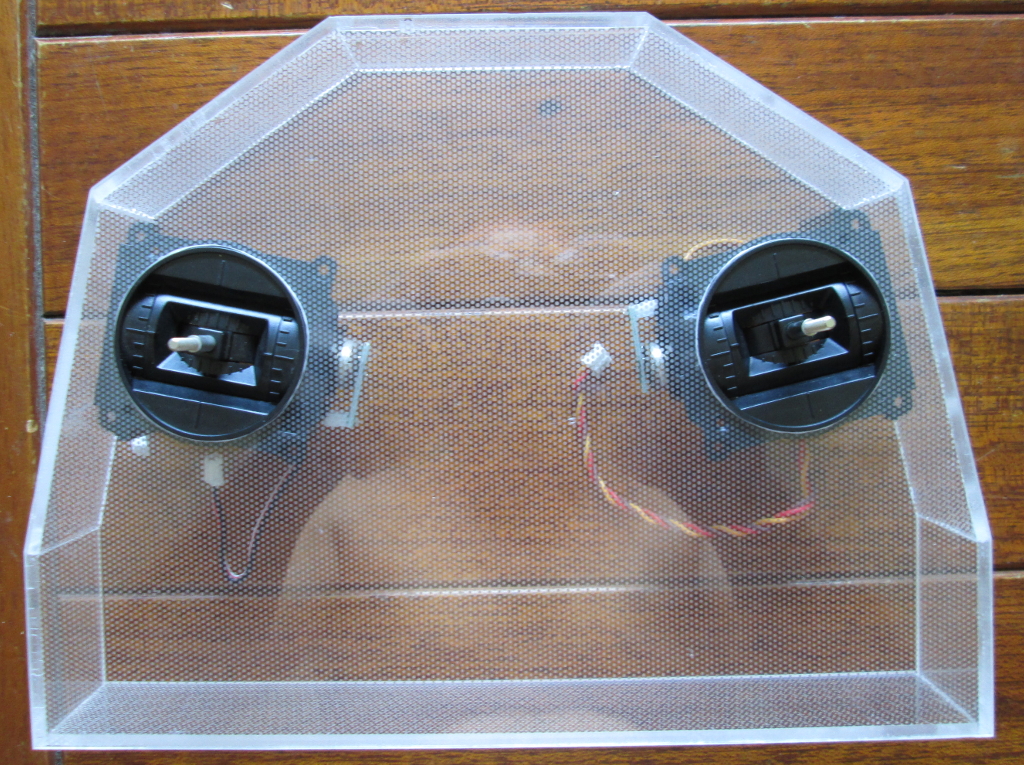
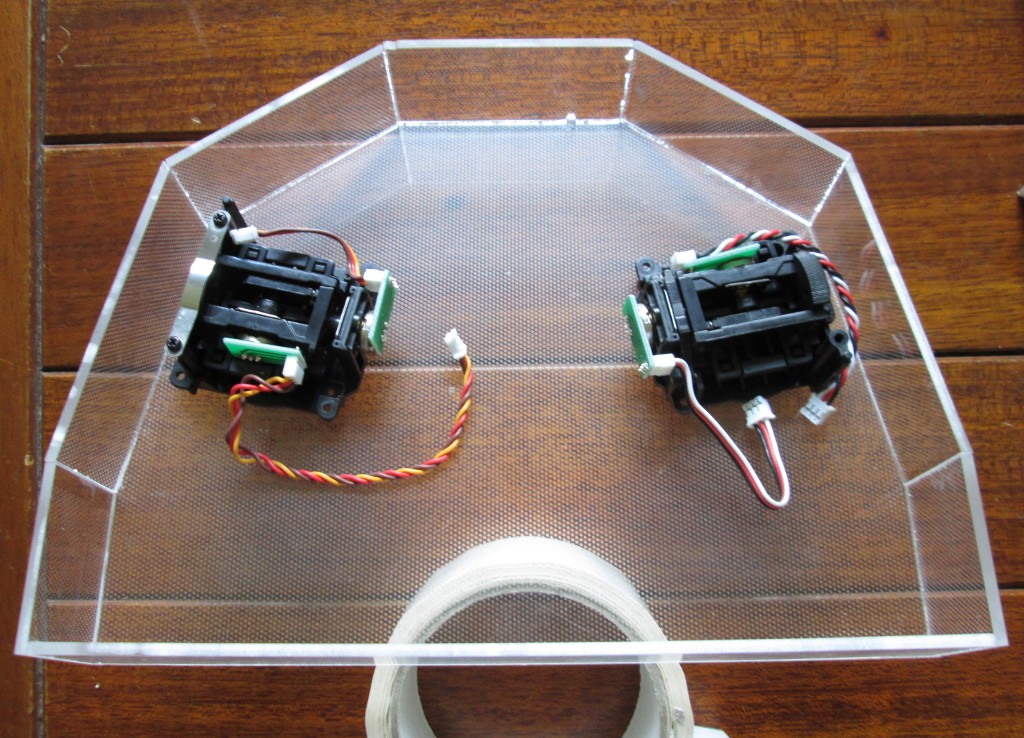
collage de 4 pièces qui font renfort aux angles + cales de hauteur pour le fond du boîtier qui rentrera dans le cadre
là aussi : ponçage aux bons angles avant collage
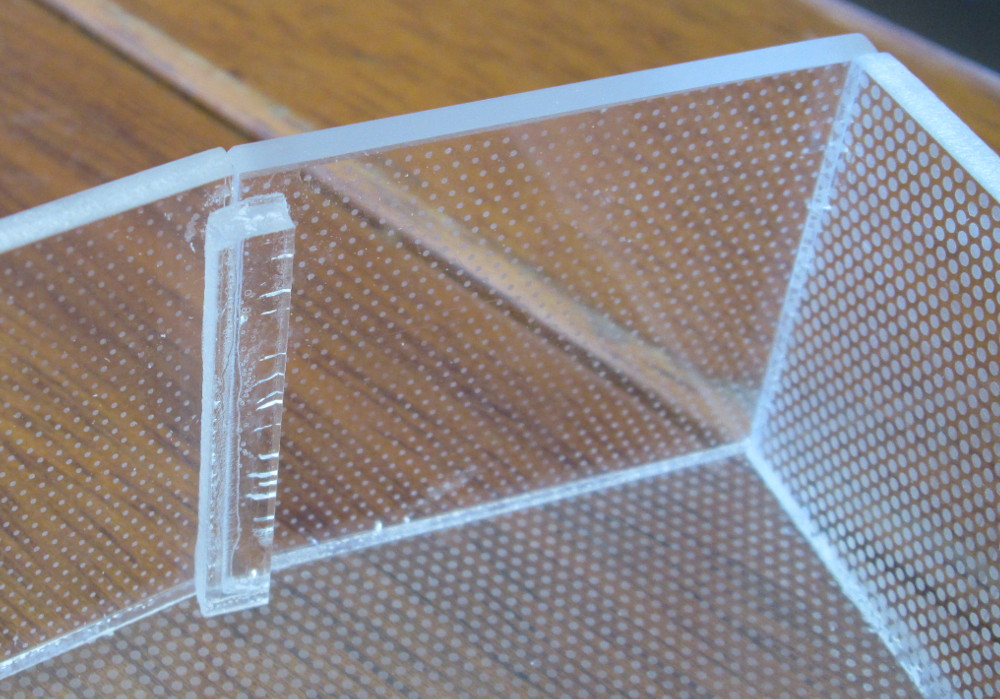
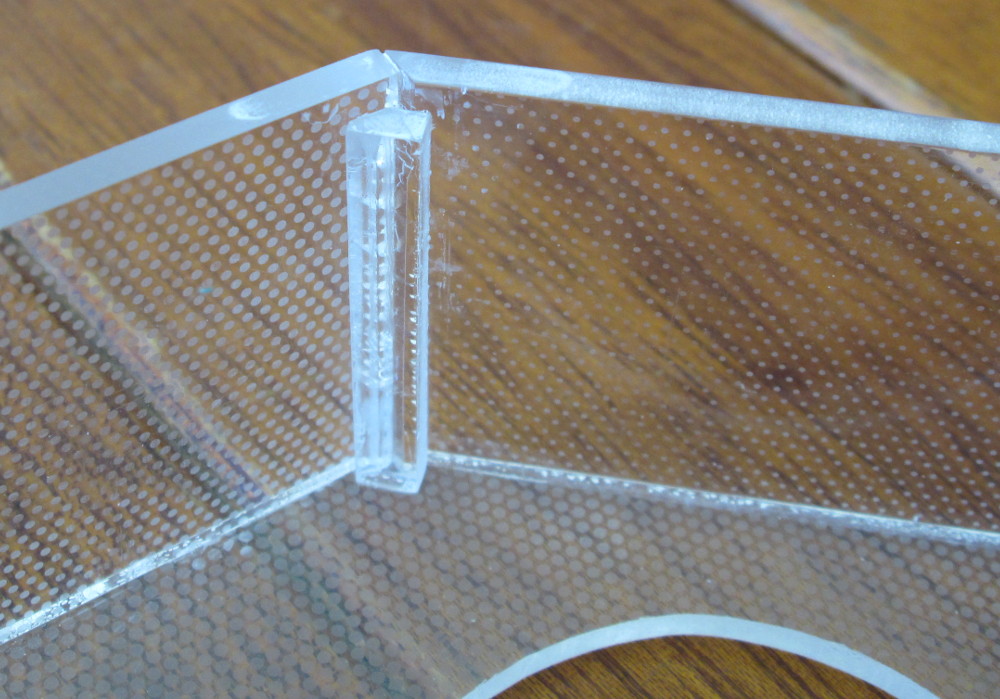
le fond est tenu par 3 paires d'aimants de 10mm de diamètre collés au pistolet à colle chaude
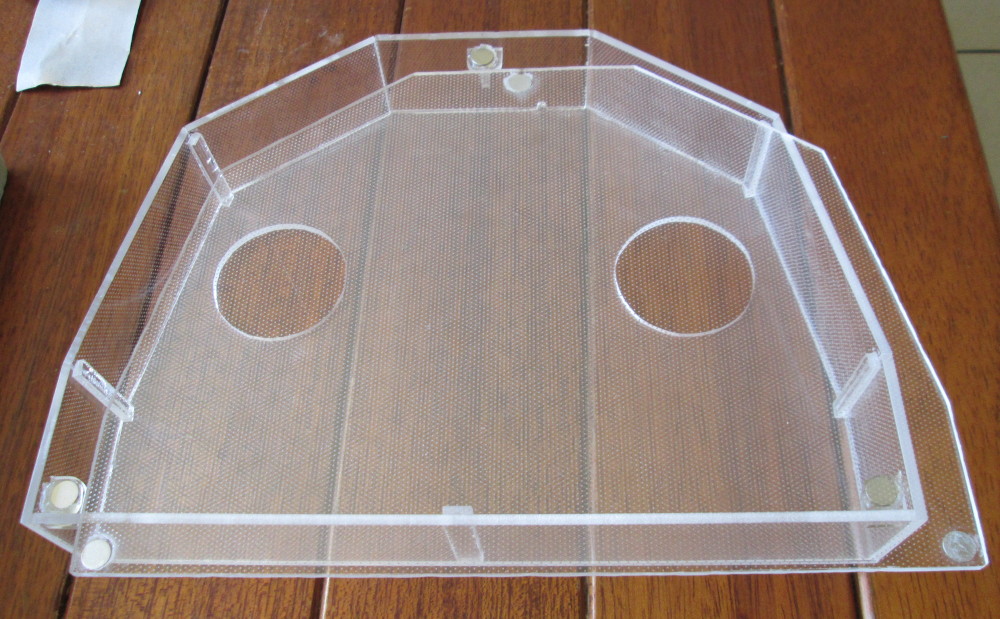
celui du haut
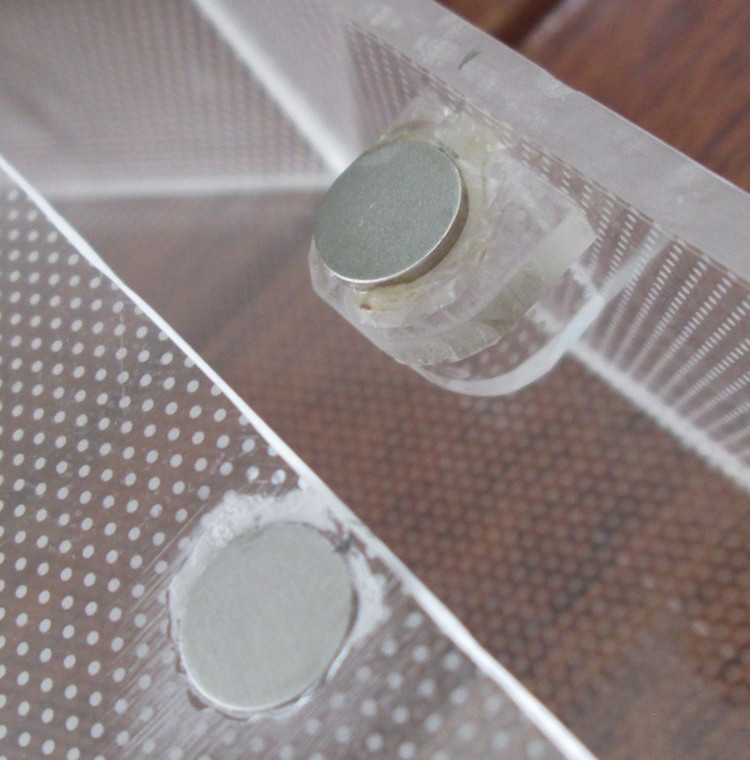
et en bas
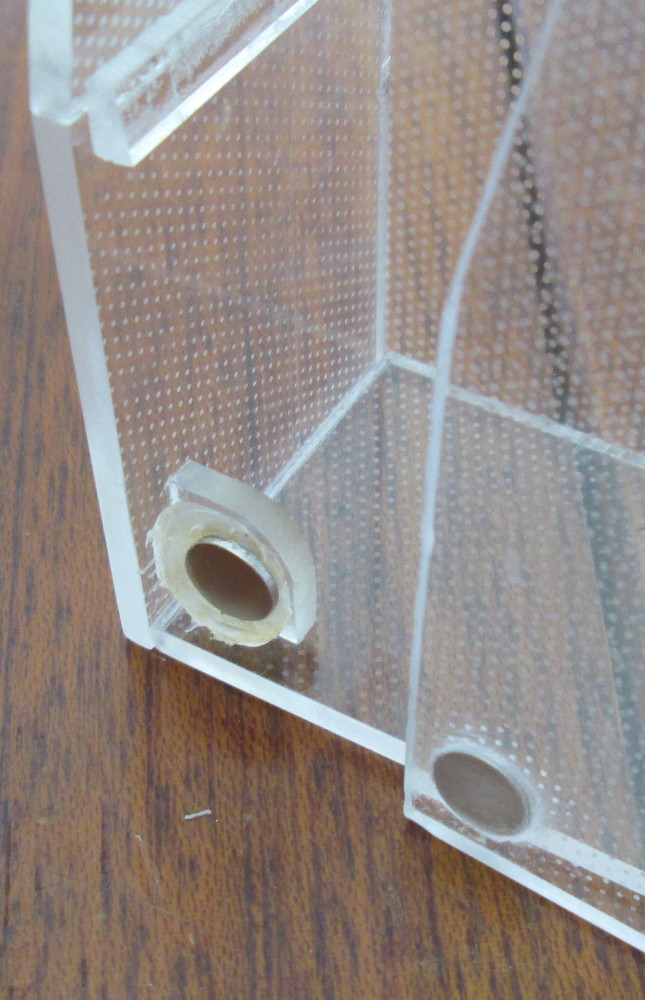
les inters et potars sont en place
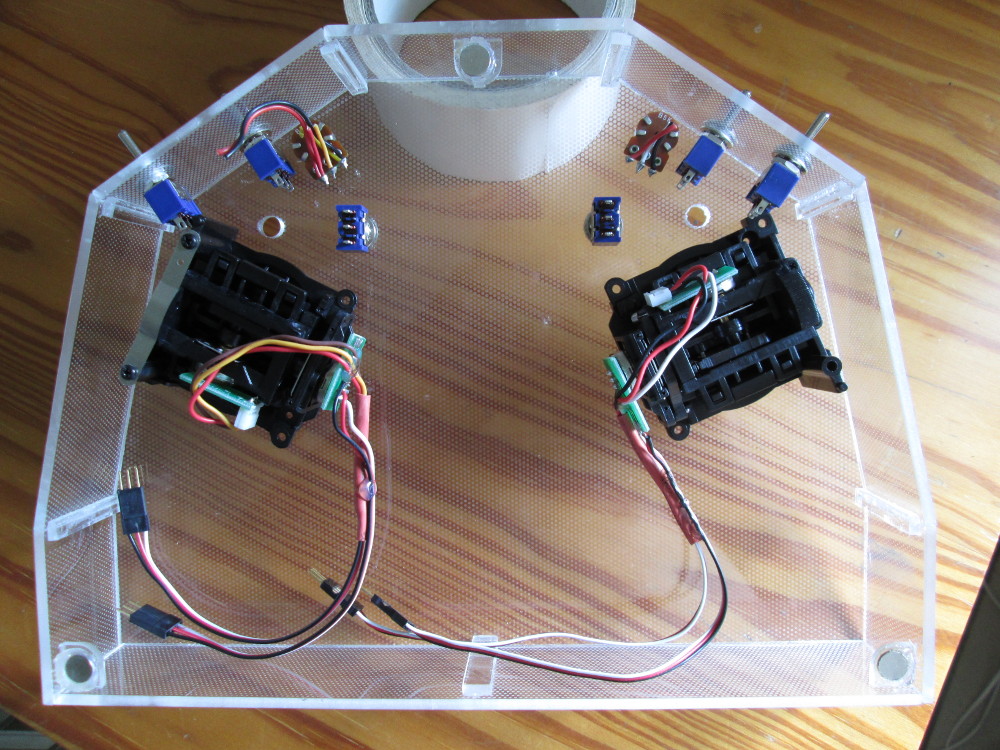
toutes les soudures sont faites sur place pour avoir direct la bonne longueur de fil --------> 'faut pas glisser avec le fer à souder ou faire tomber une goutte d'étain
le câblage des manches et potars est fait avec les rallonges de servos : sur la prise , le fil rouge central est soudé à la patte « curseur » = s'il faut inverser le sens de rotation à la 1ère mise en route , il suffira de faire "demi-tour" à la prise
comme signalé dans le post NextStepRC , en dé-torsadant les fils des potentiomètres aileron et dérive , le mouvement des axes gagne beaucoup en souplesse = un retour au neutre + précis
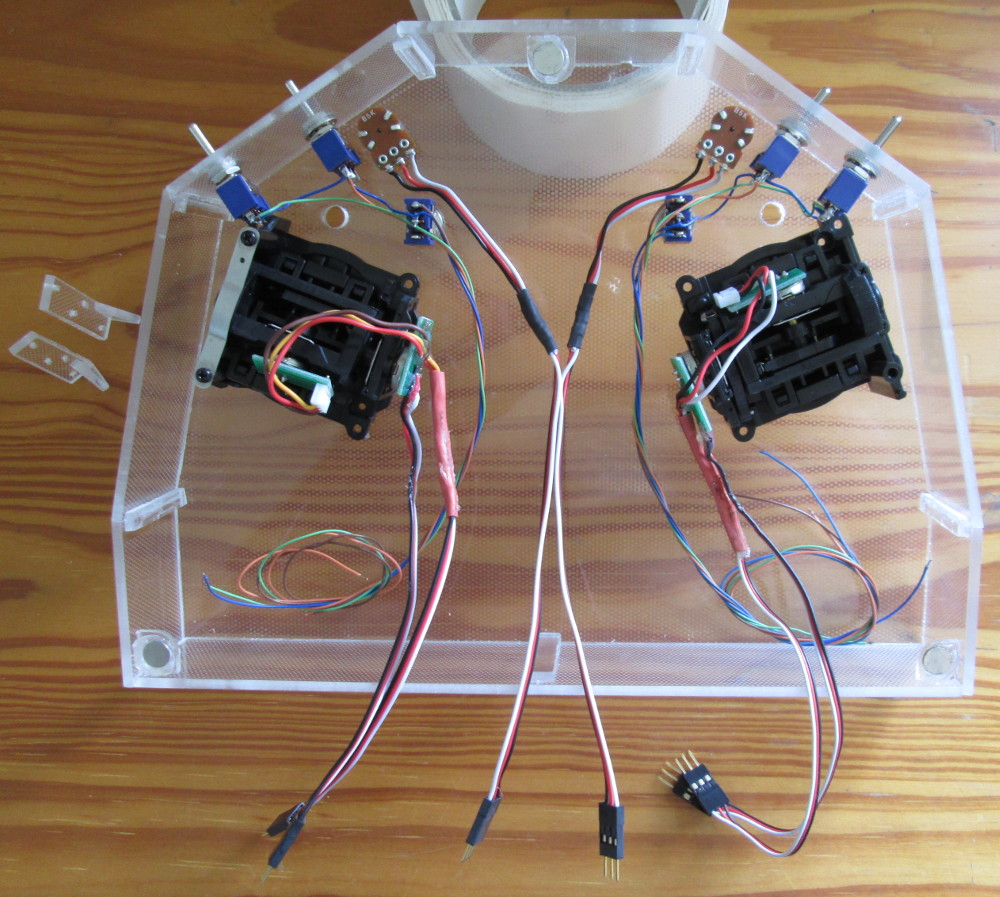
les 2 pièces en " L " au centre ( à gauche sur la photo de dessus ) permettent à la fois de caler le fond - elles font la profondeur du boîtier , comme les cales latérales - et serviront de fixations intermédiaires pour que les fils ne pendent pas entre les soudures et le mega2560
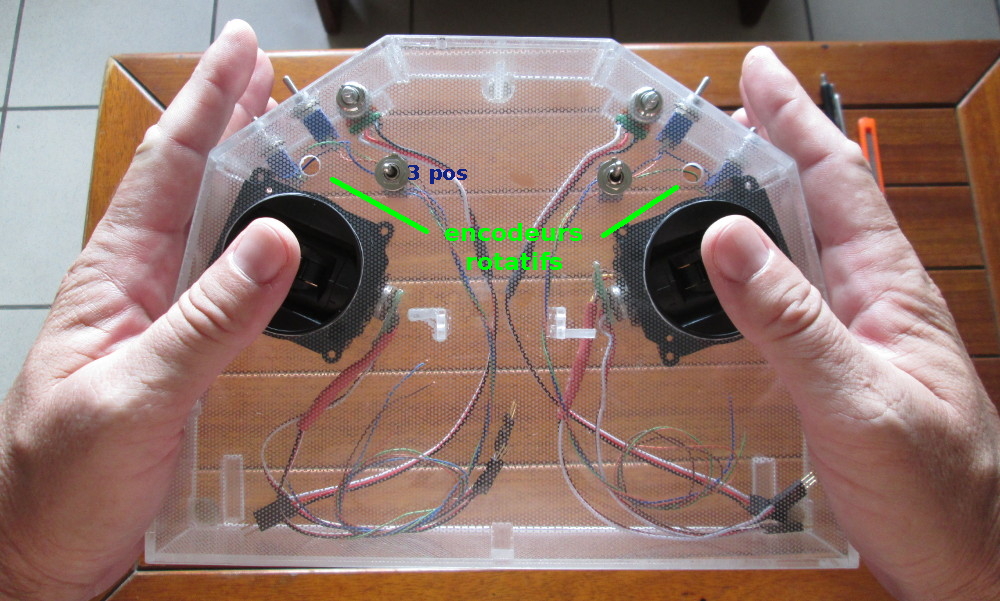
ça devient bon : tout est à portée de doigt , pas besoin de lâcher les manches
la suite en octobre une fois le reste du matériel récupéré
---- 22/09/15
de retour de métropole avec avec le reste du matériel , la suite :
réalisation du support du MEGA2650 et des deux plots taraudés pour deux vis plastiques de 3mm
les 4 fils orange-marron et bleu-noir sont ceux des 2 boutons de navigations "entrée" et "exit"
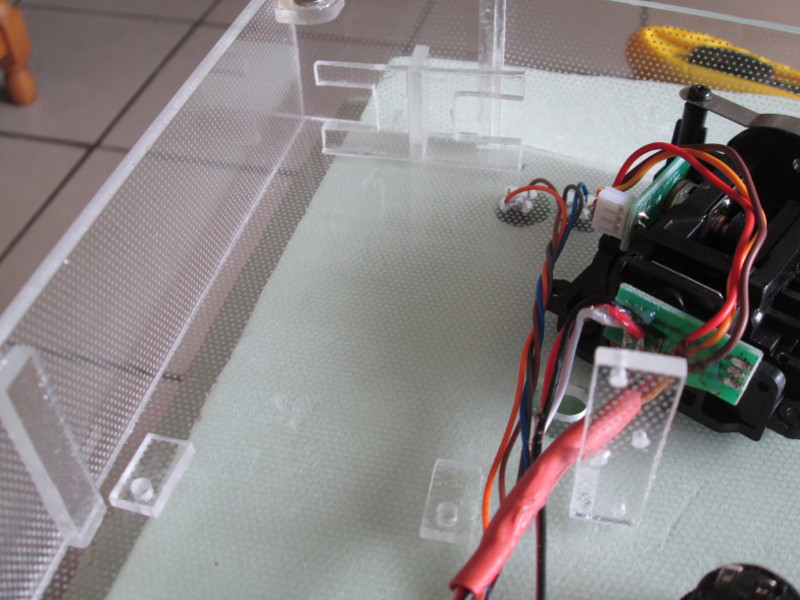
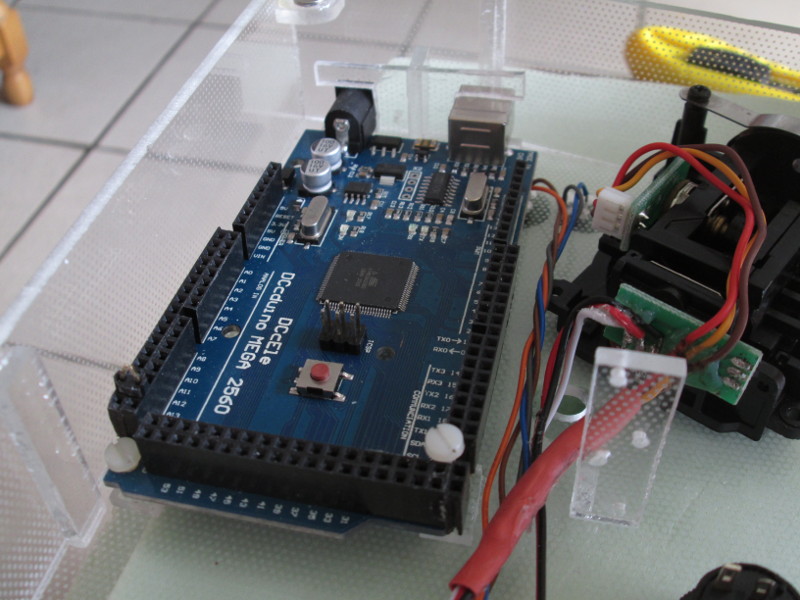
collage de barrettes supplémentaires et câblage vers le 0V pour les bleues et les +5V pour les rouges
en bas à droite le cavalier qui met l'entrée " P3 " à 0V ( pas câblé-installé pour le moment )
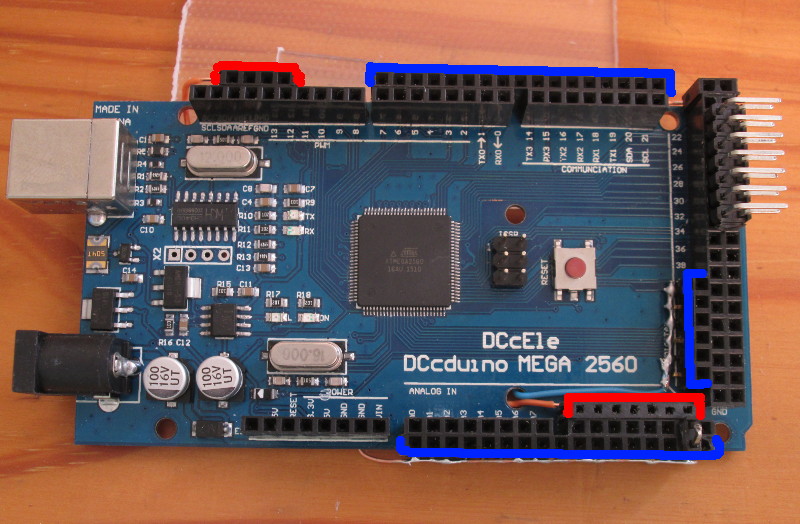
vue de dessous
en haut à droite , soudure de 7 condensateurs de 100nF entre le " 0V " et les entrées analogiques ( 4 manches et 3 potentiomètres )
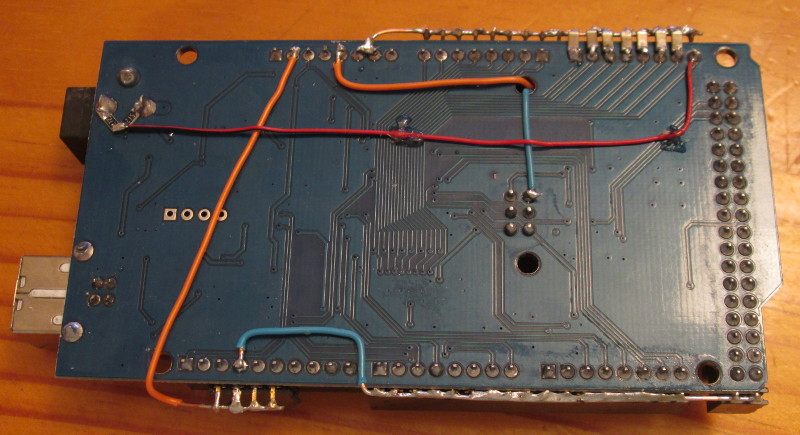
---- 23/09/15
le GRAND avantage des encodeurs rotatifs par rapport aux potentiometres , un post de M. F.Aguerre : http://frskytaranis.forumactif.org/t376-article-modele-magazine-decembre-2013
"
Côté technique : à quoi sert un encodeur rotatif ?
Réponse : à régler efficacement une variable en vol.
Prenons un exemple tout simple : soit un planeur avec 3 phases de vol (gratte, lisse, vitesse, par ex.) sur lequel on souhaite distinguer le différentiel d'aileron par phase. Pour cela, on affecte une variable globale (mettons VG1) comme taux de différentiel aux mixeurs, puis on créé une fonction personnalisée pour régler VG1 par un potentiomètre. Pour rappel : chaque variable globale VGx a une valeur propre par phase de vol sur la Taranis, inutile donc de dupliquer les mixeurs.
Le gag, c'est qu'en basculant d'une phase à l'autre, le potar (qui est un organe fournissant une valeur absolue, proportionnelle à sa position) impose de facto à VG1 la valeur à laquelle il est positionné, ce qui écrase le réglage précédent. Voilà qui est particulièrement pénible, car une fois une phase réglée et qu'on est passé à la phase suivante, il ne faut surtout pas revenir à la phase précédente sous peine d'écraser son réglage par la dernière position de potar en cours, sauf à désactiver la fonction personnalisée.
A contratio, un encodeur rotatif fonctionne en relatif par rapport à la valeur existante, il ne la change que quand on le manipule en y ajoutant ou retranchant un incrément / décrément. Donc, quand on change de phase, il n'écrase pas la valeur de VG1 en cours pour cette phase. Pour rappel, c'est exactement le principe de fonctionnement des trims digitaux de manches, qui sont eux aussi des encodeurs incrémentaux de valeurs stockées par phase.
J'ai pris l'exemple du différentiel, mais ça vaut aussi pour les dual-rate, les taux de mixage, ou toute autre valeur qu'on peut différentier par phase de vol.
"
ceux que j'ai choisi : sur ebay.com , " Rotary encoder EC12 e12 " , 24 pas par tour , l'axe fait 6mm de diamêtre , pour trouver un bouton : " knob 6mm " sur le même site
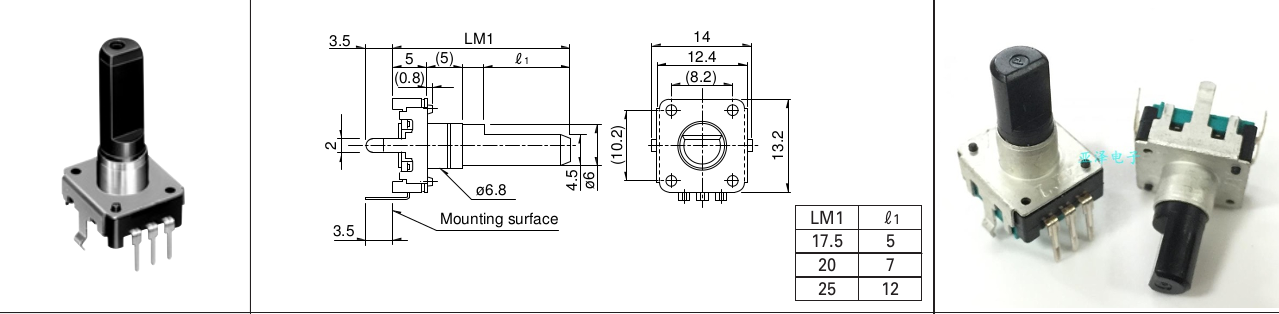
câblage des 2 encodeurs rotatifs et des 3 boutons directionnels
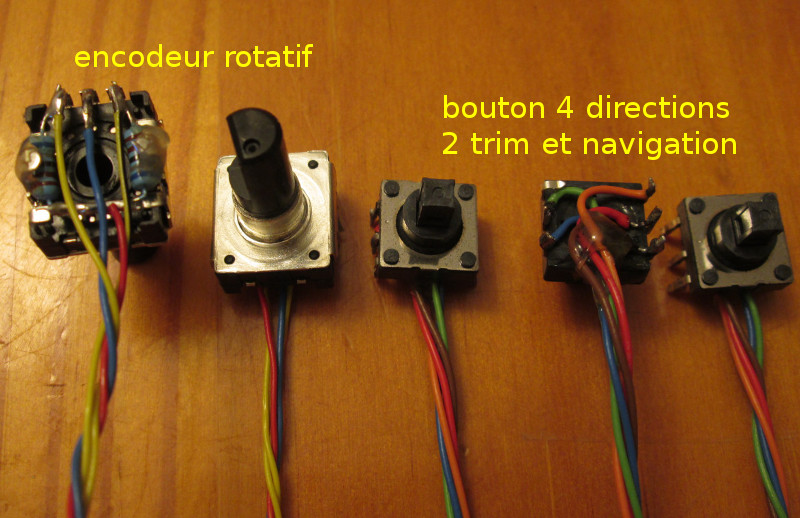
câblage de l’écran + fixation à la colle chaude <------> GAFFE ERREUR : j'ai inversé l’écran " haut-bas " , j'ai du le décoller + dessouder + ressouder les fils pour finir par le retourner
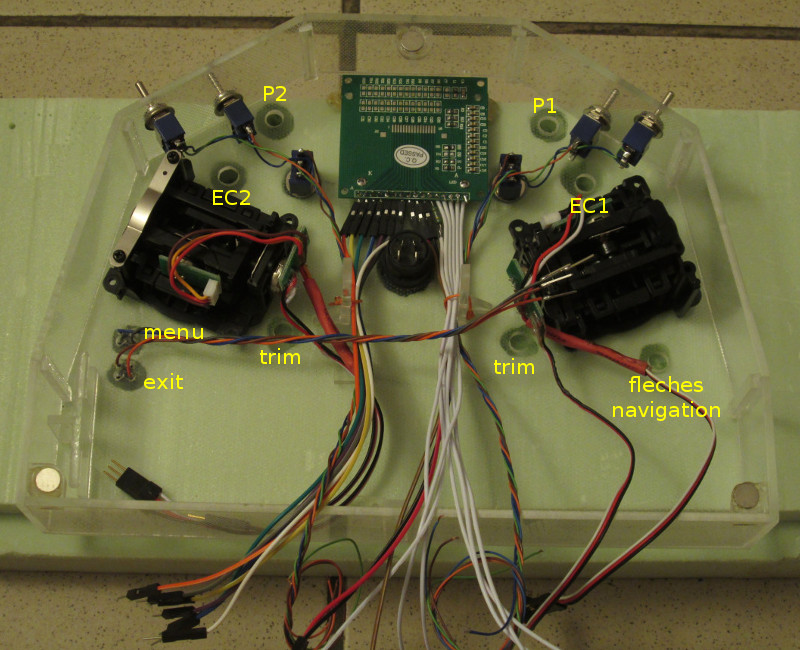
27/09/2015
collage à la colle chaude des boutons des trim et navigation , les 3 câblés avec les même couleurs pour faciliter les branchements sur l'arduino
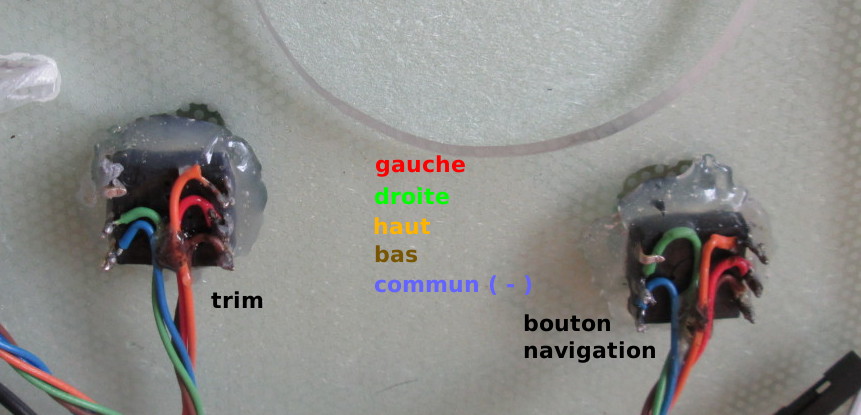
le branchement des potentiometres et des trims
pour chaque trim , les haut-bas et droite-gauche sur soudés sur 2 picots joints pour pouvoir les retourner en cas d'inversion , le fil comun bleu est aussi soudé sur 2 picots pour la résistance mécanique à l'enfichage
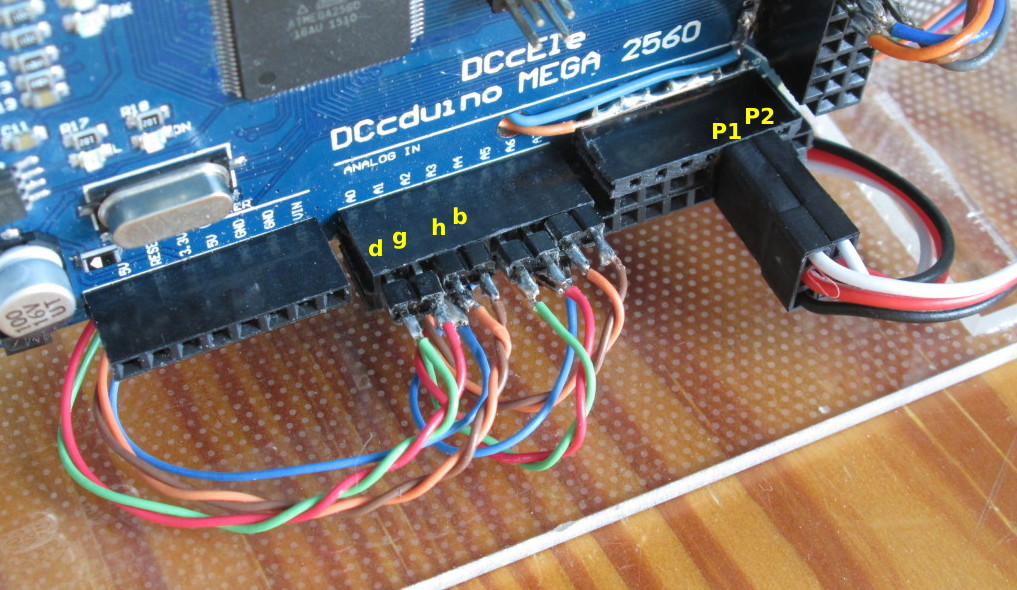
toute les " entrées " sont montées , ça commence à prendre forme <------> GAFFE ERREUR : sur cette photo aussi écran inversé " haut-bas "
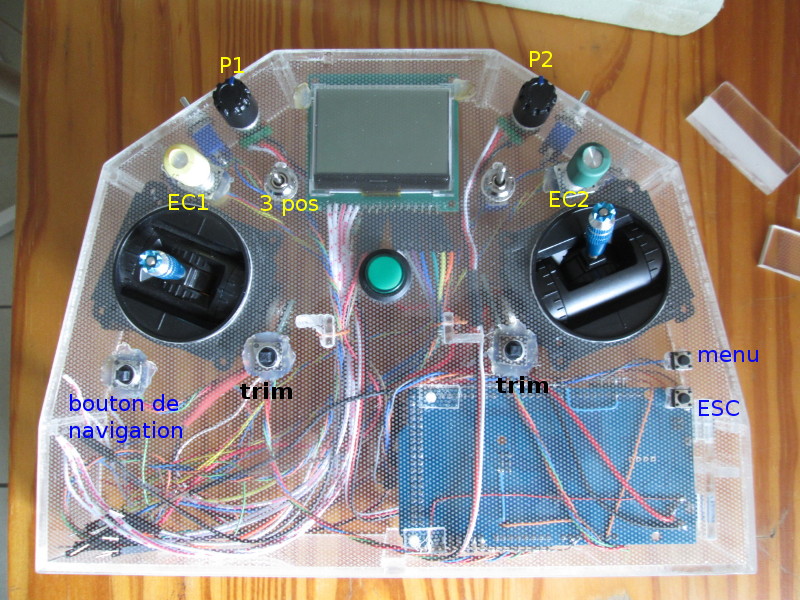
24/10/2015
ça y est..... fini , tout fonctionne au niveau du soft
il reste deux entrées disponibles non-cablées pour le moment : un potentiomètre ( le "P3" ) et le switch "TRN" ( pour celui là , j'ai vu que pour le DLG , au lancé , des p'tits gars on monté un inter momentané sur la face arrière de la radio au niveau de l'index ou du majeur .... )
en bas à gauche du boitier , l'emplacement vide est celui du futur accu , pour les essais c'est actuellement un 2S avec alim sur la prise d’équilibrage
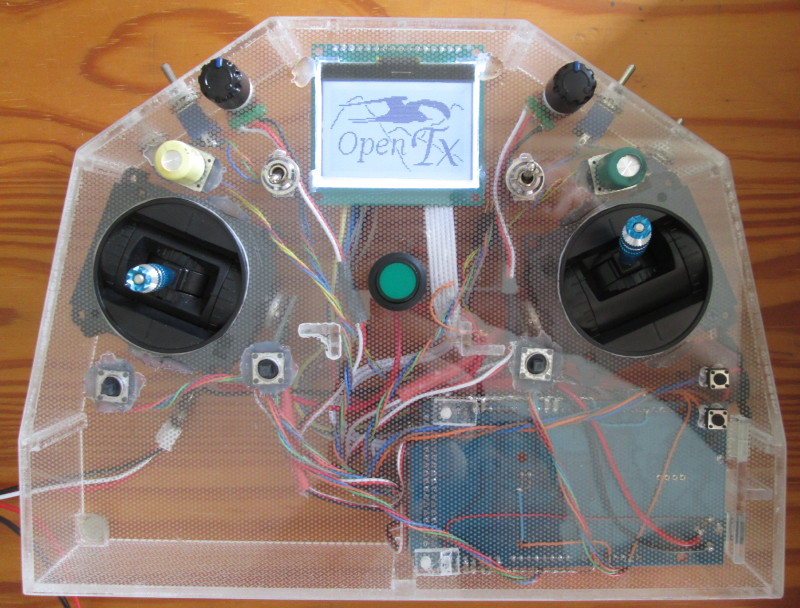
la prise avec les 3 broches apparentes est le branchement du module TX Assan qui prendra place entre la plaque de plexi et l’écran
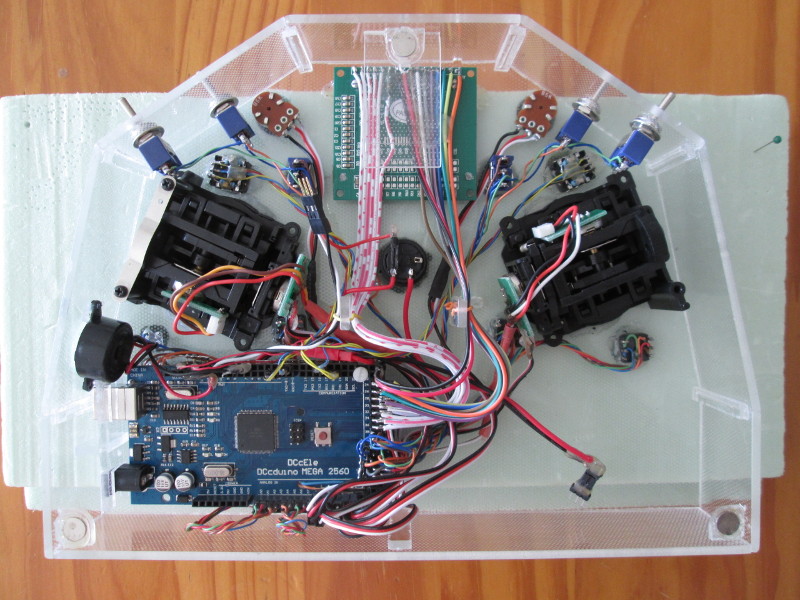
quelques photos de plus :
- le module Tx Assan est positionné sous l'écran , fixé sur la plaque transparente , antenne contre la face avant du boîtier
- pour le moment l'accu est un 3S 2200 mA de la 9XR , il sera bientôt changé pour un 2S
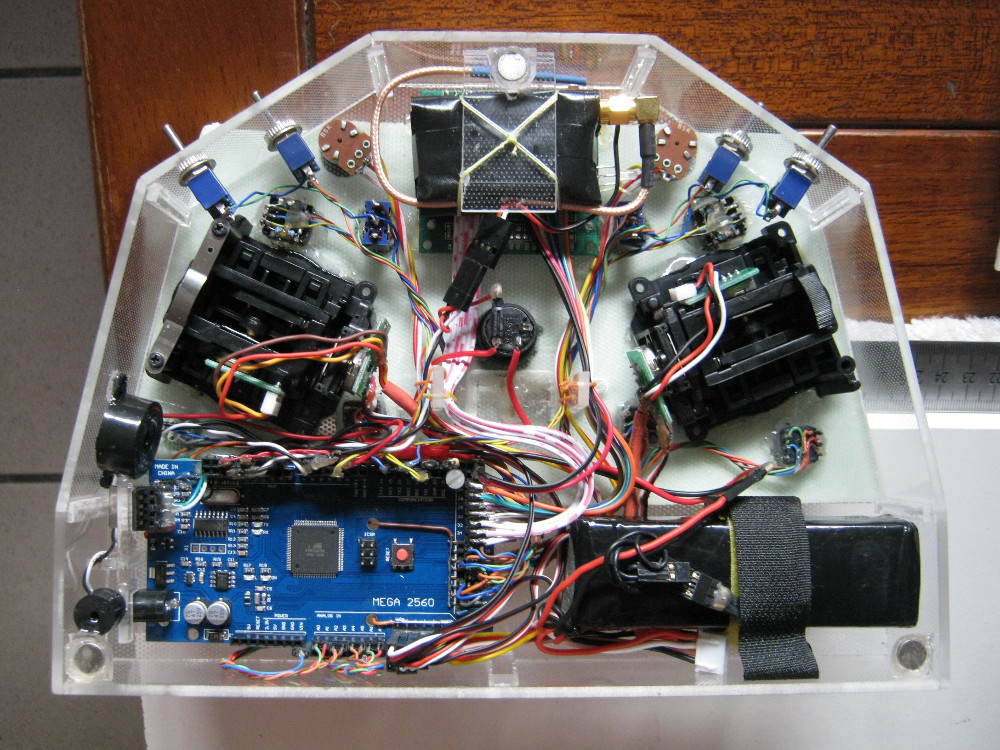
vue de l'antenne 2.4Ghz placée contre la face avant de la radio
fabriquée comme ici : http://home.nordnet.fr/fthobois/antenne 2.4GHz.htm
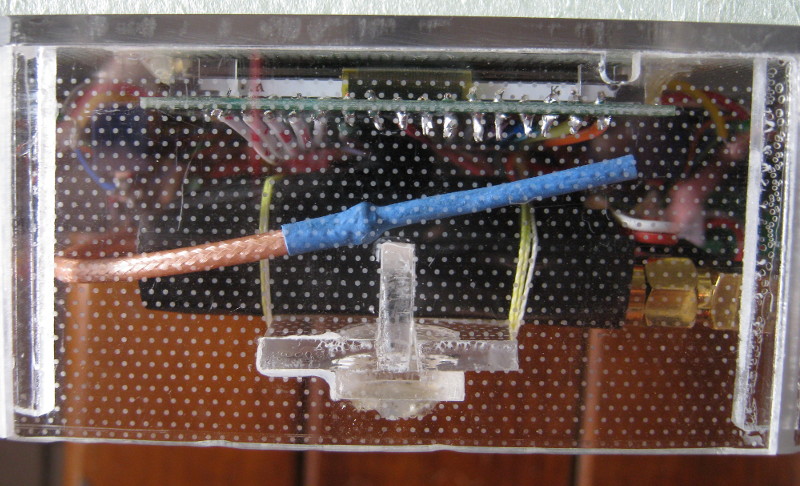
- ajout d'une prise USB collée sur celle d'origine de la carte pour ne pas sortir la carte pour les sauvegardes et mises à jour
- et un HP en 5V ( récup sur une carte mère d'ordi ) pour sortir les bips accessibles dans le menu " fonctions spéciales " , branché sans ampli , le son est un peu moins puissant que celui du buzzer mais bien suffisant
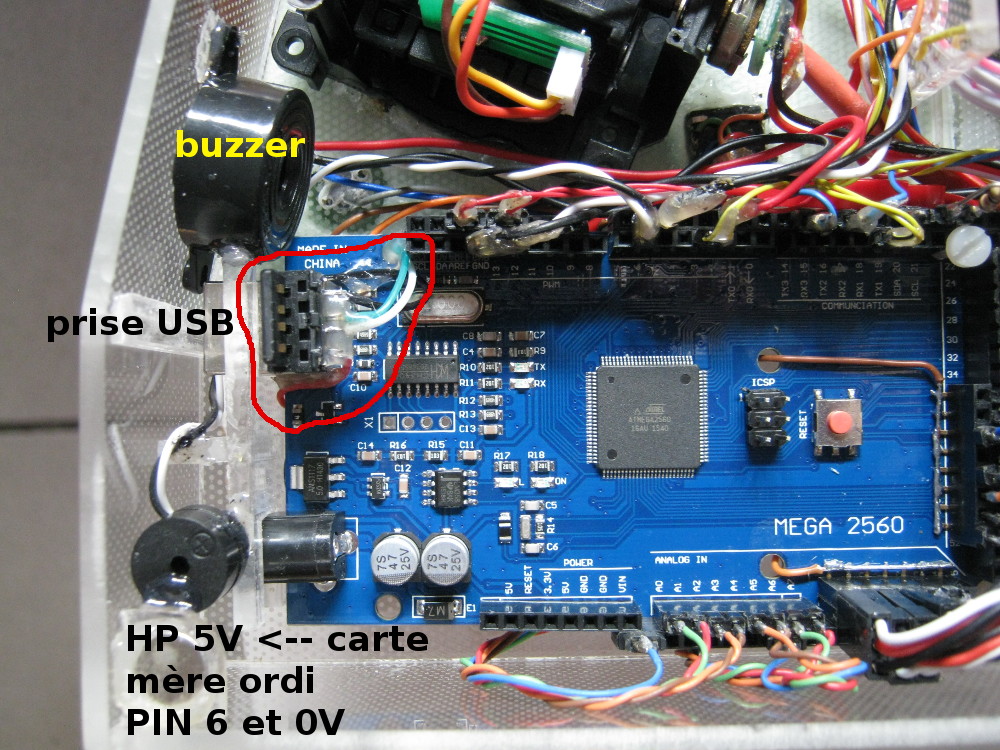
modification des boutons des encodeurs rotatifs , pour augmenter le diamètre : un bout de durit collé + gaine thermo par dessus pour l'accroche
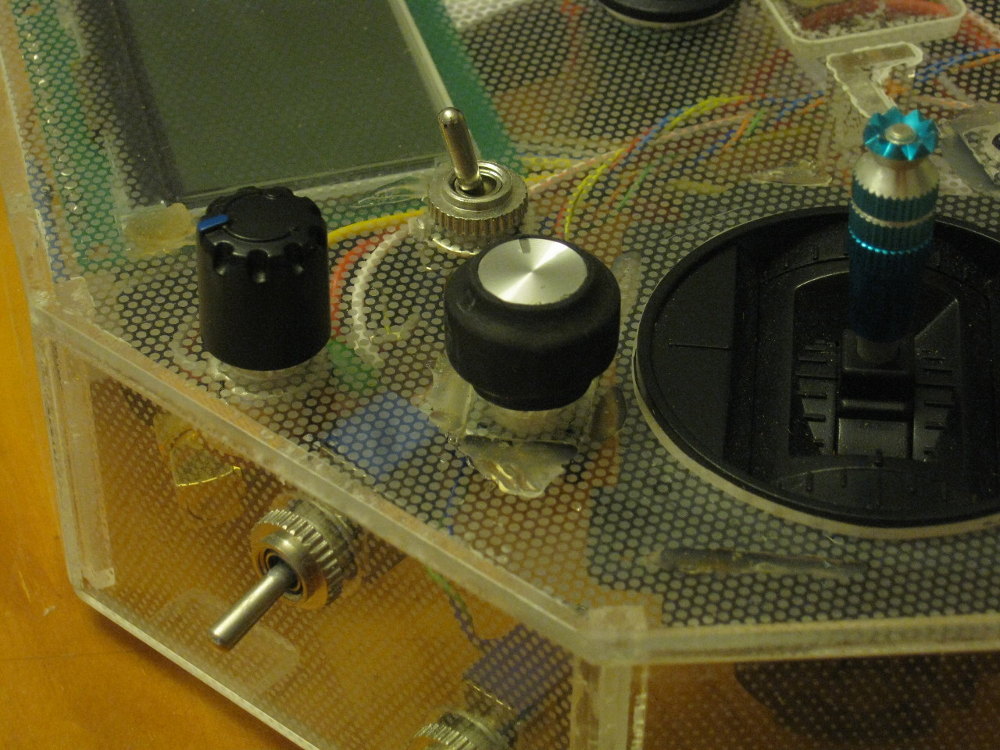
vue d'ensemble
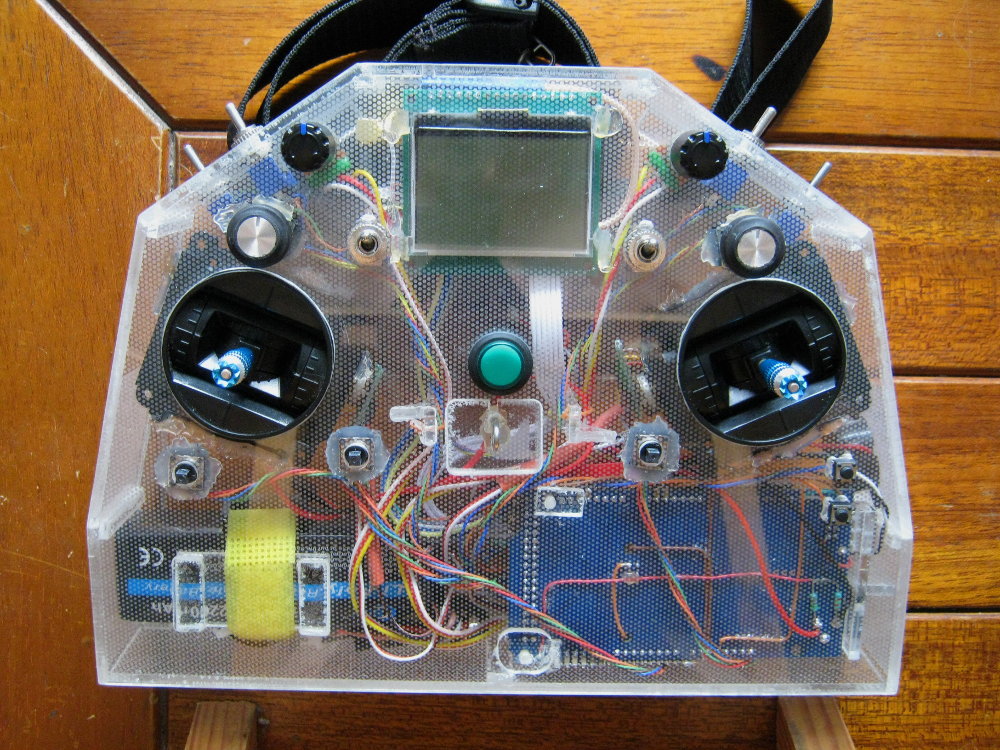
la suite : la modif des potars pour remplacement par des capteurs magnétiques
ce que ça donne
que c'est bôôôôôô
......
...... mais GAFFE : c'est vraiment très petit <----> sans être compliqué ça n'est pas simple à réaliser , il faut être minutieux , et la modif n'est pas réversible donc 'faut pas se rater
l'idée est de faire tourner le champ magnétique (lié au manche) autour du capteur (lié au châssis fixe) ..... c'est pas clair
no-stresssss : ça va venir
voilà l'idée de départ , 02 aimants en jaune collés sur un support qui génèrent un champ magnétique dans lequel est plongé le capteur ( mais au final j'ai trouvé des aimants diamétralement magnétisé percés avec les bonnes dimensions , voir plus bas )
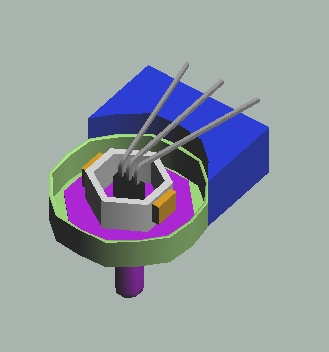
lors de la rotation du manche et de l'aimant , l'intensité du champ magnétique entrant dans le capteur varie suivant une sinusoïde …. et la linéarité ? comme les manches de la 9XR débattent de +/- 25° autour du neutre , la variation reste dans la zone quasi linéaire " en vert " de la tension de sortie / angle du manche ( pour les matheux , il y a 1.2 % de différence entre les valeurs X et SIN(X) pour 25° de débattement )
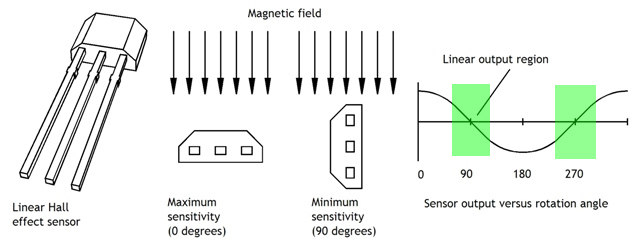
sans champ magnétique la sortie du SS495 est à la moitié de la tension d'alimentation : 2.5V ( L'arduino fournit du 5V )
quand le champ magnétique est parallèle au capteur , le champ "n'entre" pas dans le capteur , la tension de sortie est aussi à la moitié de la tension d'alimentation
quand on approche le pole Nord d'un aimant la tension monte de 2.5V vers la tension d'alimentation , quand on approche un pole Sud la tension descend de 2.5V vers 0V
le matériel utilisé et les dimensions des pièces :
du plexiglass de 3mm <<< boîtier de la radio
04 capteurs hall SS495A1
04 aimants diamétralement magnétisés 10mm ext x 7mm int x 3mm de haut
démontage du potar : déplier --- sans les casser , ça va servir + tard --- les pattes qui tiennent la piste carbone , vue sur le "peigne" qui frotte sur la piste carbone et qu'il va falloir enlever
une photo pour se faire une idée de l'usure de la piste carbone après 3 ans d'utilisation , environ une centaine d'heures / an
remarque : je n'ai pas eu de pb de faux-contacts jusqu'à aujourd'hui
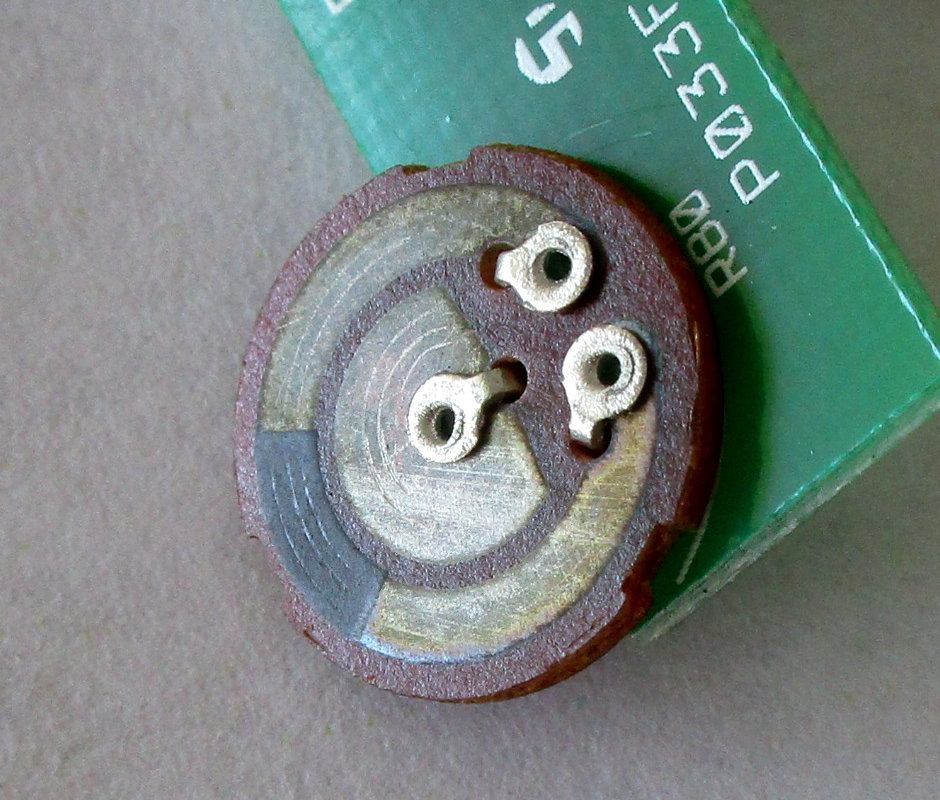
"peigne" enlevé en tirant dessus , il reste ses deux plots de fixation
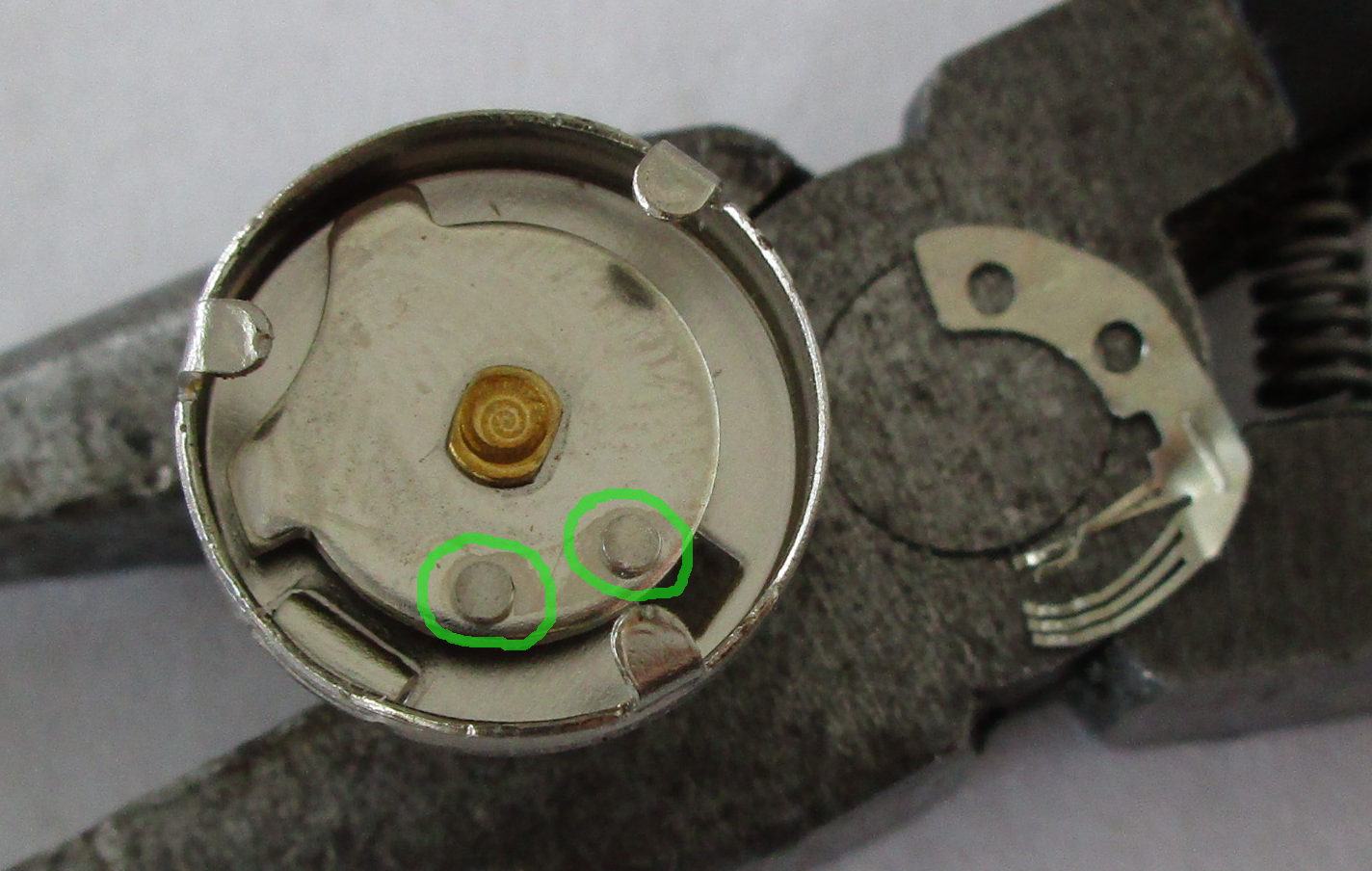
usinage des plots à la mini-perceuse et mini-fraise + rayures sur le plateau qui portera l'aimant + rayures sur un flan de l'aimant <-- collage époxy lente
collage de l'aimant , explications :
- les 03 pattes - qui n'ont pas été cassées
- servent à le tenir bien centré durant le durcissement de l’époxy sinon ce "traitre" va immédiatement se coller sur la paroi
- sur l'axe du potar il y a le méplat qui le lie au manche , il faut coller l'axe N/S de l'aimant parallèle au plan du méplat
- pour trouver le Nord et le Sud placer l'aimant sur un petit bout de dépron , déposer le tout dans une assiette avec un fond d'eau , cool , on viens de réinventer la boussole
collage d'une partie du support en plexiglas du capteur sur le potar à l’époxy , les pattes sont encore là pour renforcer le collage
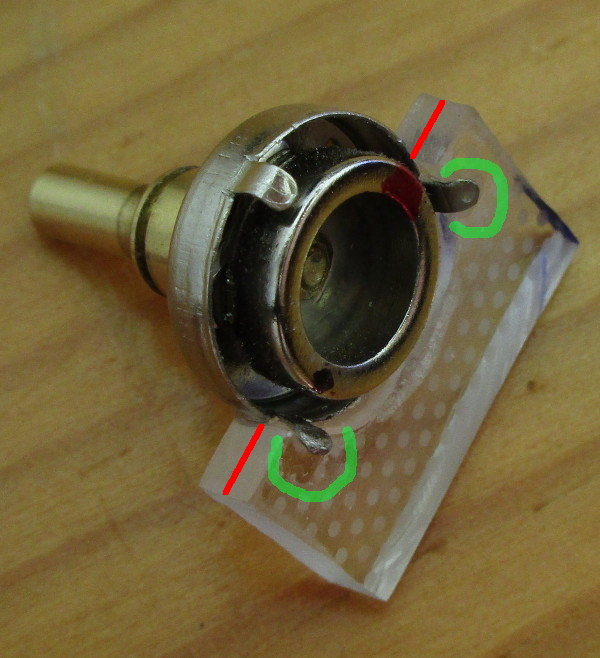
fabrication de l'autre moitié du support du capteur
soudure des 3 fils + - et signal , ligature des 03 fils au support avec un fil de cuivre pour la résistance mécanique
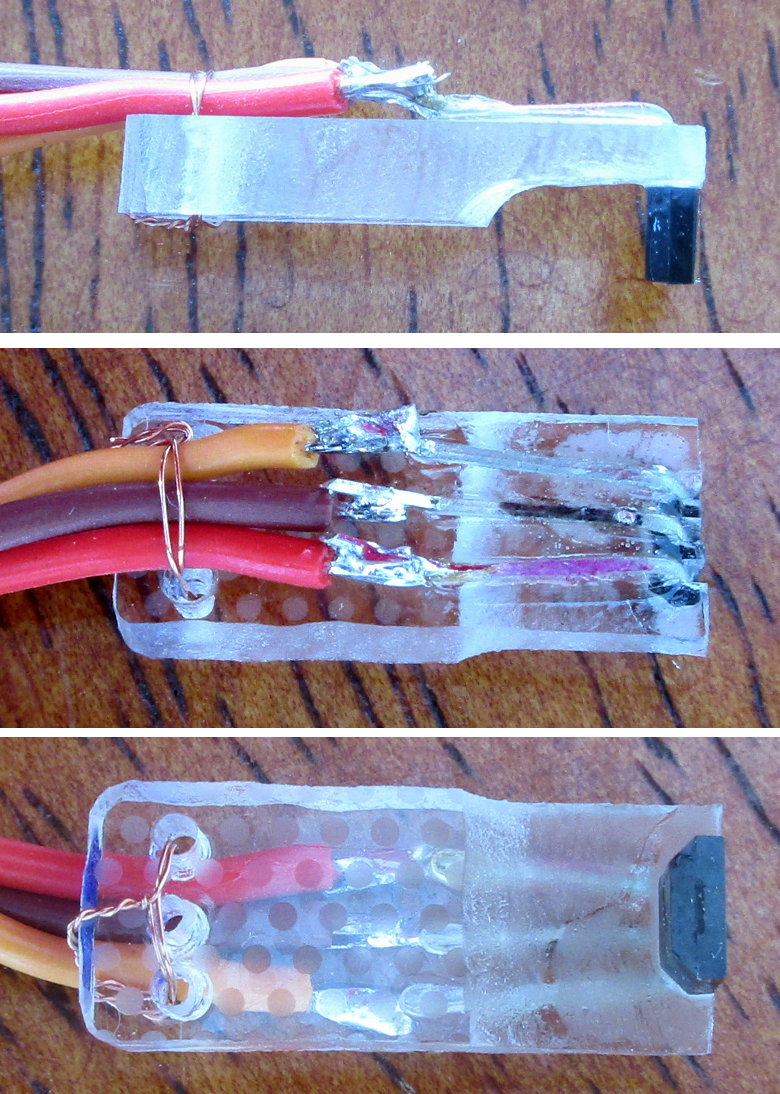
collage des 02 supports du capteur :
remonter le potar sur le manche ( ici manche Direction avec son ressort de rappel au neutre )
alimenter le capteur avec une alim 5V , mesurer réellement la tension de cette alim , puis placer le voltmètre sur la sortie signal du capteur
tout en gardant le capteur toujours au centre de l'aimant , faire tourner le "petit" support plexi pour arriver à lire exactement la tension-mesurée/2 au voltmètre
ne plus bouger , déposer une goutte d'acétone pour coller-fusionner les 02 plexi ( voir plus haut le collage du boîtier )
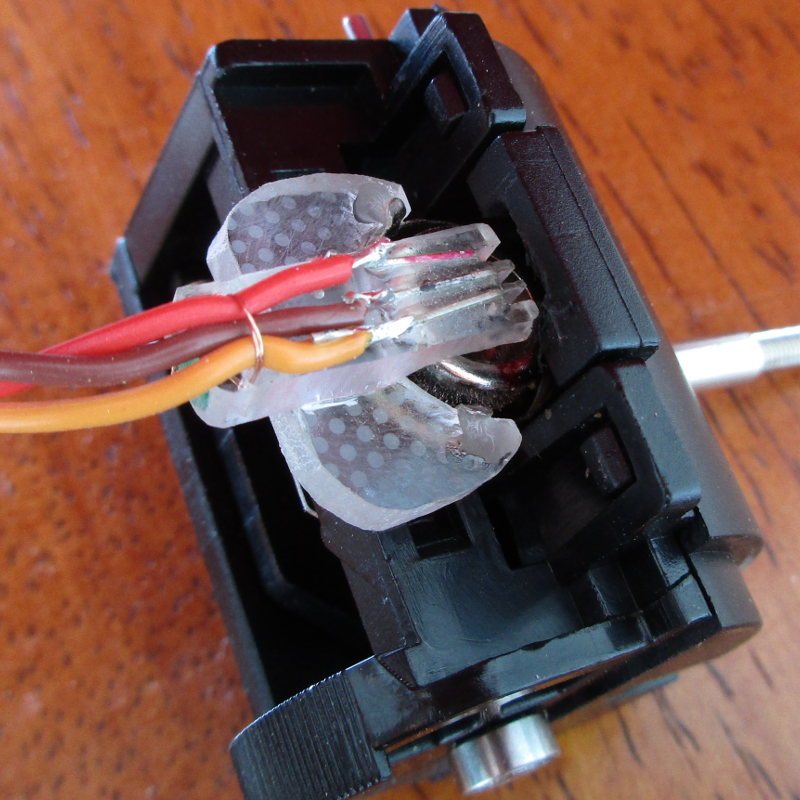
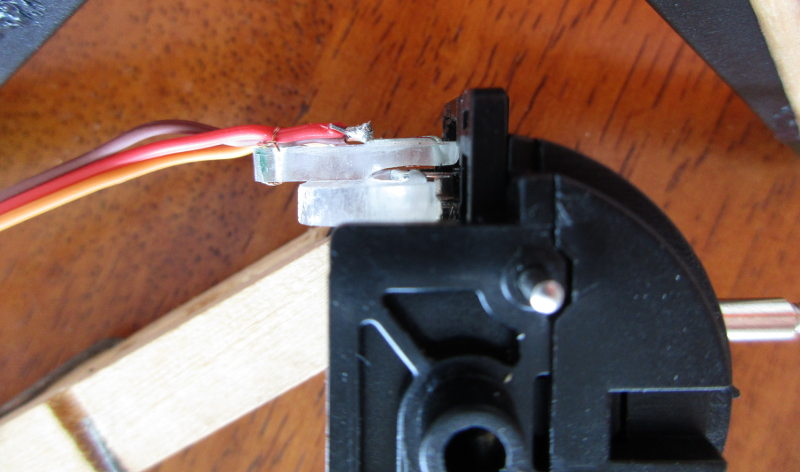
le petit plexi peut finir collé légèrement décalé pour avoir tension-mesurée/2
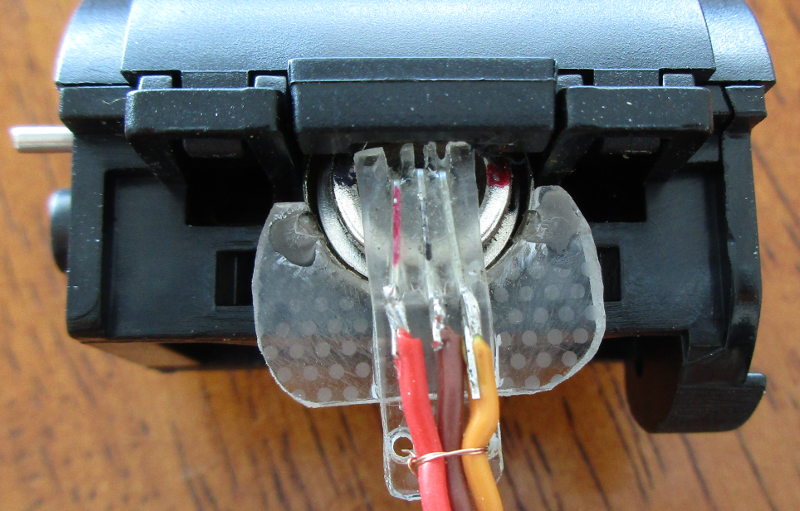
le potar de la Profondeur
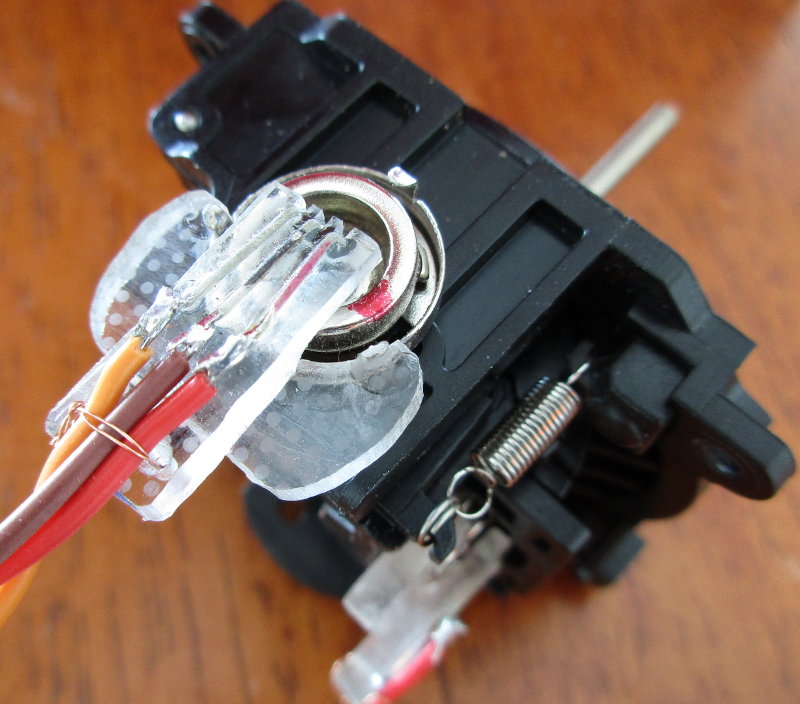
le bloc Dir Prof
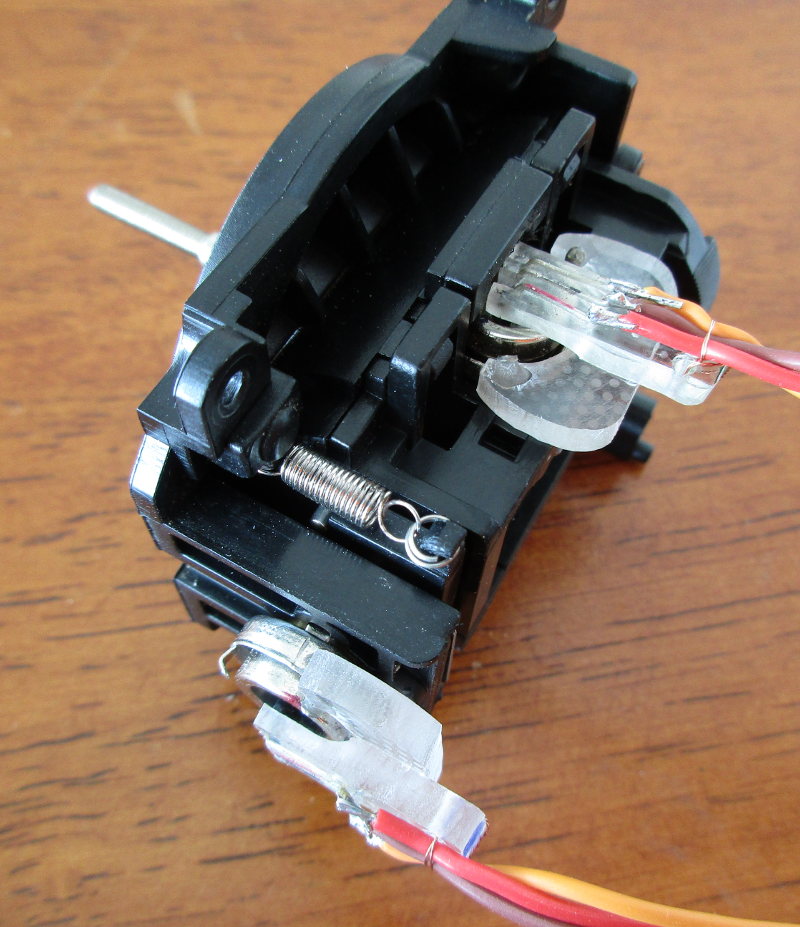
après ré-étalonnage des manches et potars , tout fonctionne nickel :
la sensibilité est excellente : entre le pouce juste posé sur le manche ou enlevé il y a une variation de 0.2 à 0.3 % à l'affichage
manche poussé en butée et ramené , la valeur revient quasi à l'identique +/- 0.1%
20/12/16
salut
suite au changement des potentiometres des manches par des capteurs magnétiques , j'ai fait quelques mesures de conso pour vérifier la doc technique des capteurs qui annonçait 7mA / capteur
j'ai pu me faire preter un multimetre pour pouvoir mesurer les petits courants ( sinon je n'ai qu'une pince ampèremetrique AC/CC , le plus petit calibre 40A , 2 décimales après le point , pas top pour la précision
)
quelques mesures :
130mA module Assan en emission + Led retro-eclairage écran allumée ( démarrage de la radio )
121mA module Assan en emission et Led écran éteinte ( tempo réglée à 10s )
76mA module Assan débranché et Led écran éteinte ( reste le Méga 2560 , 2 pot de 5Kohm et les 04 manches à capteurs magnétiques )
44mA les 04 manches débranchés
32mA / 4 : un capteur magnétique SS495A consomme donc 8mA , proche des 7mA de la doc
( + ou - la précision du multimetre )
depuis cet été la radio est alimentée avec un 2S 1100mAh , ça donne un peu plus de 8H d'autonomie
A+ bons vols
02/2019 une autre modif ....
---> avant de me lancer là dedans , j'ai essayé de "lire/comprendre" le code NextStepRc pour essayer de voir comment fonctionnent la partie relative aux encodeurs rotatifs , après avoir trouvé " quelques lignes " en rapport avec ces derniers , je dois dire que bien comprendre pour pouvoir modifier sans tout casser n'est pas à ma portée
remplacer les encodeurs rotatifs par des switch doubles
il y avait ça sur ma MX16S , il me semble que c'est plus simple de juste lever ou baisser un petit levier plutôt que de faire tourner un axe <--- ça n'engage que moi
il y en a dispo dans le commerce du genre trim de taranis facile à trouver sur le net , mais ici , à mayotte , livraison et délai
...
donc fabrication en plexiglass pour l'intergrer au boitier transparent :

les deux switchs ( 1 commun , 2 contacts ) sont fixés à la colle chaude
en place en haut du boitier , le carré de plexi bouche l'emplacement de l'ancien encodeur rotatif
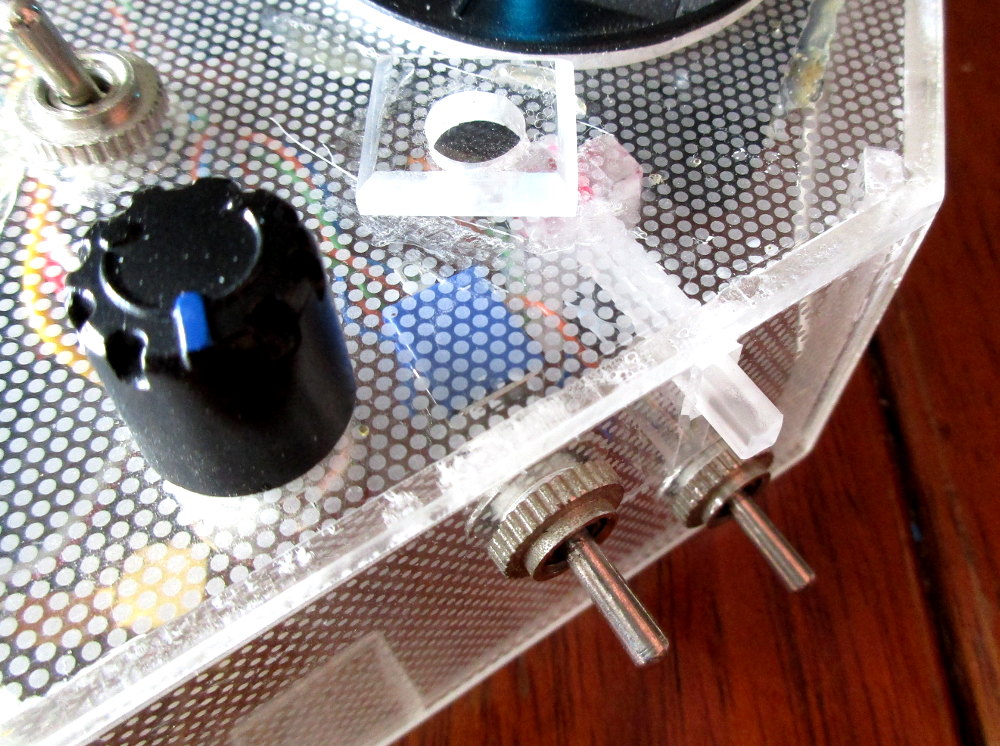
vu dans le boitier :
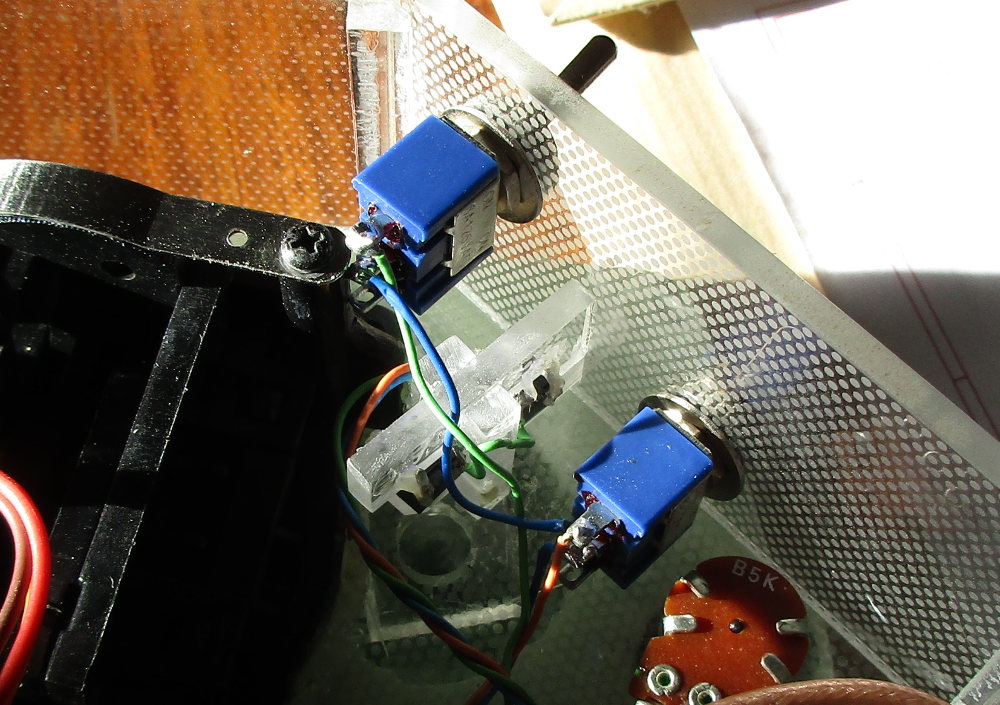
évidement pour replacer les Encodeurs par des switchs , il faut "transformer" les appuis sur les switchs en signal similaire/simulant celui des Encodeurs Rotatifs , un petit arduino attiny85 fera le bouleau
comme il n'y a plus de cran/pas de l'encodeur , un buzzer signalera les appuis , un appui bref incrémente/décrémente d'un " pas+bip " , l'appui maintenu = environ 8 à 10 " pas+bip " / seconde
ne pas tenir compte des 1er doubles-switchs qui étaient trop gros pour loger entre les éléments déjà présents dans le boitier.....
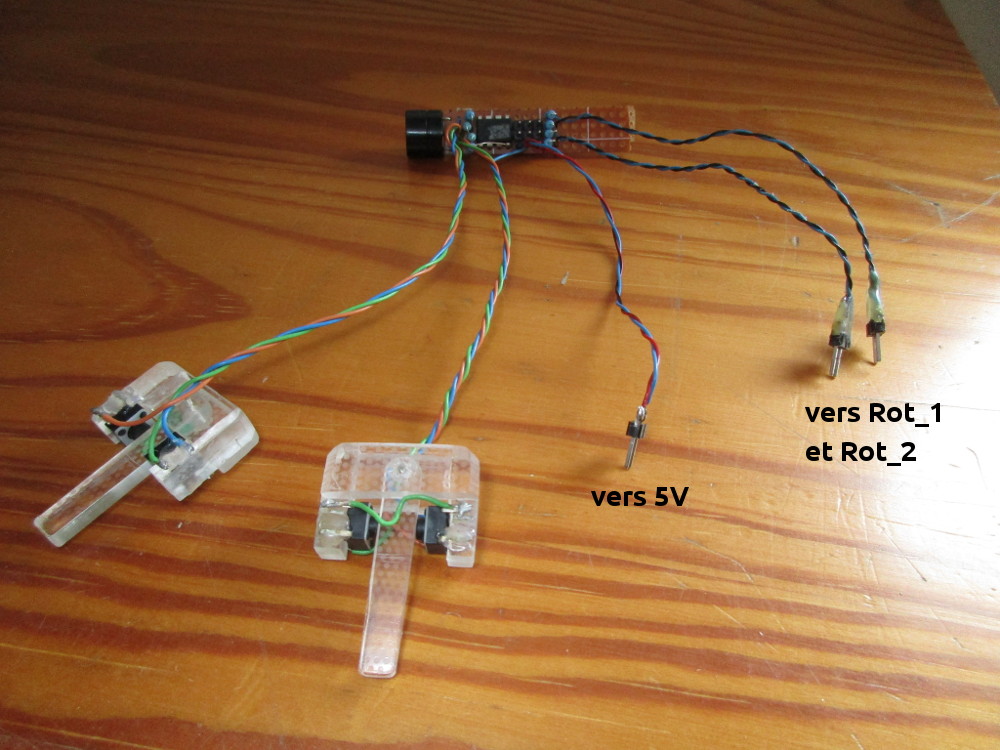
les 06 picots à droite du attiny85 servent à la programmation ( on peut s'en passer avec un support CI , pour la prog sur un support externe mais je n'avais pas )
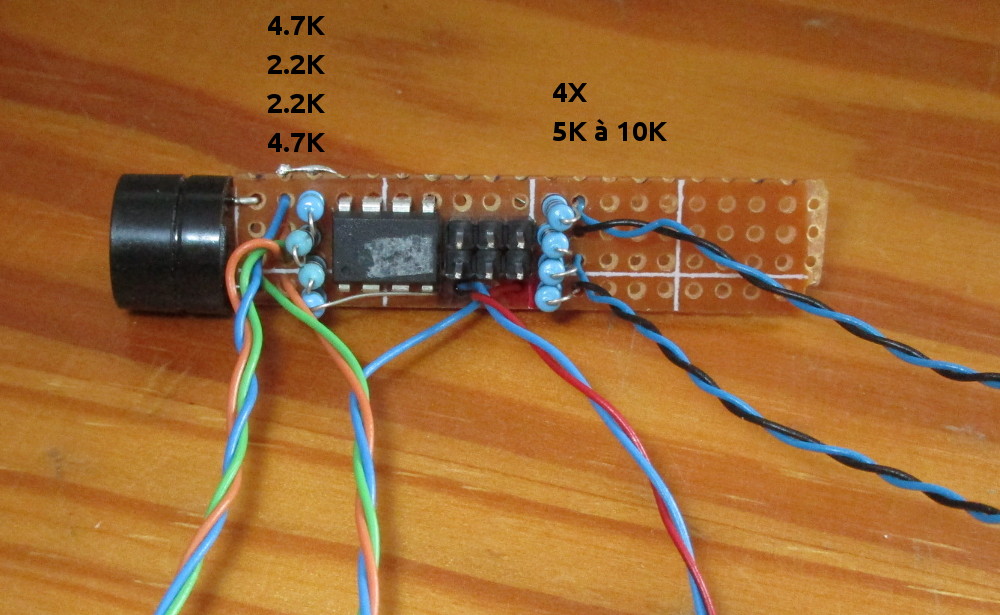
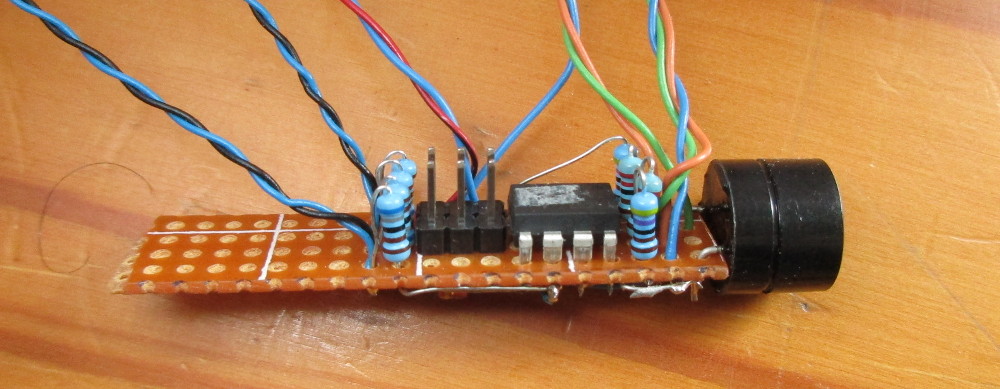
fait à l'arrache... voilà le schéma de principe utilisé :
les traits verts représentent le couplage mécanique entre 02 switchs = montés en vis à vis dans le même bloc de plexiglass
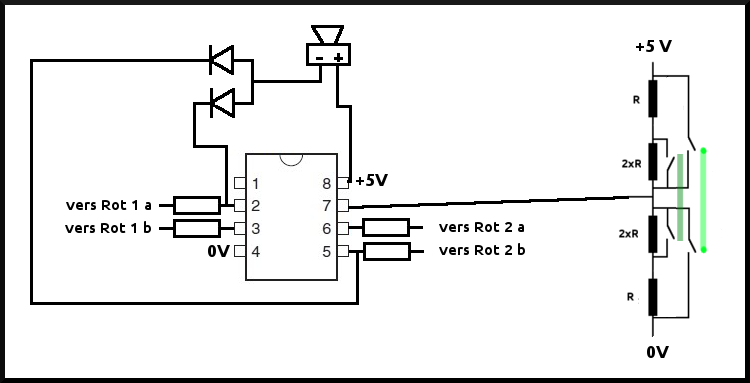
si ça intéresse du monde je ferai un copié-collé des quelques lignes de code pour l'attiny85
dès que je trouve un peu de temps , je poste une vidéo du fonctionnement ----> https://www.dailymotion.com/video/x725pqz
25/10/20
un "repère physique" sur le centre du manche des gaz :
- perso je pilote un moto-planeur en séparant en 3 zones la course des gaz : (voir plus bas )
zone supérieure = sortie AF ou relevé aileron en proportionnel
zone inférieure = courbure en proportionnel
zone centrale = tout en "lisse"
+ démarrage/arrêt moteur sur un inter temporisé
- valable sur une radio dont on peut ouvrir le boîtier facilement/rapidement sur le terrain pour passer du pilotage avion/ multicoptere vers moto-planeur et inversement
un peu de pliage
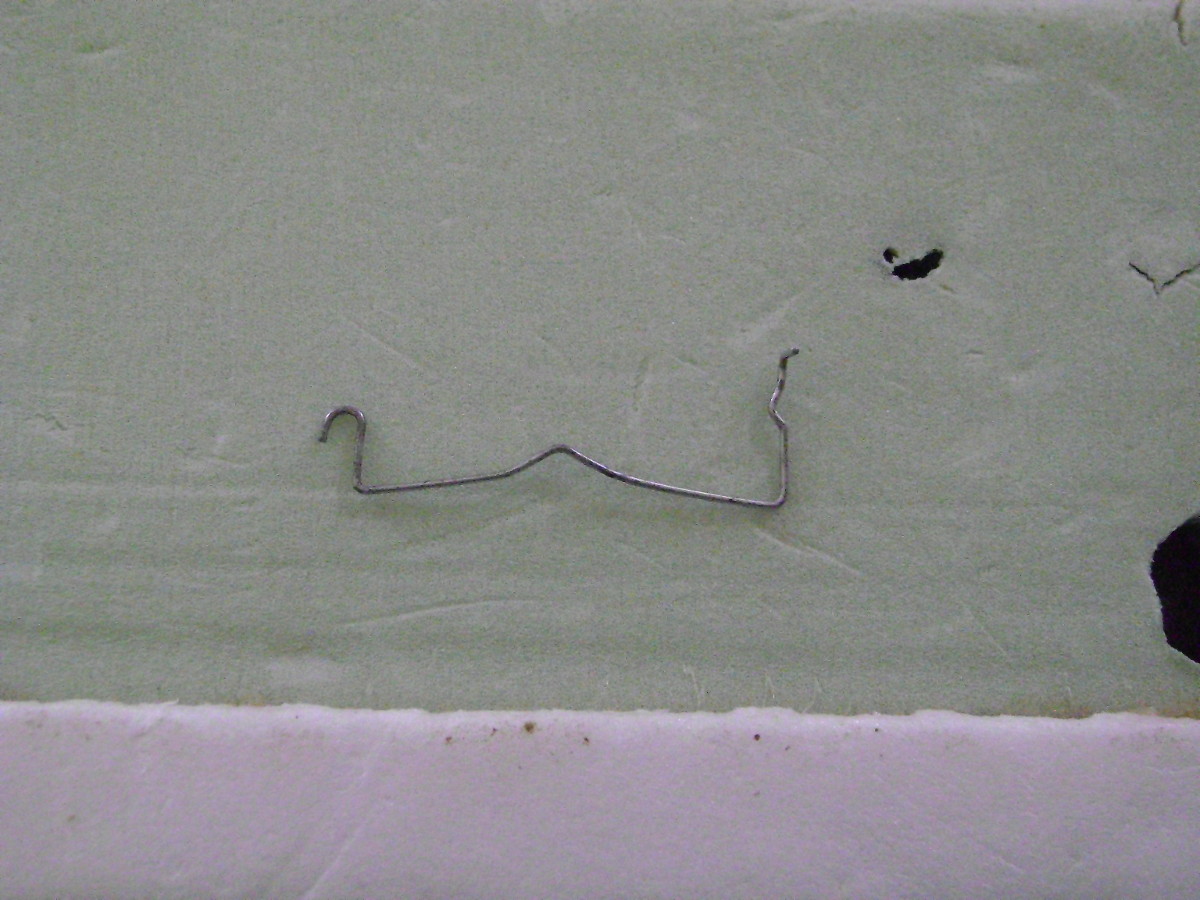
à la lime : une petite encoche au centre et sur le côté ( pas sur le dessus )
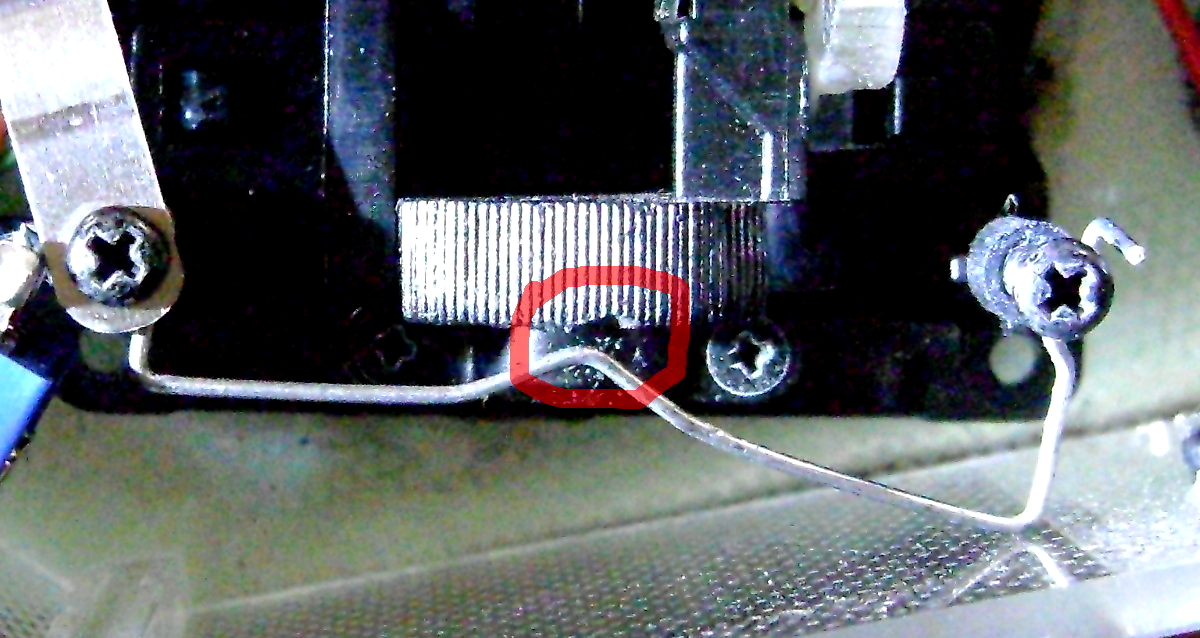
d'un doigt on passe de la position avion ( manche libre ) à la position moto-planeur ( manche avec repère physique central )
désolé pour la définition du GIF animé
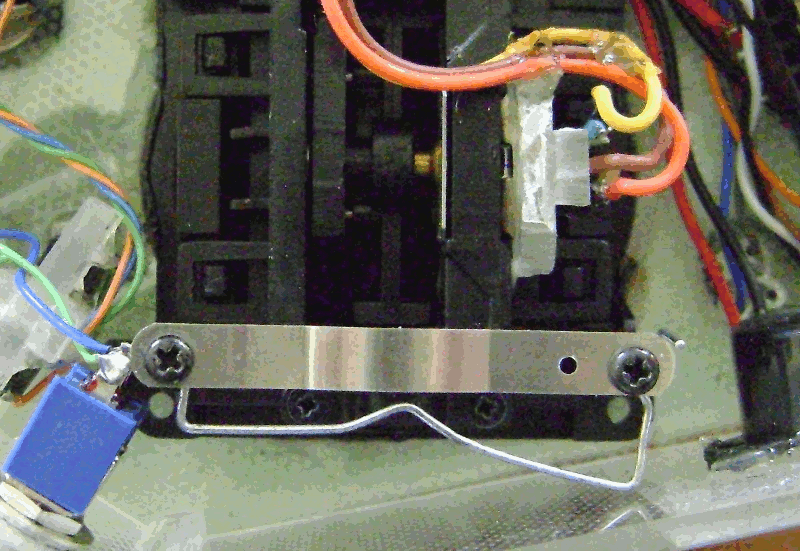
le principe de la prog du manche de gaz et du switch moteur temporisé
+ le trim de gaz qui permet d'ajuster la puissance entre 60% - à la pente - et 100% - en plaine -
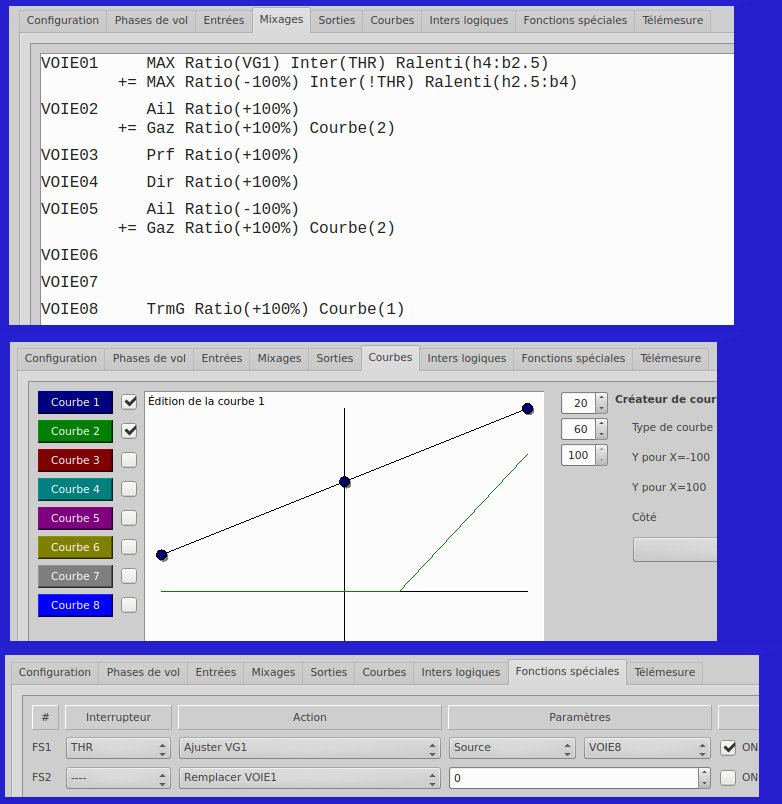
A+ bons vols
tout est parti du Mmag de Juin 2015 et de ce post : NextStepRC : radio OpenTX DIY (MMag juin 2015)
utilisateur convaincu d'OpenTx depuis 3 ans , j'ai commandé le kit NextStepRC chez cncfilchaud
étant sur Mayotte , je ne récupère le kit ( + quelques options perso ) que dans quelques temps lors de mon passage en métropole et vu qu'il y a le boîtier en bois en " rescue " dans le kit , j'ai commencé un boîtier plexy
à s'y mettre , autant le faire aux dimensions perso " kivonbien " :
angle des bras
taille des mains
angle des manches
positions des inters - potars - encodeurs rotatifs par rapport à la longueur des doigts
épaisseur du boîtier...… ( au final : 43mm )
après quelques essais découpés dans du carton voilà les dimensions finales
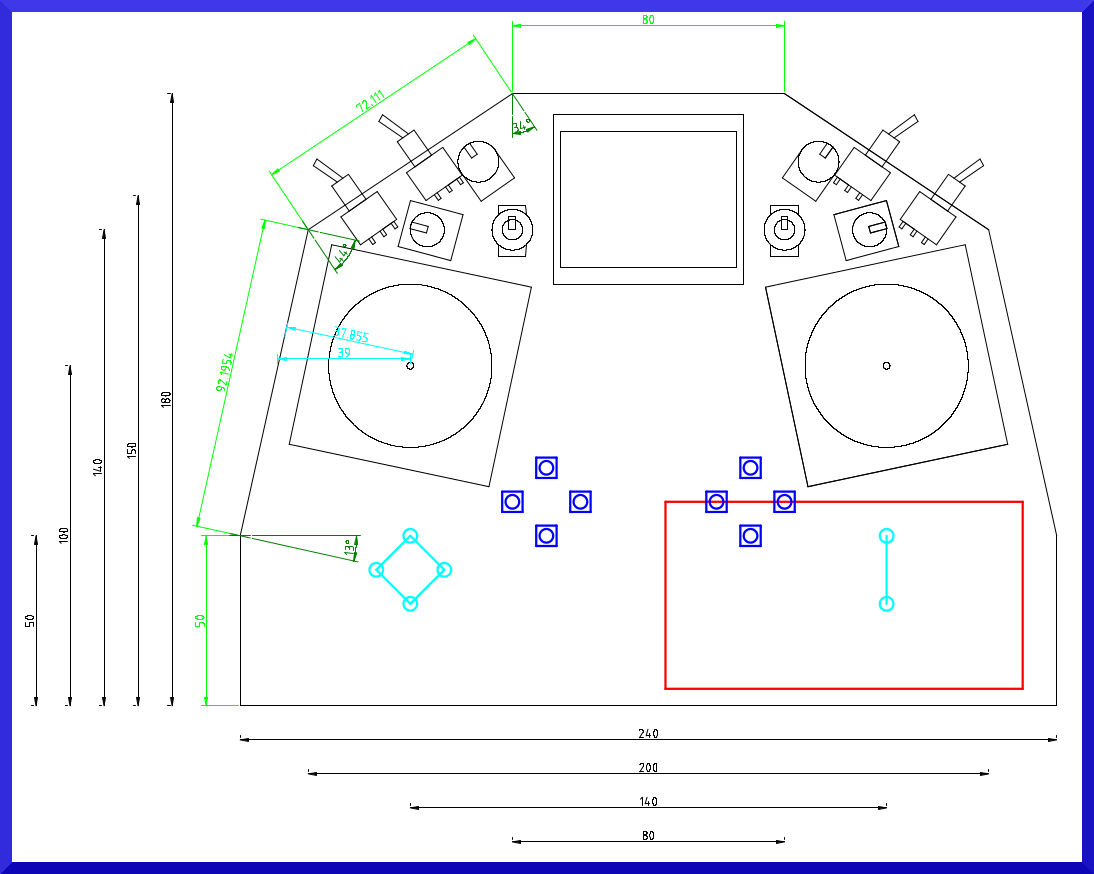
le Plexi de 3 mm est récupéré en démontant un écran LCD de Télé HS
vu sur des sites d'aquariophilie et de tuning PC ( boite pour le water-cooling ) , le plexi se colle au chloroforme………..
-----problèmes :
- il faut une ordonnance
- trouver une pharmacie qui en a encore ( surtout ici sur Mayotte )
- il semblerait que ça soit un poil dangereux à manipuler ( vu sur wikipédia , visiblement , on est pas dans un film ... )
- le + gênant : éventuellement finir endormit la tête dans le plexi

du coup , test à la cyano , ça colle mais c'est pas super costaud , et surtout ça laisse des traces blanches à l'évaporation du solvant
plus facile à trouver : l'acétone , ça fond les parties en contact = c'est costaud , par contre la préparation des pièces avant collage demande du temps et il ne faut pas se louper en déposant la goutte d'acétone sur la jonction
découpe des pièces à la Dremel - enfin , une mini-perceuse... - avec l'accessoire Dremel "kivabien" et une cornière en alu en " L " pour guide
il faut faire des tests pour trouver le bon compromis vitesse de rotation / vitesse d'avance par rapport à l'épaisseur du plexi : si la fraise force trop et-ou tourne trop vite , elle chauffe , le plexi fond , forme une "bourre" qui s'y colle et encrasse la fraise
le plexi est posé sur une plaque de polystyrène pour que la fraise traverse
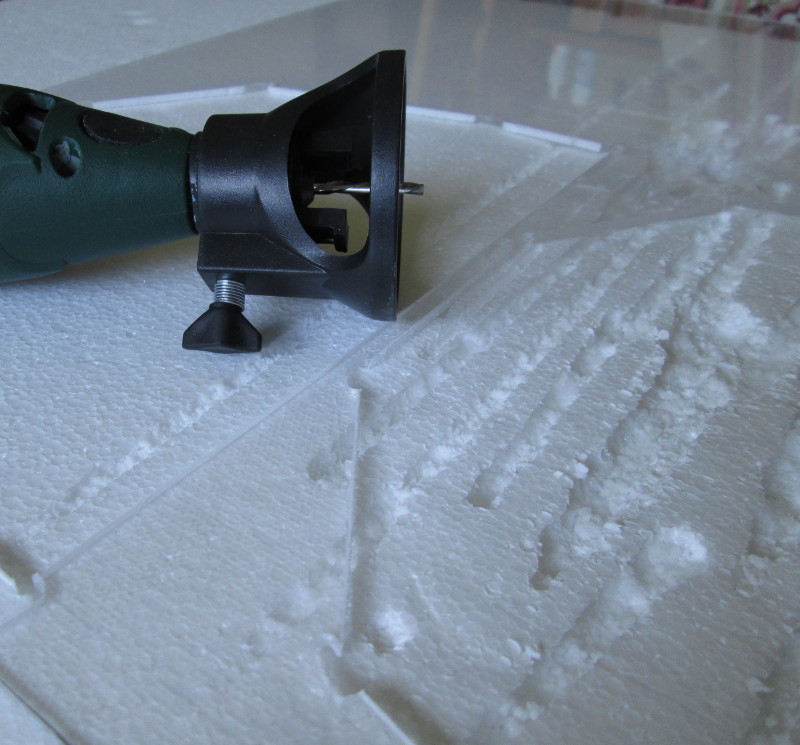
usinage à la main + dremel des évidements circulaires pour les manches : prévoir un " certain temps "
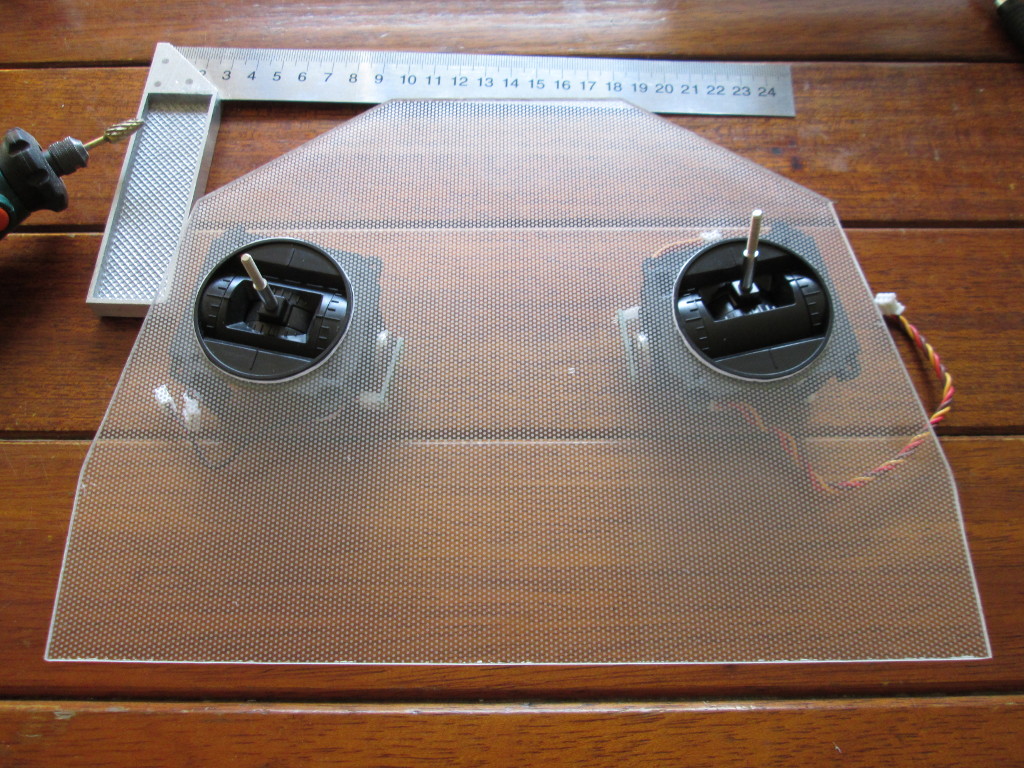
il faut préparer les pièces à réunir : le " collage " à l’acétone ne remplit pas les interstices , ça fait fondre localement les deux surfaces qui fusionnent
donc les deux pièces à joindre doivent présenter une surface en contact 100 % plane et très lisse pour être la plus grande possible
--> ponçage des champs au gros papier de verre posé sur une vitre jusqu'à arriver contre le tracé puis au papier très fin toujours posé sur une vitre , là , c'est long mais indispensable
il n'y a pas de n° sur mon papier de verre fin mais c'est celui utilisé en dernier pour la finition des gel-coat bateaux , il doit y avoir des équivalents chez Brico au rayon carrosserie
- caler les pièces avec du scotch <---> ne pas tenir à la main sinon ça va bouger vu le temps de séchage
- poser une goutte d'acétone pile-poil sur la jonction , si les pièces ont été bien poncées , on voit bien l'acétone qui se répand par capillarité entre les deux surfaces
>>> si une goutte tombe sur le plexi , c'est le drame
aucune idée du temps de séchage – évaporation - fusion , j’attends 10 min environ avant d'enlever le scotch , ça tient
là c'est un des mes nombreux essais sur des chutes , la goutte d'acétone est déposée avec une seringue
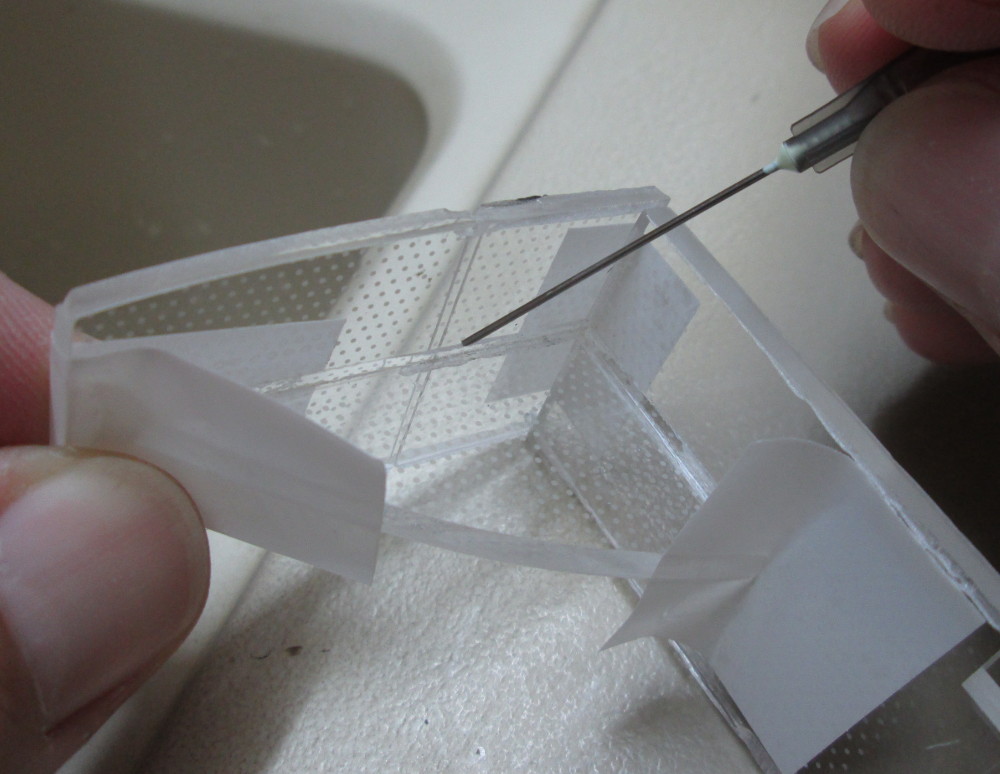
quand les surfaces en contact sont bien planes et lisses , la jonction devient quasi-transparente , les deux pièces " fusionnent " , la partie non-soudée est le futur passage du coaxial de l'antenne
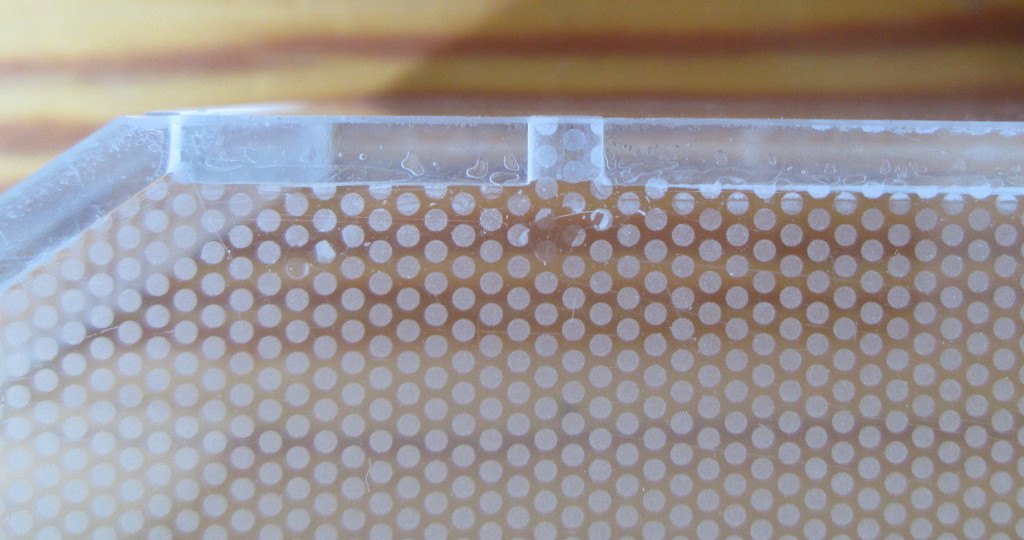
voilà le boîtier qui prend forme
évidement , il faut aussi poncer finement et aux bons angles les parois latérales pour qu'elles s'ajustent avant collage , là aussi prévoir un " certain temps "
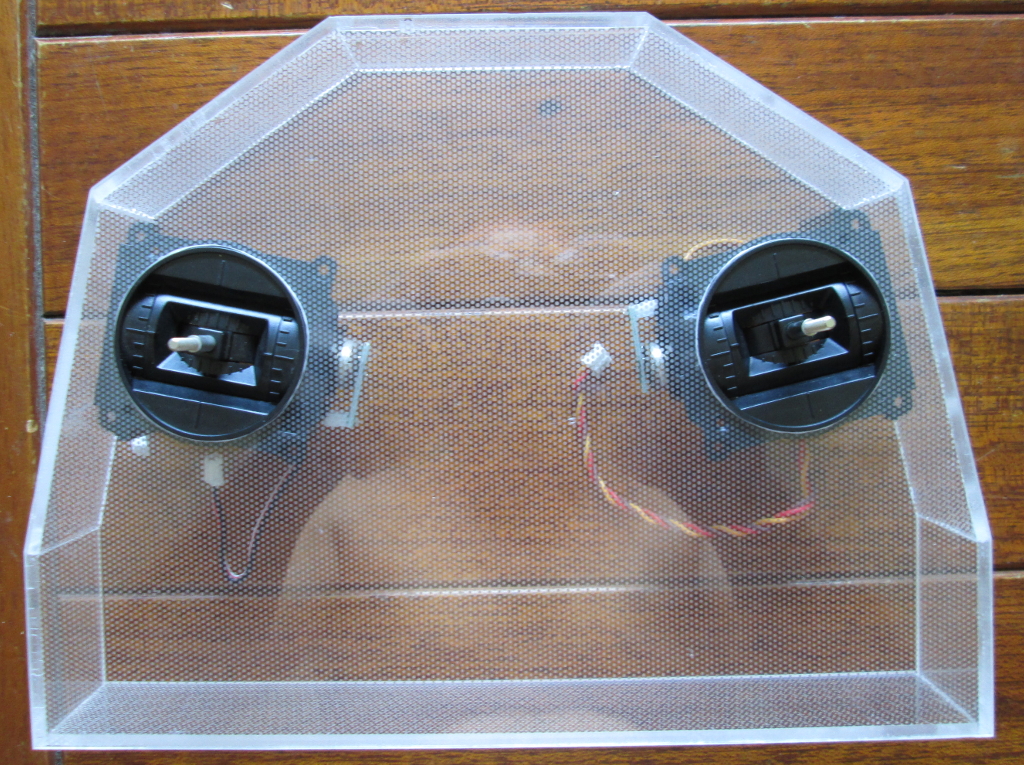
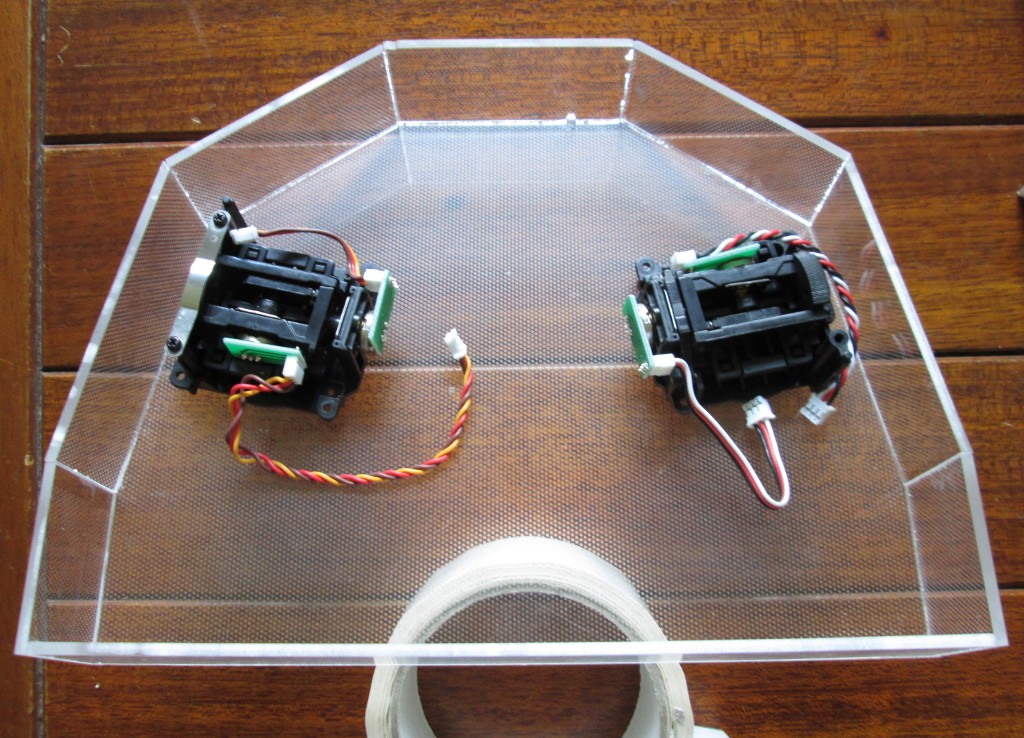
collage de 4 pièces qui font renfort aux angles + cales de hauteur pour le fond du boîtier qui rentrera dans le cadre
là aussi : ponçage aux bons angles avant collage
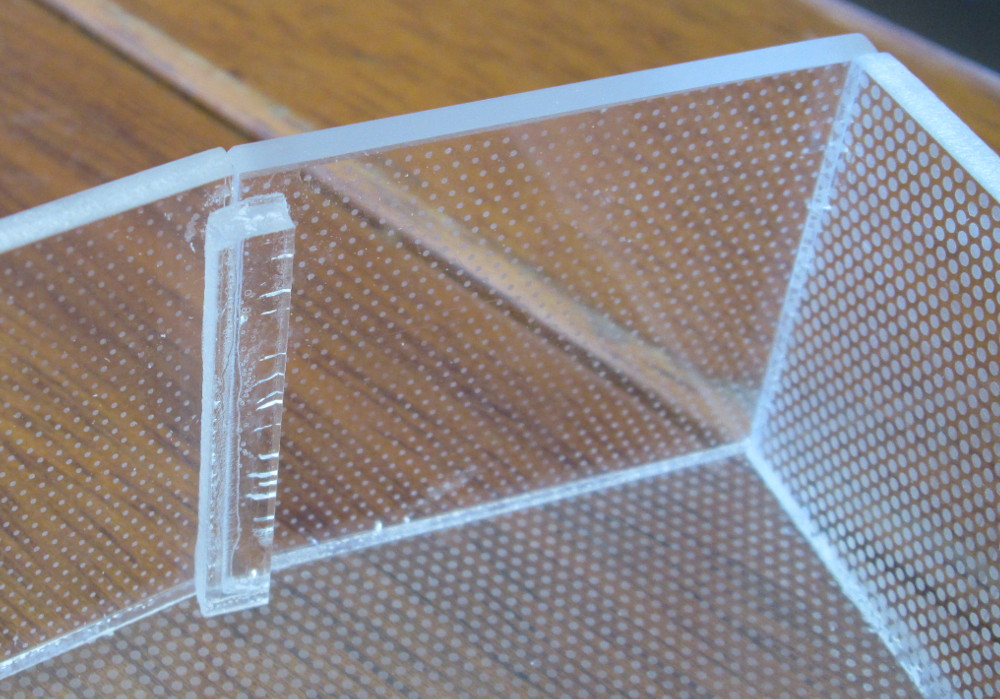
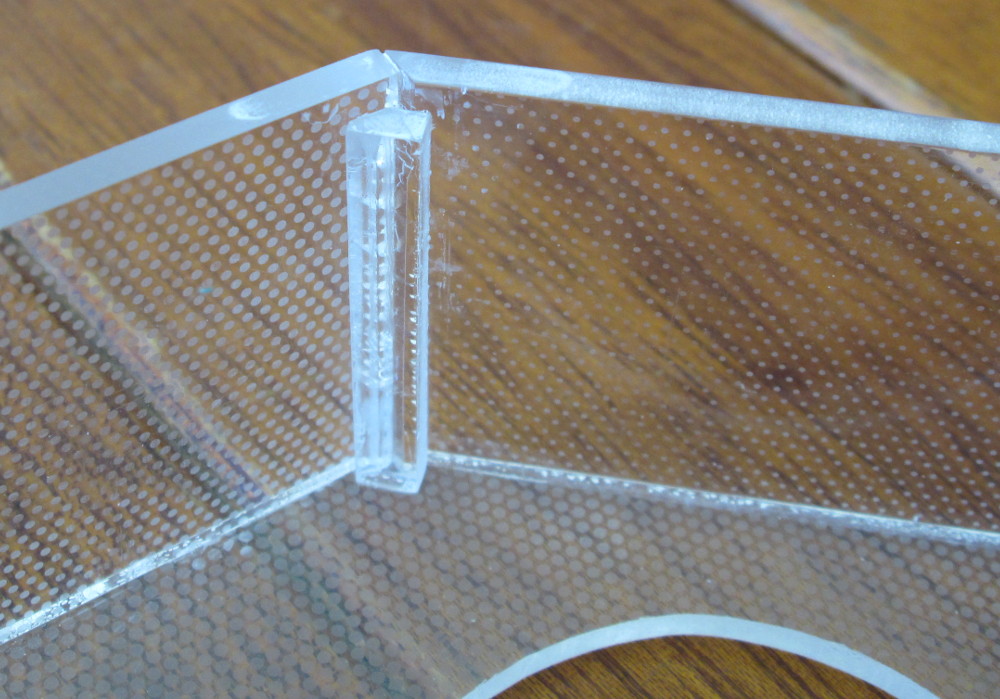
le fond est tenu par 3 paires d'aimants de 10mm de diamètre collés au pistolet à colle chaude
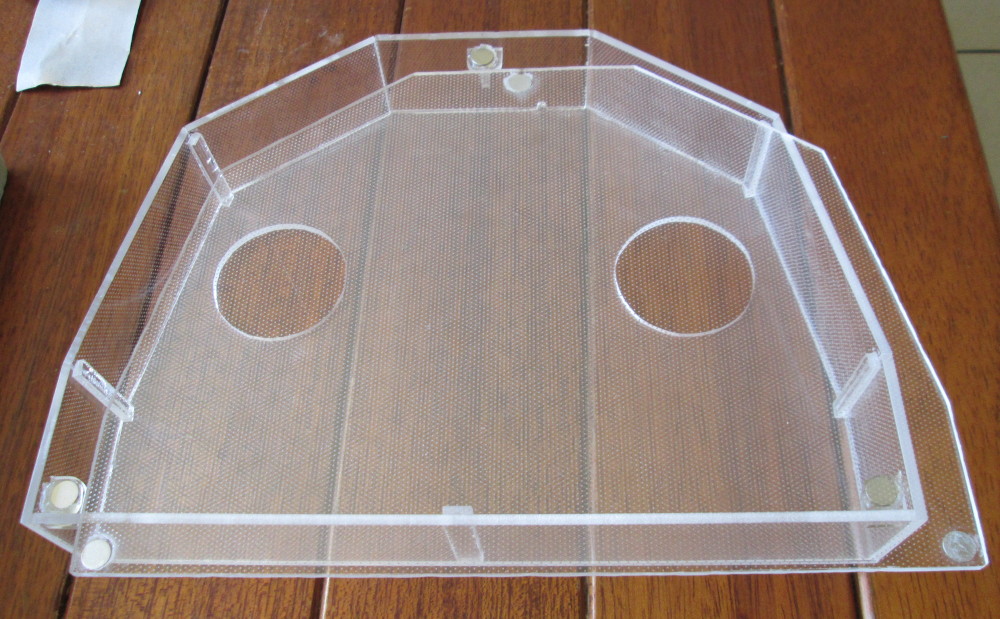
celui du haut
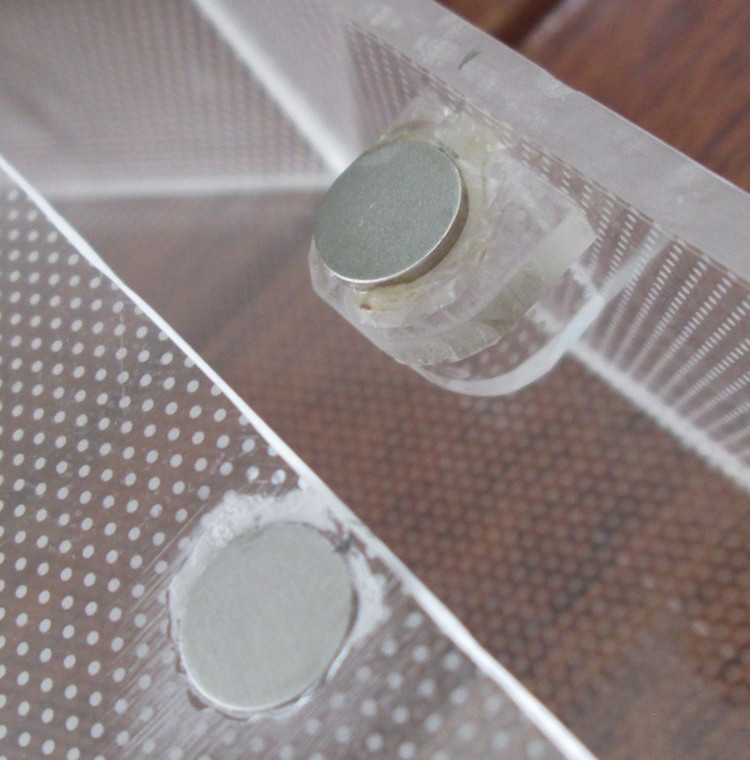
et en bas
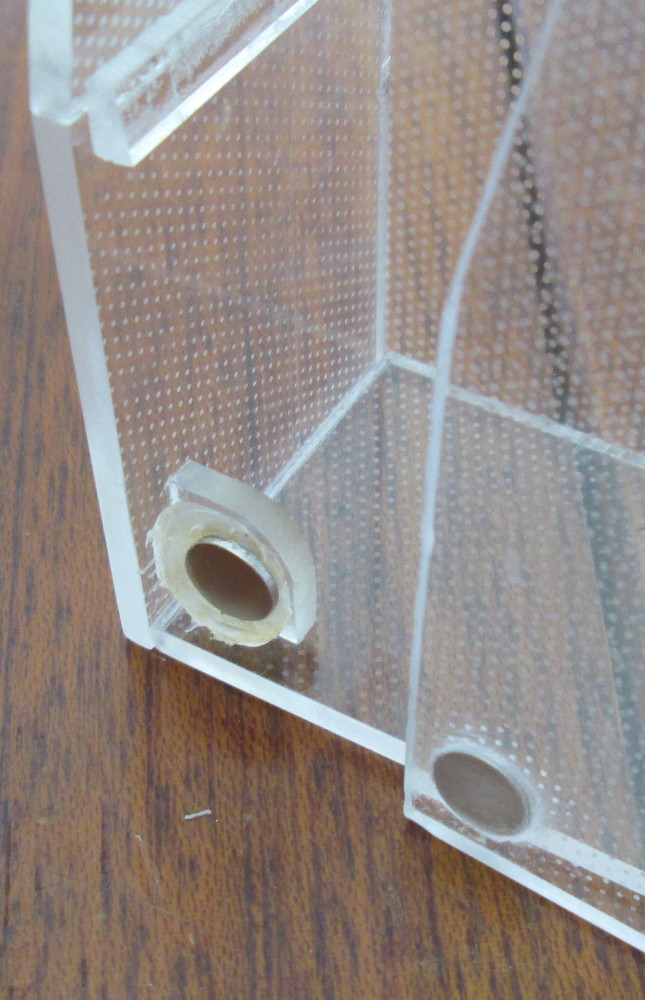
les inters et potars sont en place
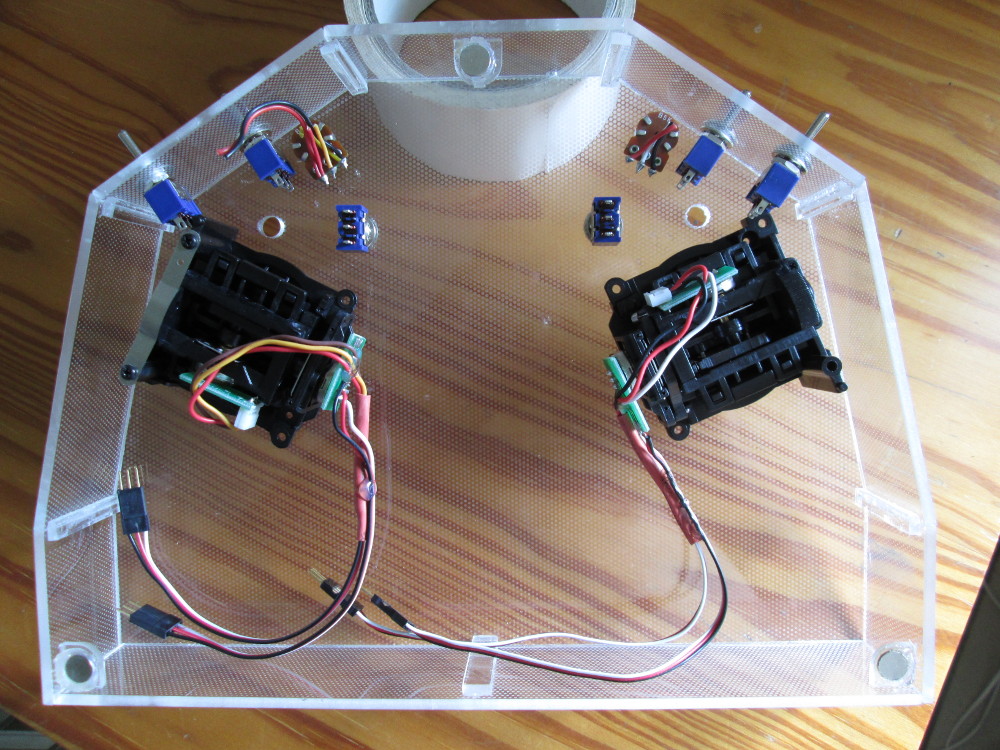
toutes les soudures sont faites sur place pour avoir direct la bonne longueur de fil --------> 'faut pas glisser avec le fer à souder ou faire tomber une goutte d'étain
le câblage des manches et potars est fait avec les rallonges de servos : sur la prise , le fil rouge central est soudé à la patte « curseur » = s'il faut inverser le sens de rotation à la 1ère mise en route , il suffira de faire "demi-tour" à la prise
comme signalé dans le post NextStepRC , en dé-torsadant les fils des potentiomètres aileron et dérive , le mouvement des axes gagne beaucoup en souplesse = un retour au neutre + précis
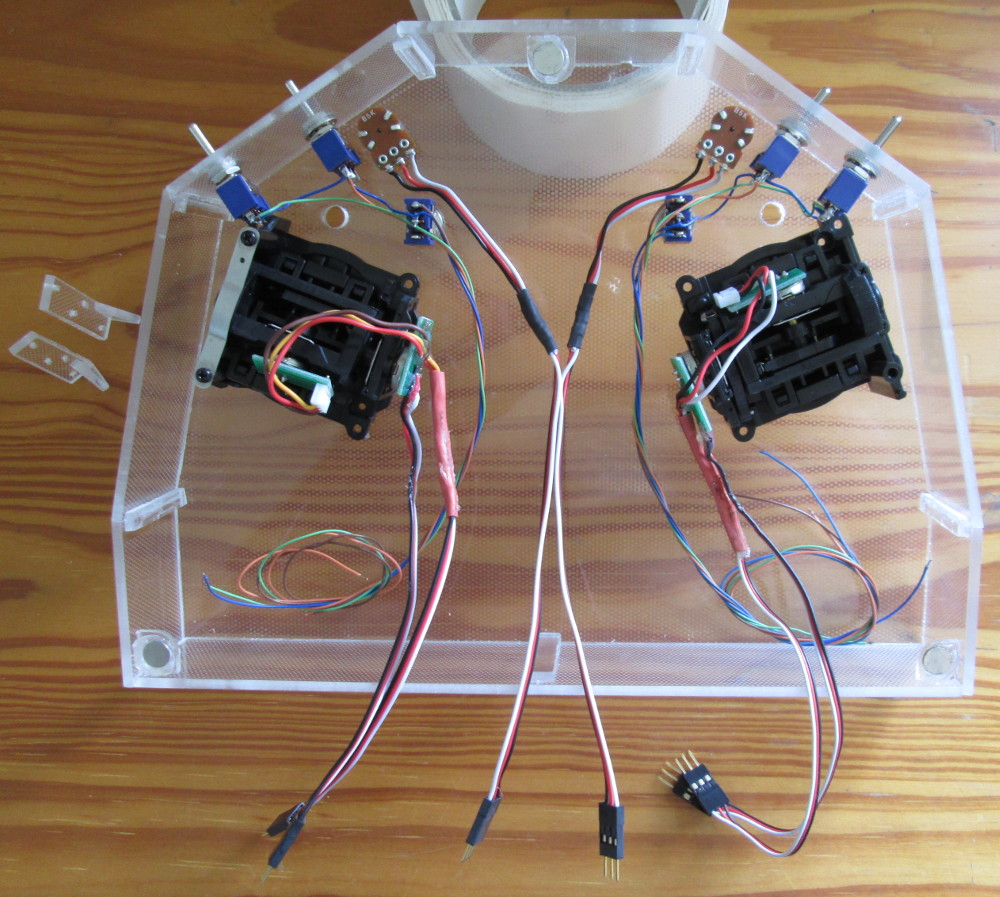
les 2 pièces en " L " au centre ( à gauche sur la photo de dessus ) permettent à la fois de caler le fond - elles font la profondeur du boîtier , comme les cales latérales - et serviront de fixations intermédiaires pour que les fils ne pendent pas entre les soudures et le mega2560
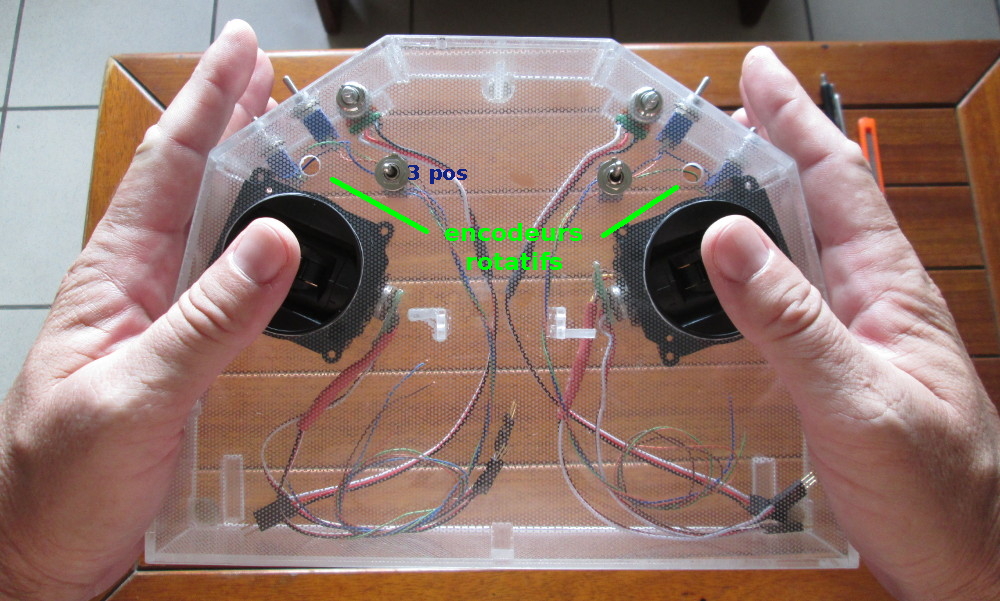
ça devient bon : tout est à portée de doigt , pas besoin de lâcher les manches
la suite en octobre une fois le reste du matériel récupéré
---- 22/09/15
de retour de métropole avec avec le reste du matériel , la suite :
réalisation du support du MEGA2650 et des deux plots taraudés pour deux vis plastiques de 3mm
les 4 fils orange-marron et bleu-noir sont ceux des 2 boutons de navigations "entrée" et "exit"
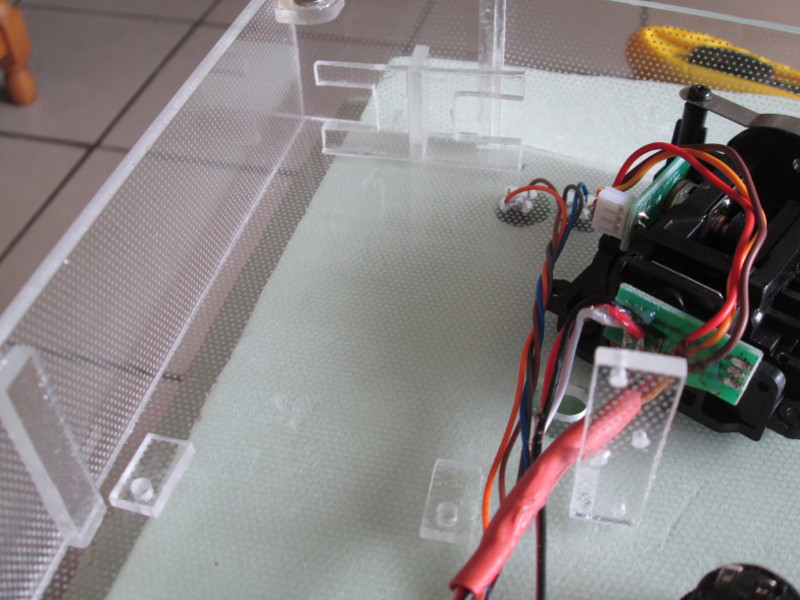
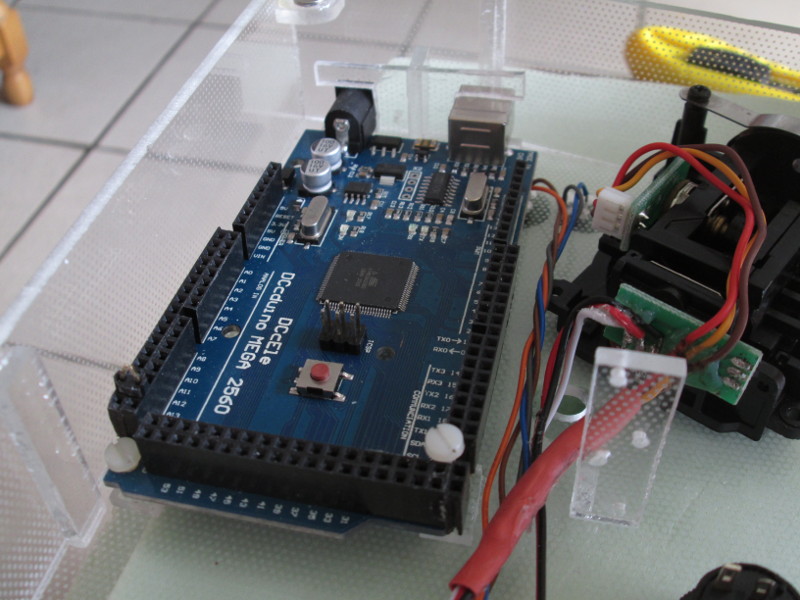
collage de barrettes supplémentaires et câblage vers le 0V pour les bleues et les +5V pour les rouges
en bas à droite le cavalier qui met l'entrée " P3 " à 0V ( pas câblé-installé pour le moment )
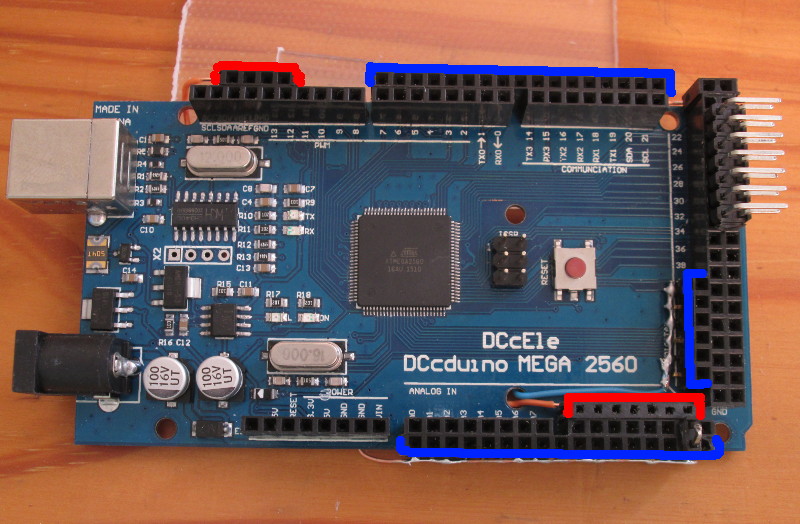
vue de dessous
en haut à droite , soudure de 7 condensateurs de 100nF entre le " 0V " et les entrées analogiques ( 4 manches et 3 potentiomètres )
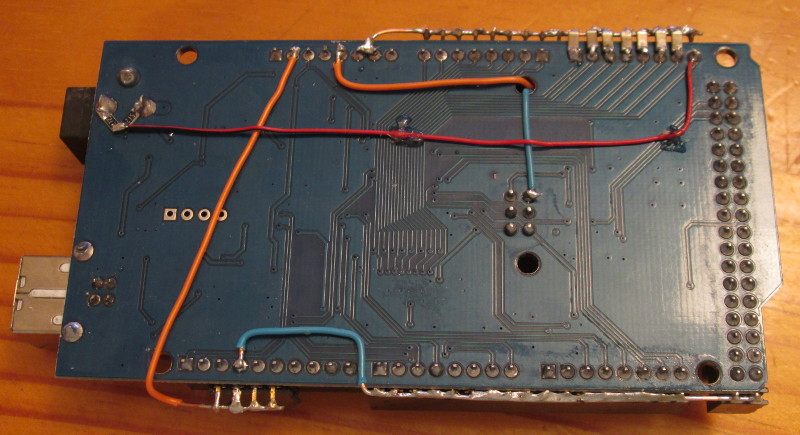
---- 23/09/15


"
Côté technique : à quoi sert un encodeur rotatif ?
Réponse : à régler efficacement une variable en vol.
Prenons un exemple tout simple : soit un planeur avec 3 phases de vol (gratte, lisse, vitesse, par ex.) sur lequel on souhaite distinguer le différentiel d'aileron par phase. Pour cela, on affecte une variable globale (mettons VG1) comme taux de différentiel aux mixeurs, puis on créé une fonction personnalisée pour régler VG1 par un potentiomètre. Pour rappel : chaque variable globale VGx a une valeur propre par phase de vol sur la Taranis, inutile donc de dupliquer les mixeurs.
Le gag, c'est qu'en basculant d'une phase à l'autre, le potar (qui est un organe fournissant une valeur absolue, proportionnelle à sa position) impose de facto à VG1 la valeur à laquelle il est positionné, ce qui écrase le réglage précédent. Voilà qui est particulièrement pénible, car une fois une phase réglée et qu'on est passé à la phase suivante, il ne faut surtout pas revenir à la phase précédente sous peine d'écraser son réglage par la dernière position de potar en cours, sauf à désactiver la fonction personnalisée.
A contratio, un encodeur rotatif fonctionne en relatif par rapport à la valeur existante, il ne la change que quand on le manipule en y ajoutant ou retranchant un incrément / décrément. Donc, quand on change de phase, il n'écrase pas la valeur de VG1 en cours pour cette phase. Pour rappel, c'est exactement le principe de fonctionnement des trims digitaux de manches, qui sont eux aussi des encodeurs incrémentaux de valeurs stockées par phase.
J'ai pris l'exemple du différentiel, mais ça vaut aussi pour les dual-rate, les taux de mixage, ou toute autre valeur qu'on peut différentier par phase de vol.
"
ceux que j'ai choisi : sur ebay.com , " Rotary encoder EC12 e12 " , 24 pas par tour , l'axe fait 6mm de diamêtre , pour trouver un bouton : " knob 6mm " sur le même site
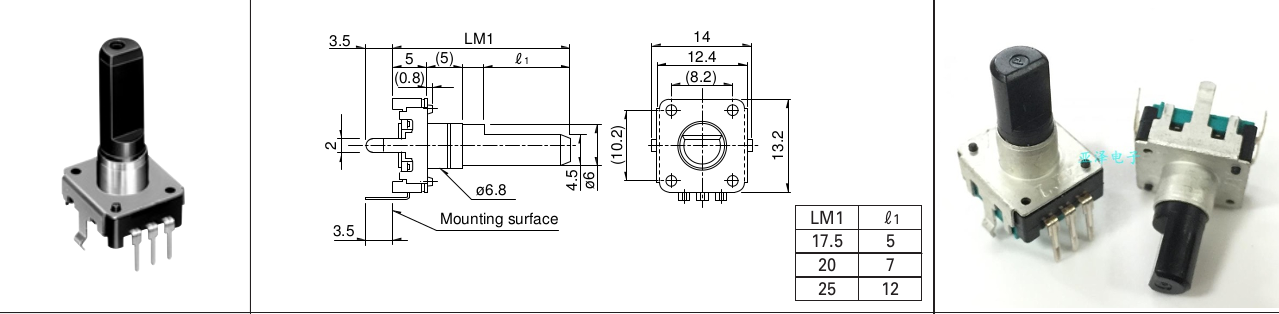
câblage des 2 encodeurs rotatifs et des 3 boutons directionnels
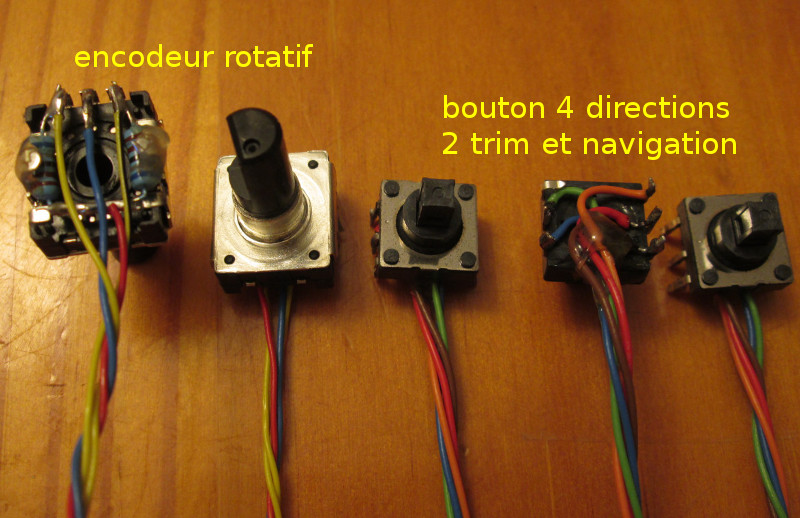
câblage de l’écran + fixation à la colle chaude <------> GAFFE ERREUR : j'ai inversé l’écran " haut-bas " , j'ai du le décoller + dessouder + ressouder les fils pour finir par le retourner
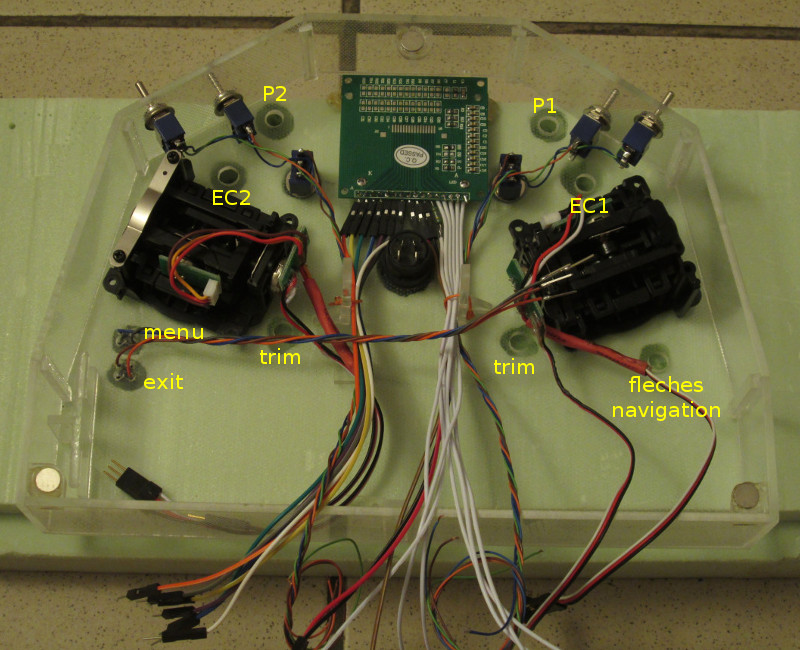
27/09/2015
collage à la colle chaude des boutons des trim et navigation , les 3 câblés avec les même couleurs pour faciliter les branchements sur l'arduino
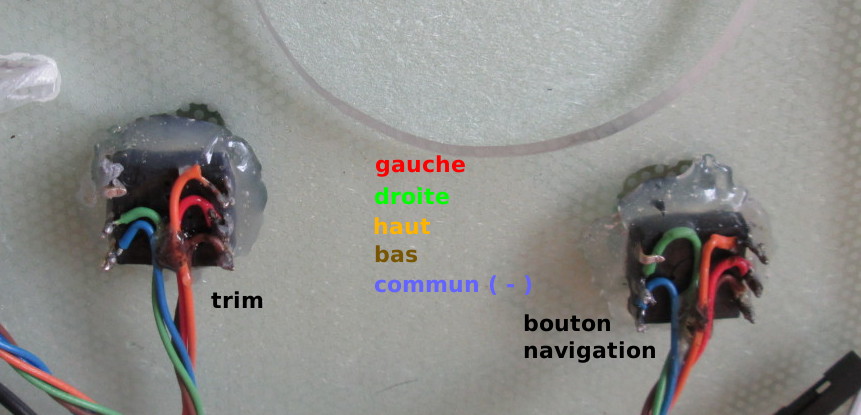
le branchement des potentiometres et des trims
pour chaque trim , les haut-bas et droite-gauche sur soudés sur 2 picots joints pour pouvoir les retourner en cas d'inversion , le fil comun bleu est aussi soudé sur 2 picots pour la résistance mécanique à l'enfichage
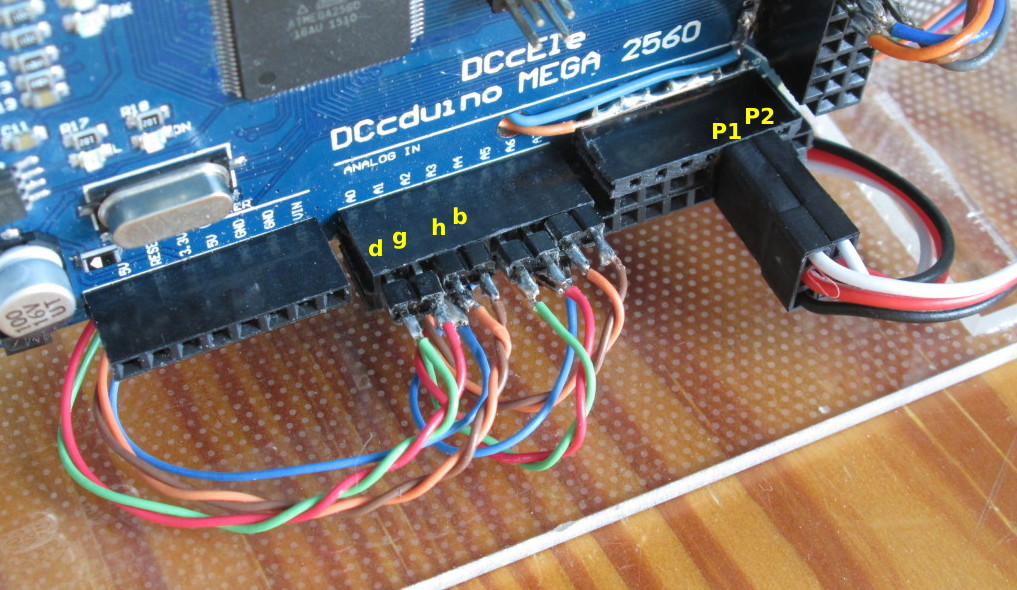
toute les " entrées " sont montées , ça commence à prendre forme <------> GAFFE ERREUR : sur cette photo aussi écran inversé " haut-bas "
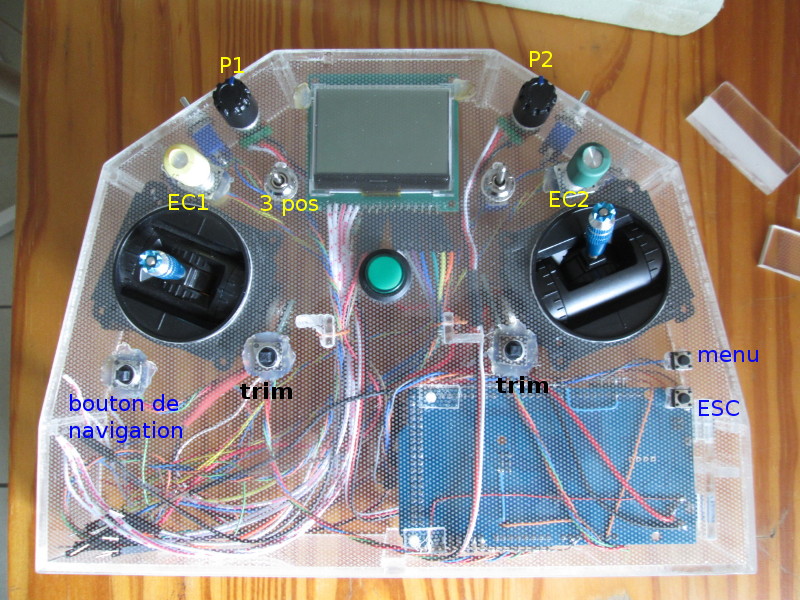
24/10/2015
ça y est..... fini , tout fonctionne au niveau du soft

il reste deux entrées disponibles non-cablées pour le moment : un potentiomètre ( le "P3" ) et le switch "TRN" ( pour celui là , j'ai vu que pour le DLG , au lancé , des p'tits gars on monté un inter momentané sur la face arrière de la radio au niveau de l'index ou du majeur .... )
en bas à gauche du boitier , l'emplacement vide est celui du futur accu , pour les essais c'est actuellement un 2S avec alim sur la prise d’équilibrage
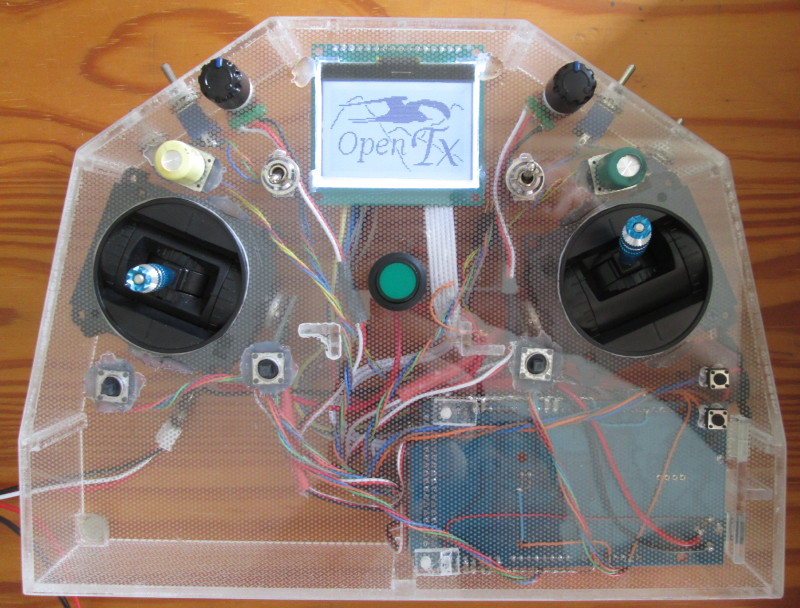
la prise avec les 3 broches apparentes est le branchement du module TX Assan qui prendra place entre la plaque de plexi et l’écran
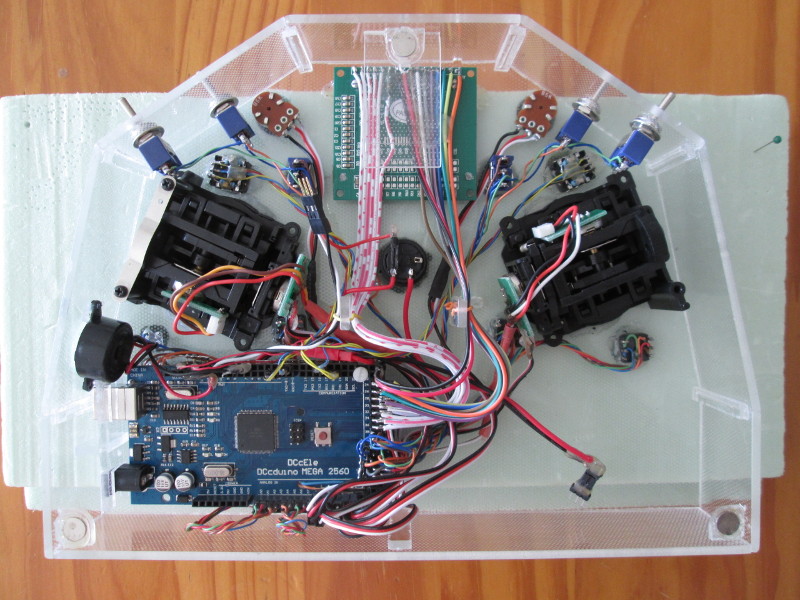
quelques photos de plus :
- le module Tx Assan est positionné sous l'écran , fixé sur la plaque transparente , antenne contre la face avant du boîtier
- pour le moment l'accu est un 3S 2200 mA de la 9XR , il sera bientôt changé pour un 2S
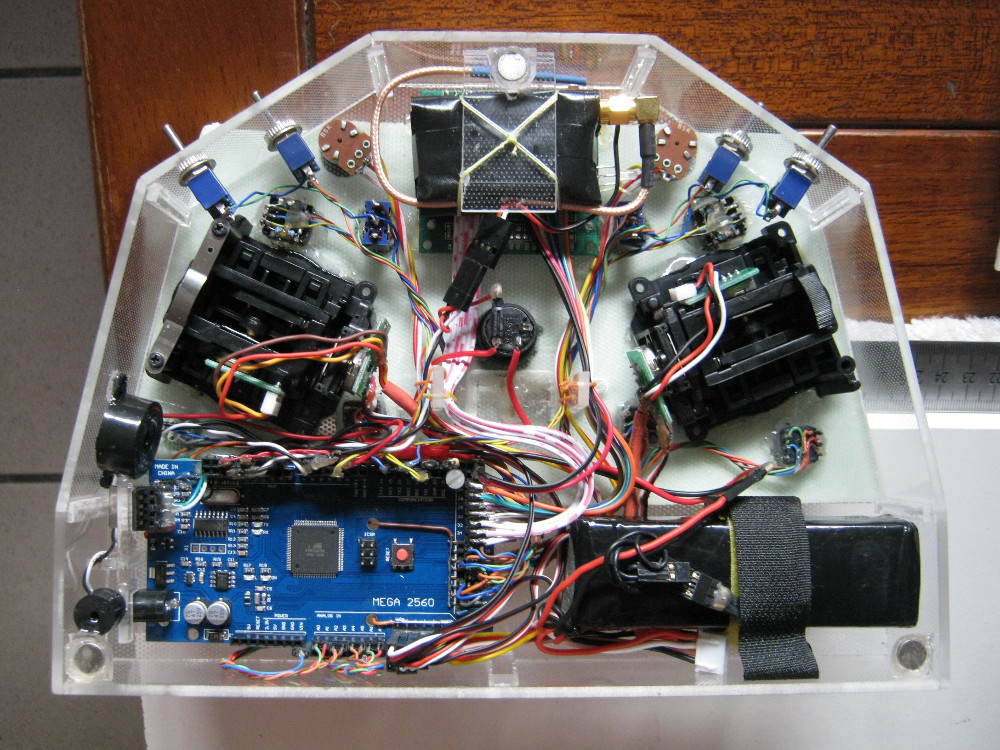
vue de l'antenne 2.4Ghz placée contre la face avant de la radio
fabriquée comme ici : http://home.nordnet.fr/fthobois/antenne 2.4GHz.htm
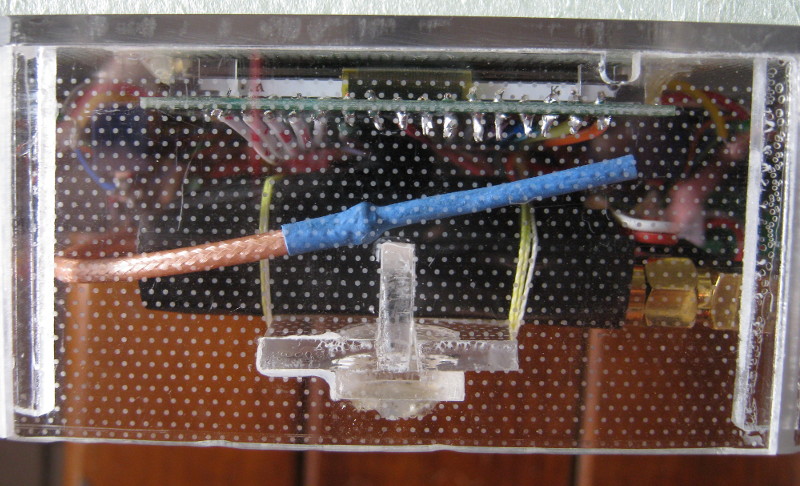
- ajout d'une prise USB collée sur celle d'origine de la carte pour ne pas sortir la carte pour les sauvegardes et mises à jour
- et un HP en 5V ( récup sur une carte mère d'ordi ) pour sortir les bips accessibles dans le menu " fonctions spéciales " , branché sans ampli , le son est un peu moins puissant que celui du buzzer mais bien suffisant
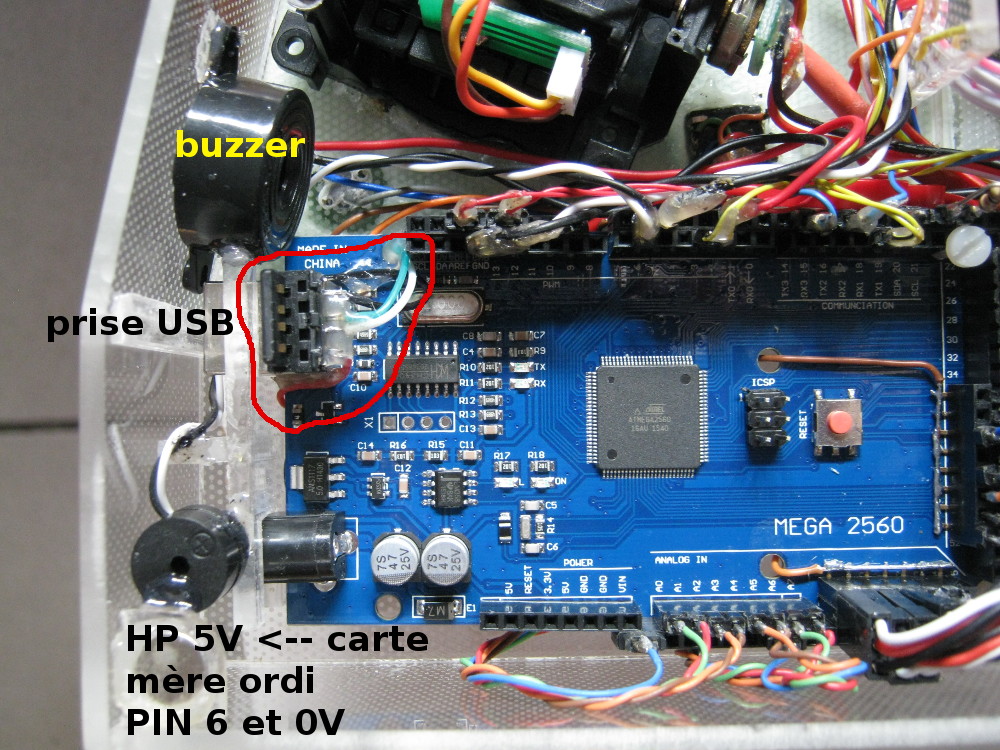
modification des boutons des encodeurs rotatifs , pour augmenter le diamètre : un bout de durit collé + gaine thermo par dessus pour l'accroche
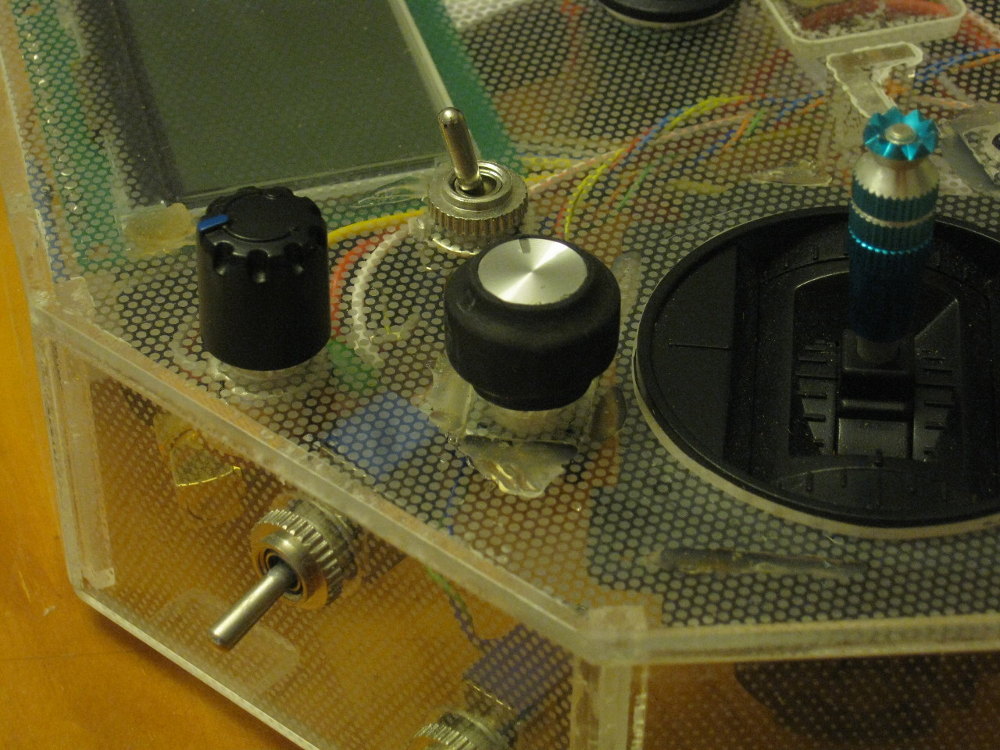
vue d'ensemble
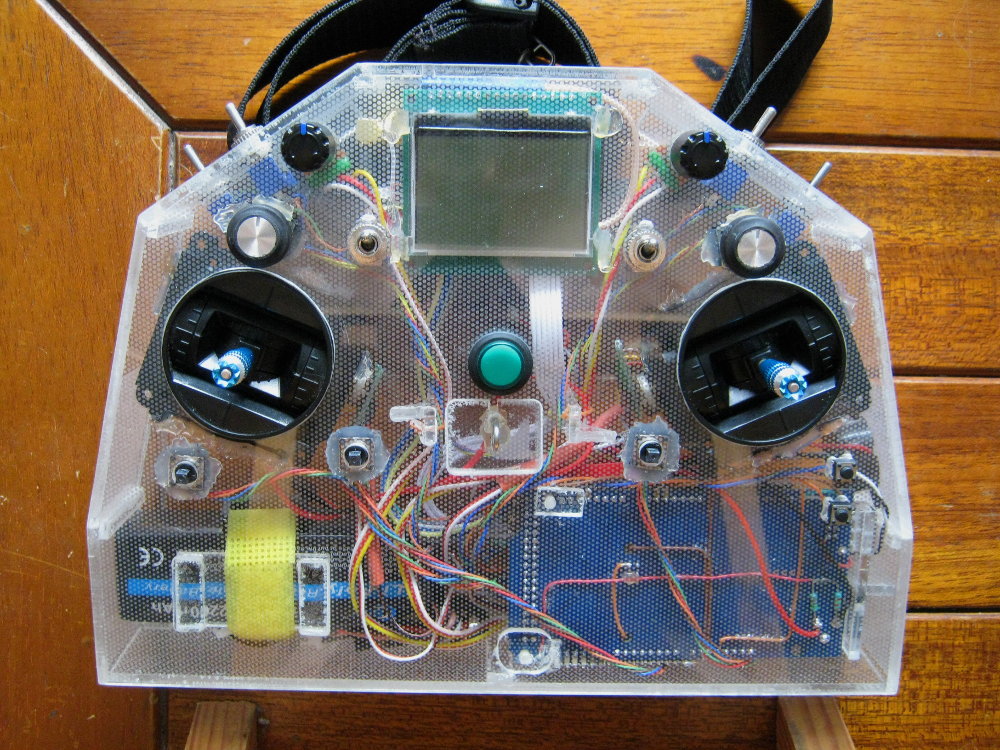
la suite : la modif des potars pour remplacement par des capteurs magnétiques
ce que ça donne
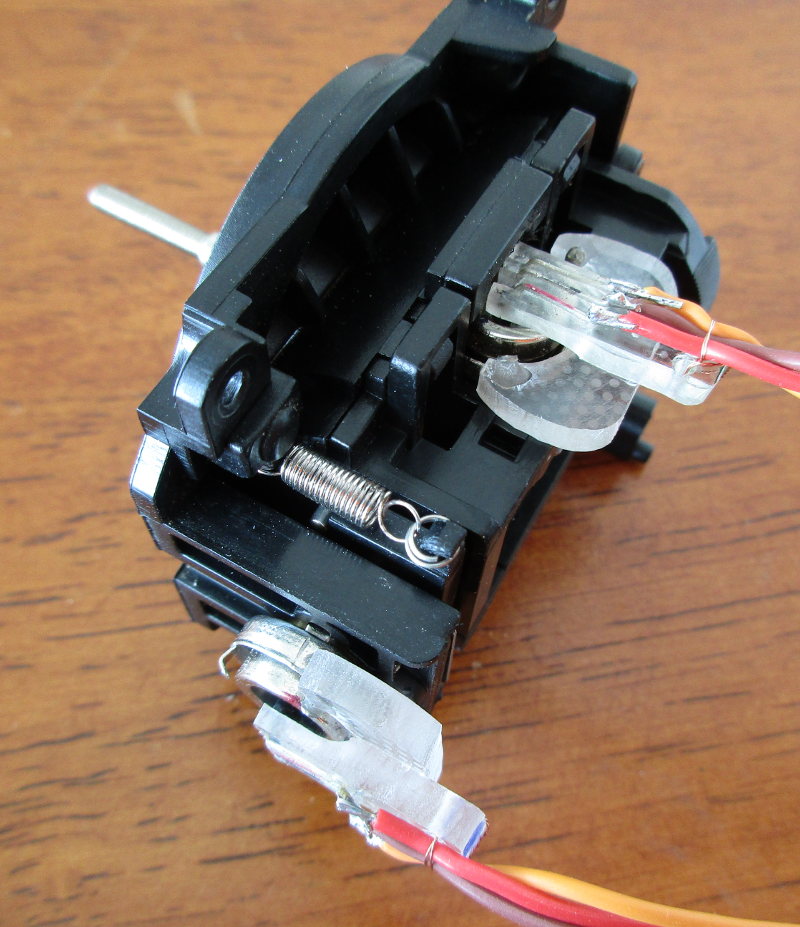
que c'est bôôôôôô
...... mais GAFFE : c'est vraiment très petit <----> sans être compliqué ça n'est pas simple à réaliser , il faut être minutieux , et la modif n'est pas réversible donc 'faut pas se rater
l'idée est de faire tourner le champ magnétique (lié au manche) autour du capteur (lié au châssis fixe) ..... c'est pas clair
voilà l'idée de départ , 02 aimants en jaune collés sur un support qui génèrent un champ magnétique dans lequel est plongé le capteur ( mais au final j'ai trouvé des aimants diamétralement magnétisé percés avec les bonnes dimensions , voir plus bas )
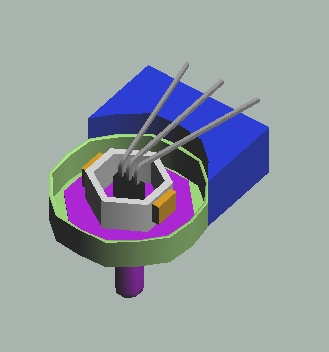
lors de la rotation du manche et de l'aimant , l'intensité du champ magnétique entrant dans le capteur varie suivant une sinusoïde …. et la linéarité ? comme les manches de la 9XR débattent de +/- 25° autour du neutre , la variation reste dans la zone quasi linéaire " en vert " de la tension de sortie / angle du manche ( pour les matheux , il y a 1.2 % de différence entre les valeurs X et SIN(X) pour 25° de débattement )
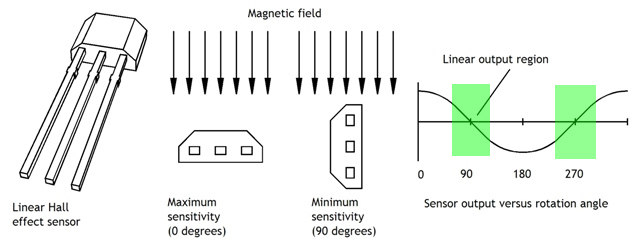
sans champ magnétique la sortie du SS495 est à la moitié de la tension d'alimentation : 2.5V ( L'arduino fournit du 5V )
quand le champ magnétique est parallèle au capteur , le champ "n'entre" pas dans le capteur , la tension de sortie est aussi à la moitié de la tension d'alimentation
quand on approche le pole Nord d'un aimant la tension monte de 2.5V vers la tension d'alimentation , quand on approche un pole Sud la tension descend de 2.5V vers 0V
le matériel utilisé et les dimensions des pièces :
du plexiglass de 3mm <<< boîtier de la radio
04 capteurs hall SS495A1
04 aimants diamétralement magnétisés 10mm ext x 7mm int x 3mm de haut
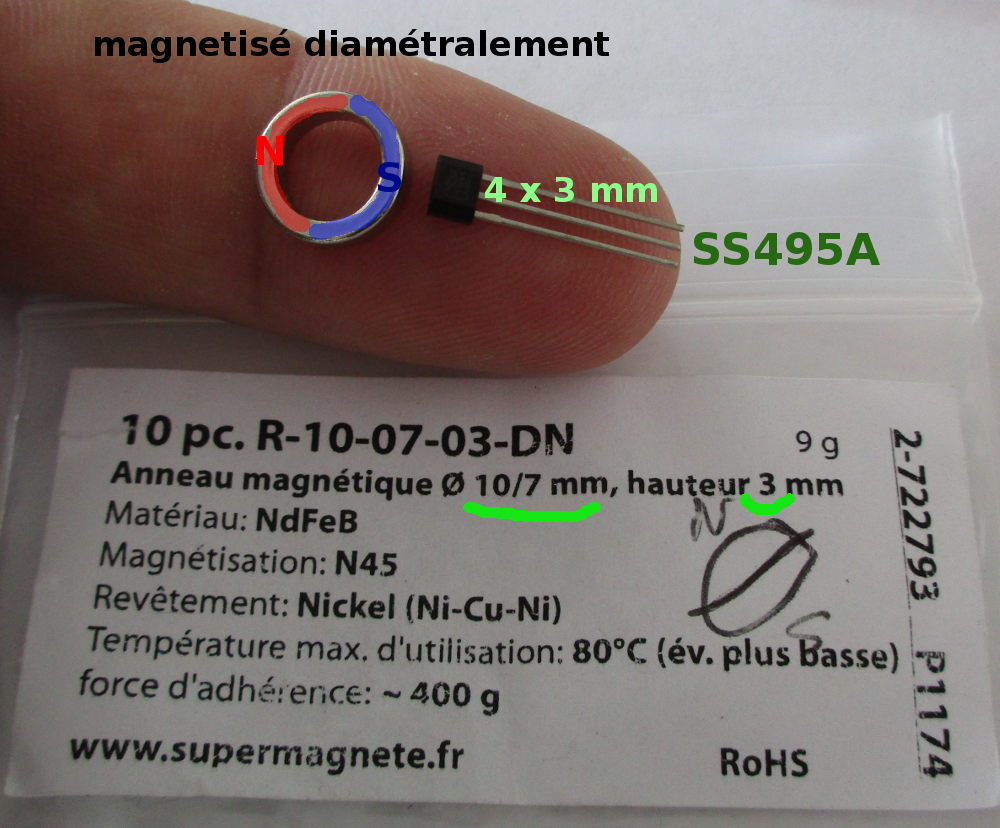
démontage du potar : déplier --- sans les casser , ça va servir + tard --- les pattes qui tiennent la piste carbone , vue sur le "peigne" qui frotte sur la piste carbone et qu'il va falloir enlever
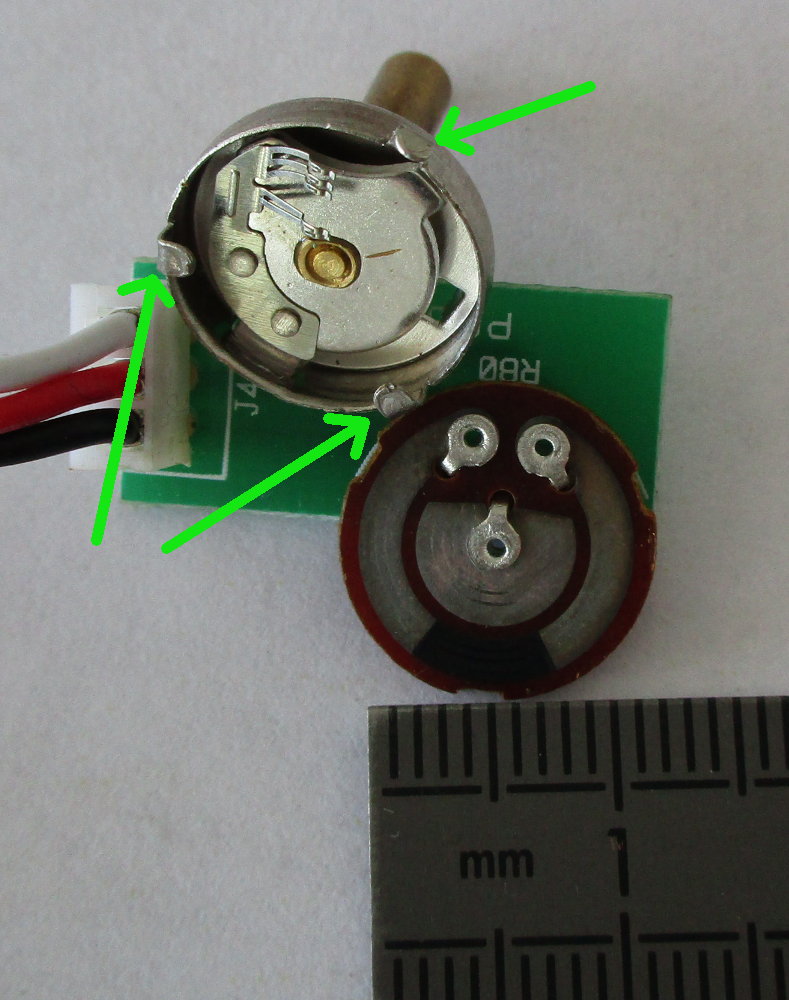
une photo pour se faire une idée de l'usure de la piste carbone après 3 ans d'utilisation , environ une centaine d'heures / an
remarque : je n'ai pas eu de pb de faux-contacts jusqu'à aujourd'hui
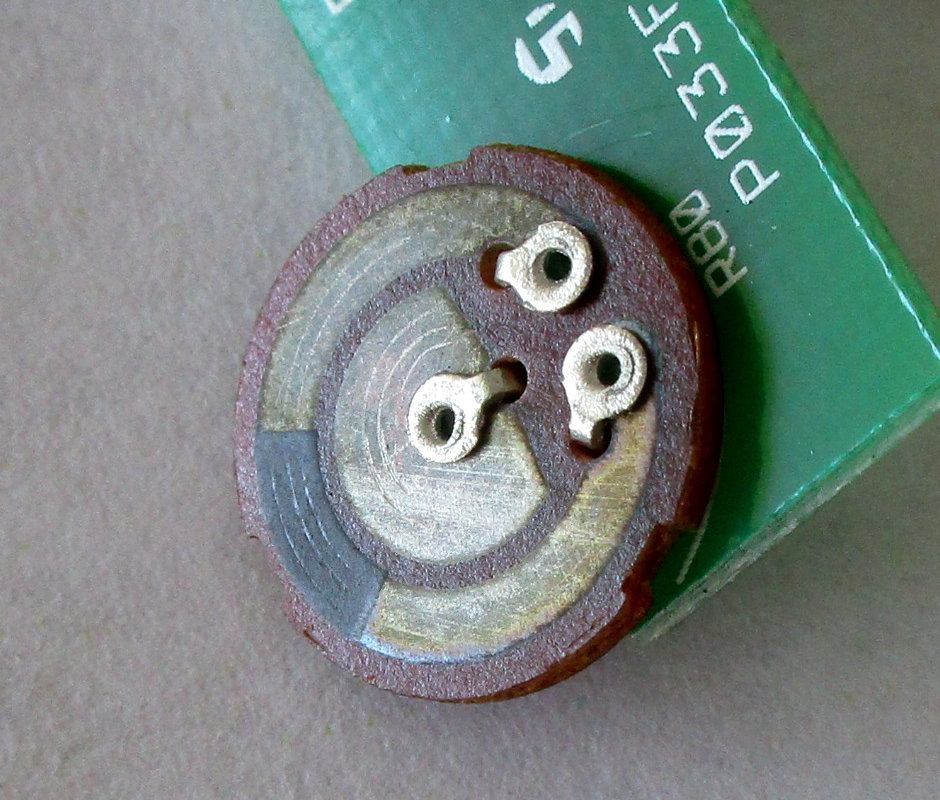
"peigne" enlevé en tirant dessus , il reste ses deux plots de fixation
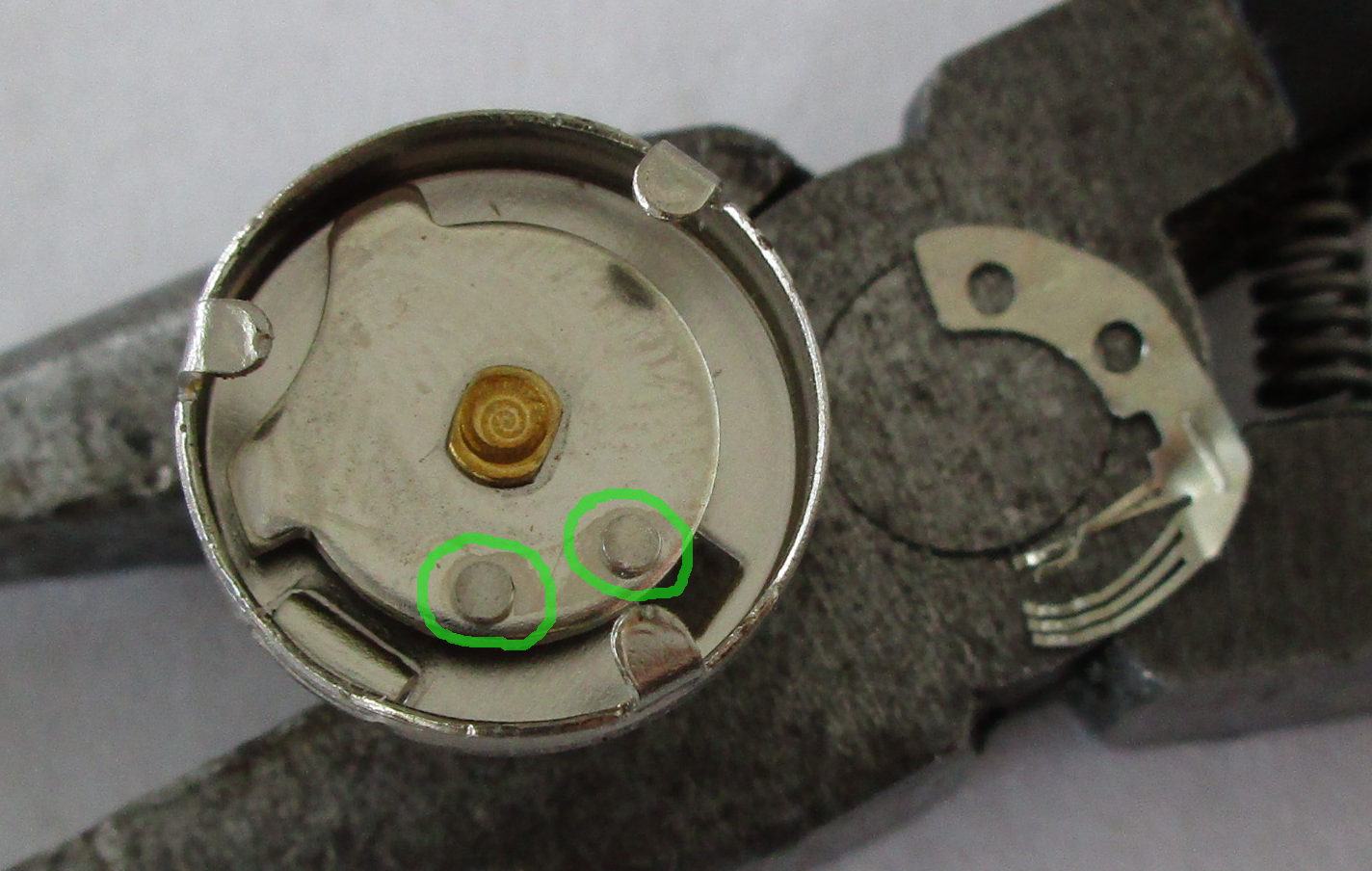
usinage des plots à la mini-perceuse et mini-fraise + rayures sur le plateau qui portera l'aimant + rayures sur un flan de l'aimant <-- collage époxy lente
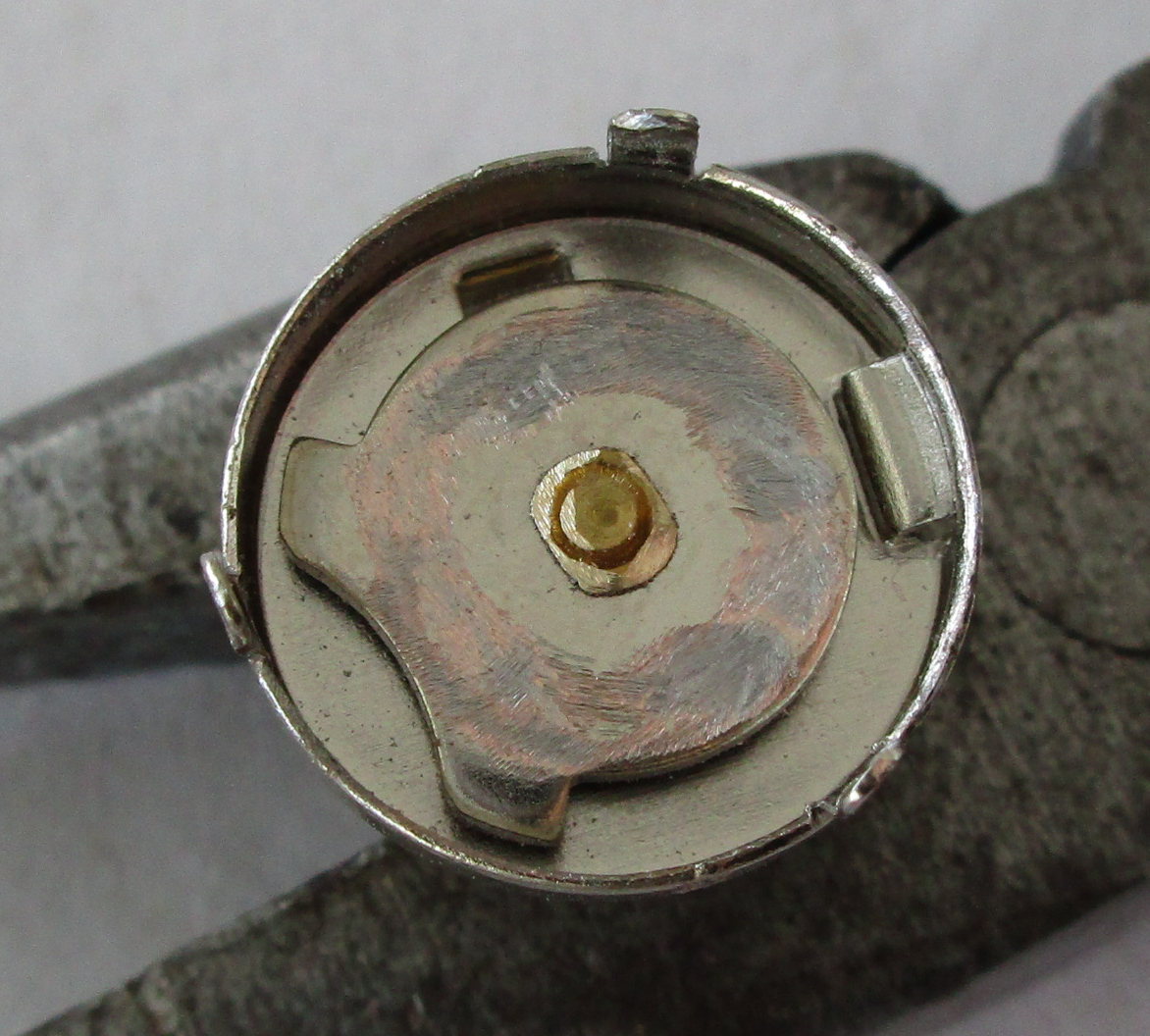
collage de l'aimant , explications :
- les 03 pattes - qui n'ont pas été cassées
- sur l'axe du potar il y a le méplat qui le lie au manche , il faut coller l'axe N/S de l'aimant parallèle au plan du méplat
- pour trouver le Nord et le Sud placer l'aimant sur un petit bout de dépron , déposer le tout dans une assiette avec un fond d'eau , cool , on viens de réinventer la boussole
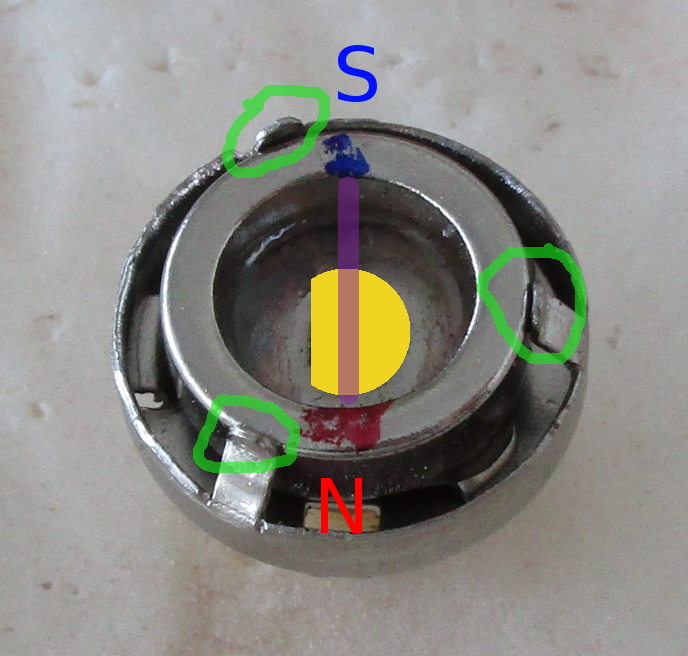
collage d'une partie du support en plexiglas du capteur sur le potar à l’époxy , les pattes sont encore là pour renforcer le collage
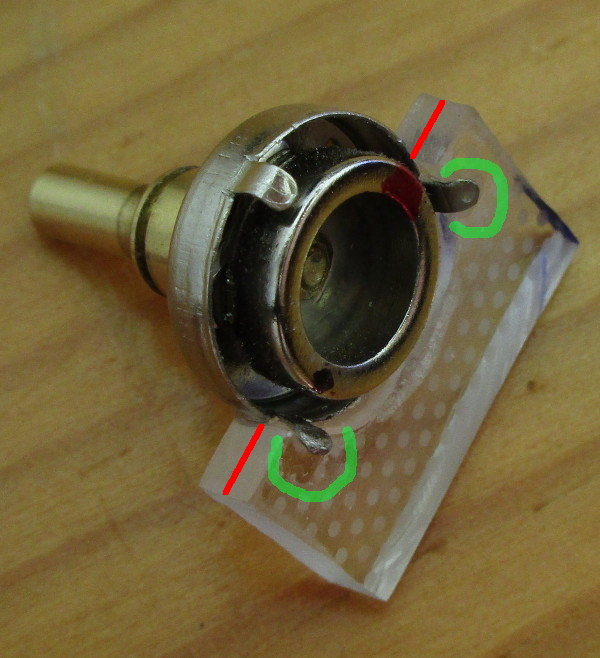
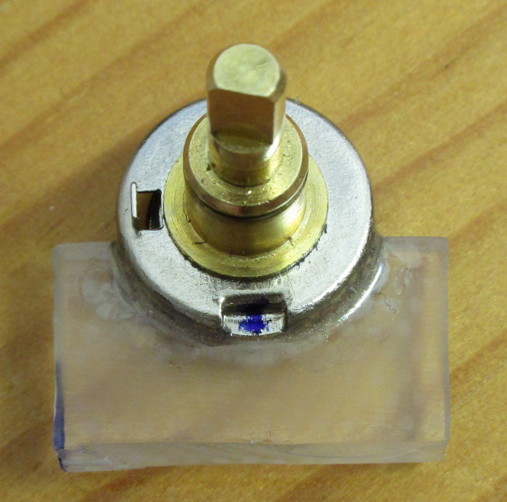
fabrication de l'autre moitié du support du capteur
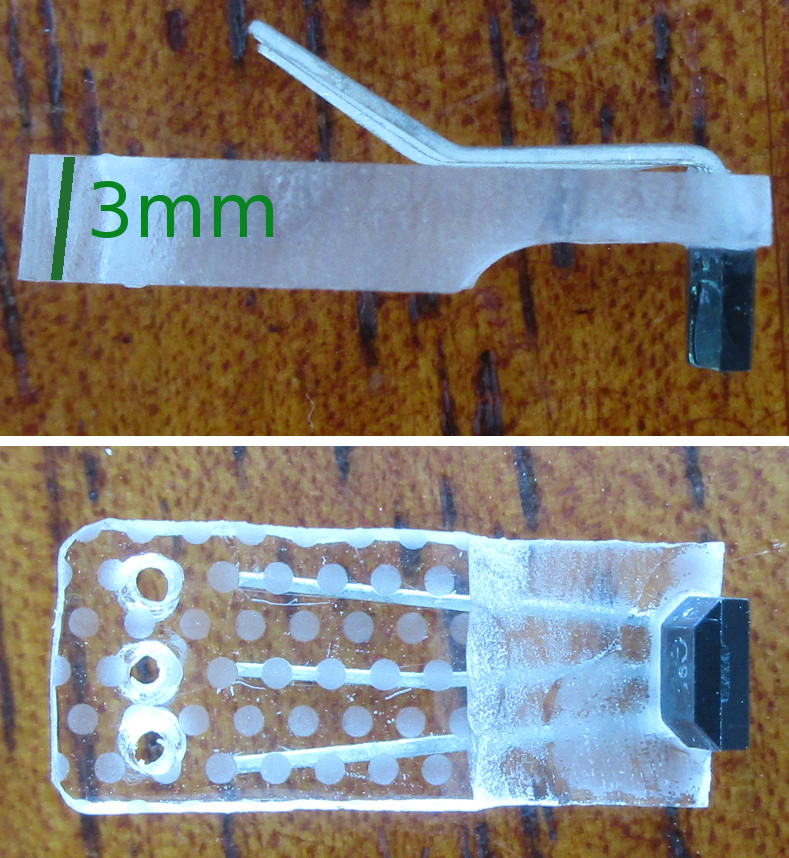
soudure des 3 fils + - et signal , ligature des 03 fils au support avec un fil de cuivre pour la résistance mécanique
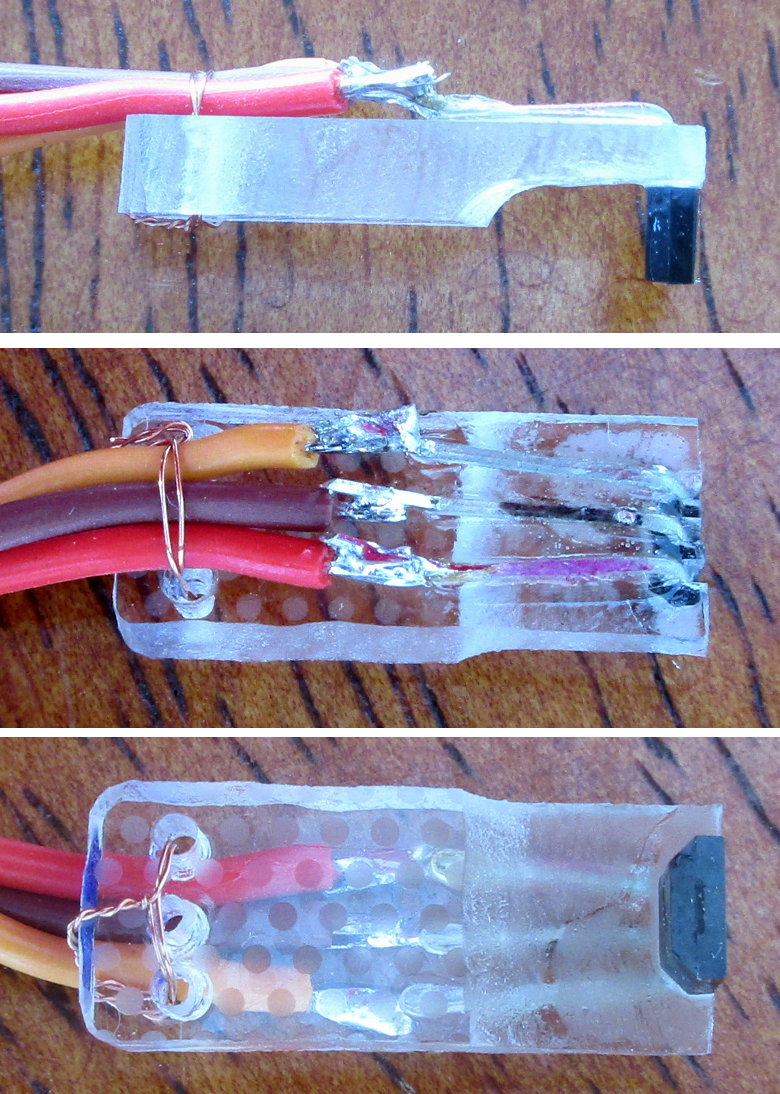
collage des 02 supports du capteur :
remonter le potar sur le manche ( ici manche Direction avec son ressort de rappel au neutre )
alimenter le capteur avec une alim 5V , mesurer réellement la tension de cette alim , puis placer le voltmètre sur la sortie signal du capteur
tout en gardant le capteur toujours au centre de l'aimant , faire tourner le "petit" support plexi pour arriver à lire exactement la tension-mesurée/2 au voltmètre
ne plus bouger , déposer une goutte d'acétone pour coller-fusionner les 02 plexi ( voir plus haut le collage du boîtier )
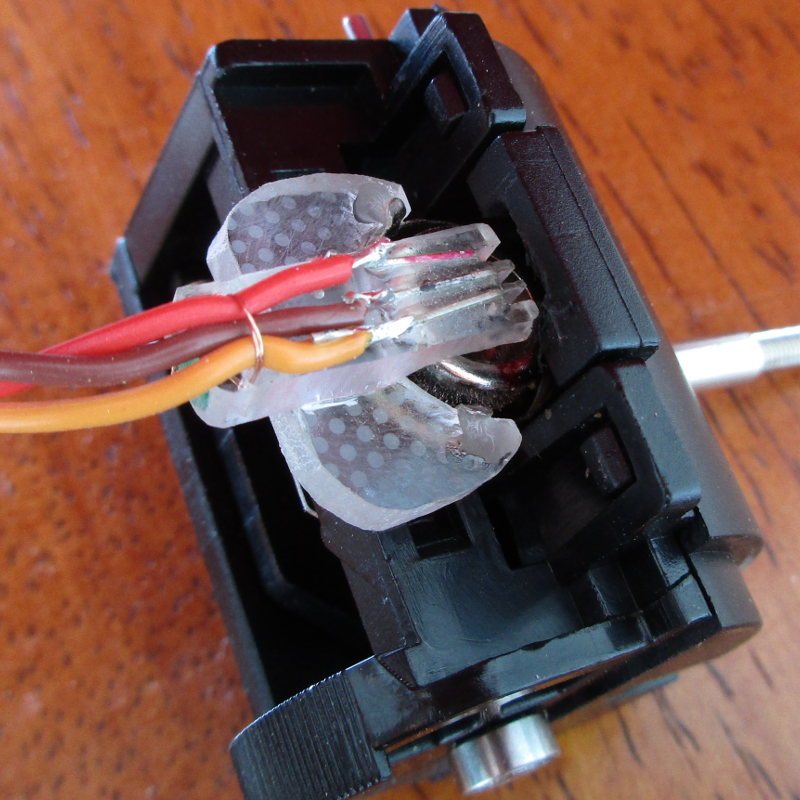
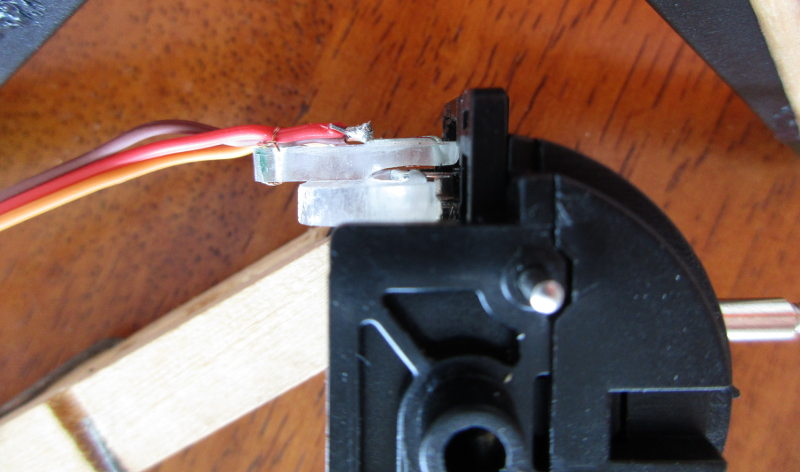
le petit plexi peut finir collé légèrement décalé pour avoir tension-mesurée/2
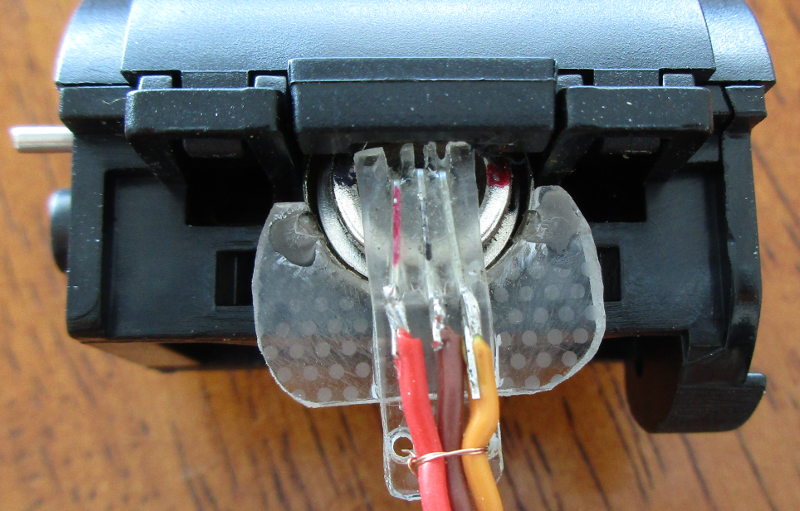
le potar de la Profondeur
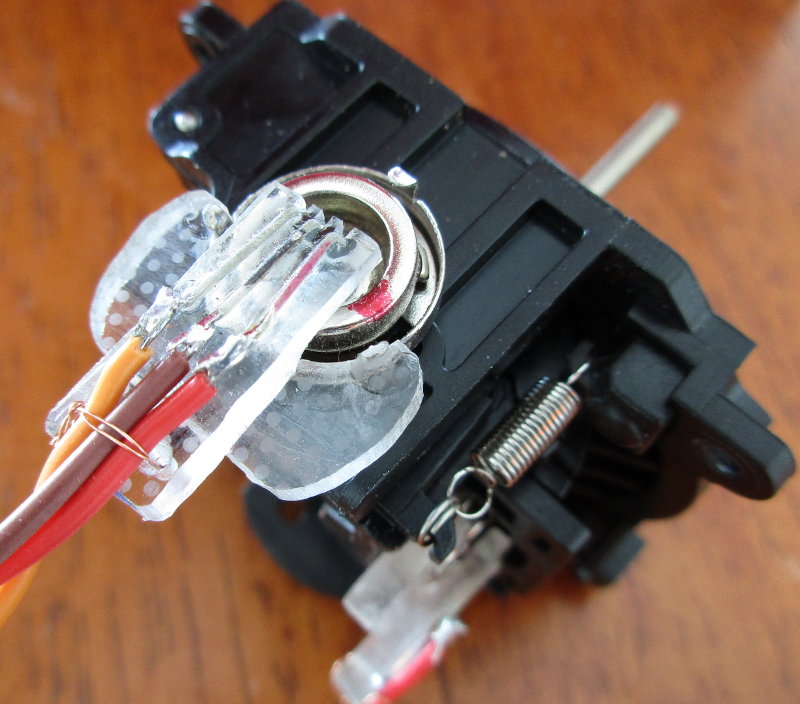
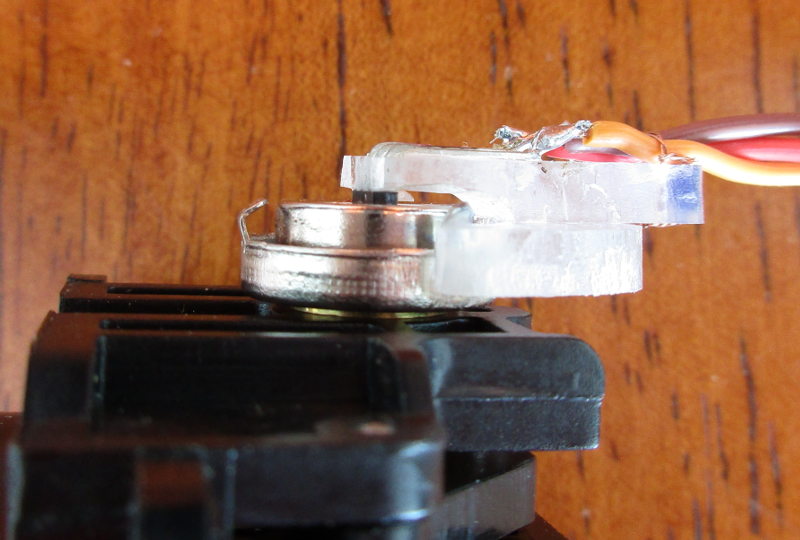
le bloc Dir Prof
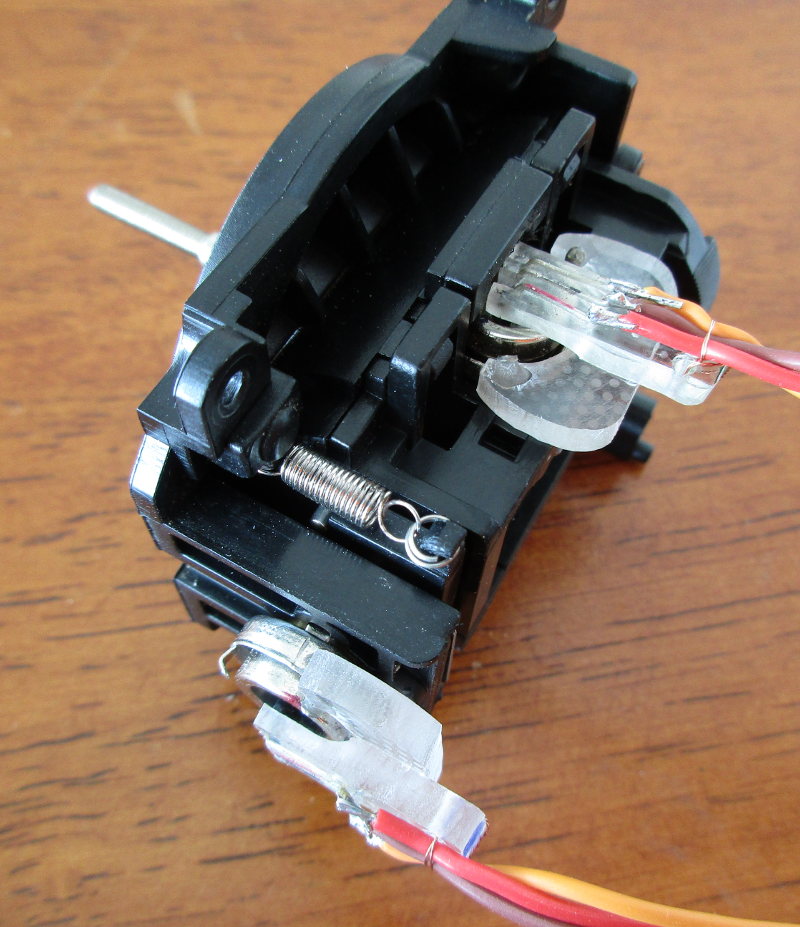
après ré-étalonnage des manches et potars , tout fonctionne nickel :
la sensibilité est excellente : entre le pouce juste posé sur le manche ou enlevé il y a une variation de 0.2 à 0.3 % à l'affichage
manche poussé en butée et ramené , la valeur revient quasi à l'identique +/- 0.1%
20/12/16
salut
suite au changement des potentiometres des manches par des capteurs magnétiques , j'ai fait quelques mesures de conso pour vérifier la doc technique des capteurs qui annonçait 7mA / capteur
j'ai pu me faire preter un multimetre pour pouvoir mesurer les petits courants ( sinon je n'ai qu'une pince ampèremetrique AC/CC , le plus petit calibre 40A , 2 décimales après le point , pas top pour la précision

quelques mesures :
130mA module Assan en emission + Led retro-eclairage écran allumée ( démarrage de la radio )
121mA module Assan en emission et Led écran éteinte ( tempo réglée à 10s )
76mA module Assan débranché et Led écran éteinte ( reste le Méga 2560 , 2 pot de 5Kohm et les 04 manches à capteurs magnétiques )
44mA les 04 manches débranchés
32mA / 4 : un capteur magnétique SS495A consomme donc 8mA , proche des 7mA de la doc

depuis cet été la radio est alimentée avec un 2S 1100mAh , ça donne un peu plus de 8H d'autonomie

A+ bons vols
02/2019 une autre modif ....
---> avant de me lancer là dedans , j'ai essayé de "lire/comprendre" le code NextStepRc pour essayer de voir comment fonctionnent la partie relative aux encodeurs rotatifs , après avoir trouvé " quelques lignes " en rapport avec ces derniers , je dois dire que bien comprendre pour pouvoir modifier sans tout casser n'est pas à ma portée

remplacer les encodeurs rotatifs par des switch doubles
il y avait ça sur ma MX16S , il me semble que c'est plus simple de juste lever ou baisser un petit levier plutôt que de faire tourner un axe <--- ça n'engage que moi

il y en a dispo dans le commerce du genre trim de taranis facile à trouver sur le net , mais ici , à mayotte , livraison et délai


donc fabrication en plexiglass pour l'intergrer au boitier transparent :

les deux switchs ( 1 commun , 2 contacts ) sont fixés à la colle chaude
en place en haut du boitier , le carré de plexi bouche l'emplacement de l'ancien encodeur rotatif
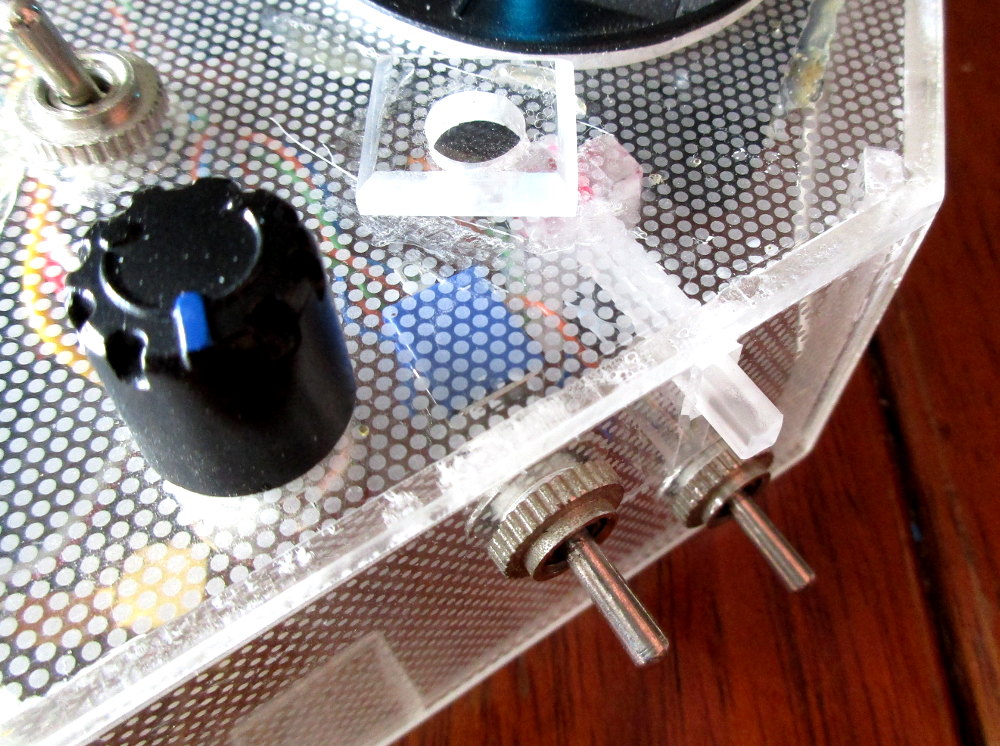
vu dans le boitier :
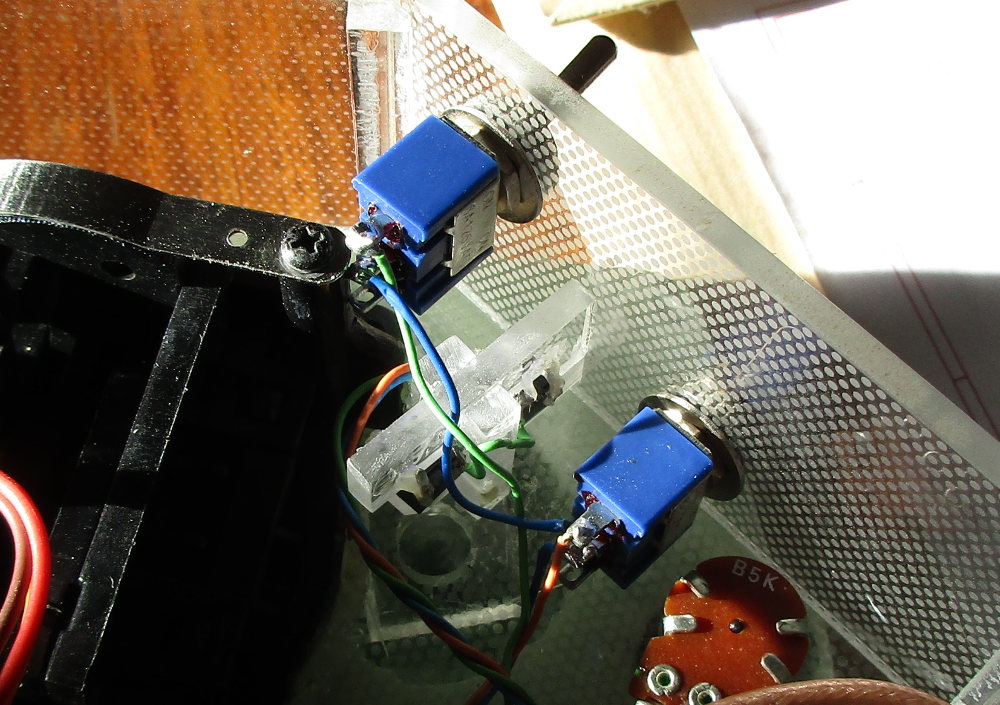
évidement pour replacer les Encodeurs par des switchs , il faut "transformer" les appuis sur les switchs en signal similaire/simulant celui des Encodeurs Rotatifs , un petit arduino attiny85 fera le bouleau
comme il n'y a plus de cran/pas de l'encodeur , un buzzer signalera les appuis , un appui bref incrémente/décrémente d'un " pas+bip " , l'appui maintenu = environ 8 à 10 " pas+bip " / seconde
ne pas tenir compte des 1er doubles-switchs qui étaient trop gros pour loger entre les éléments déjà présents dans le boitier.....
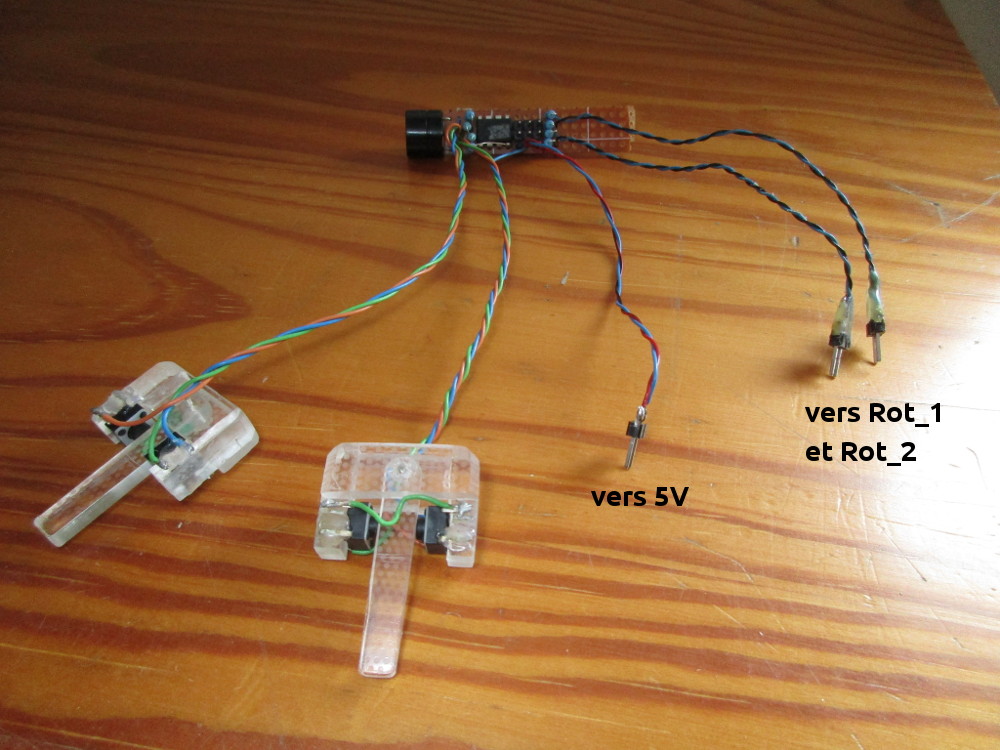
les 06 picots à droite du attiny85 servent à la programmation ( on peut s'en passer avec un support CI , pour la prog sur un support externe mais je n'avais pas )
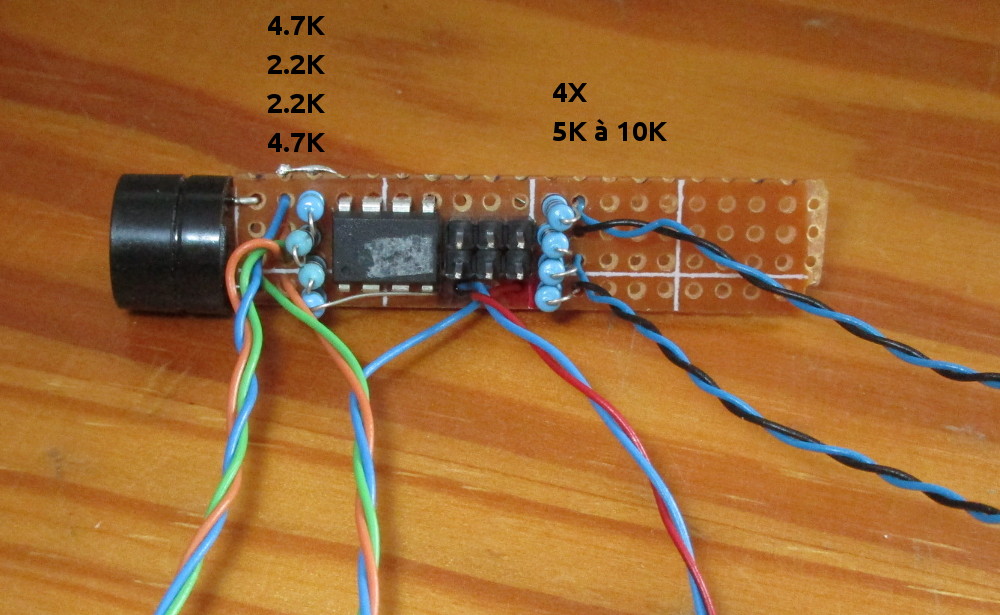
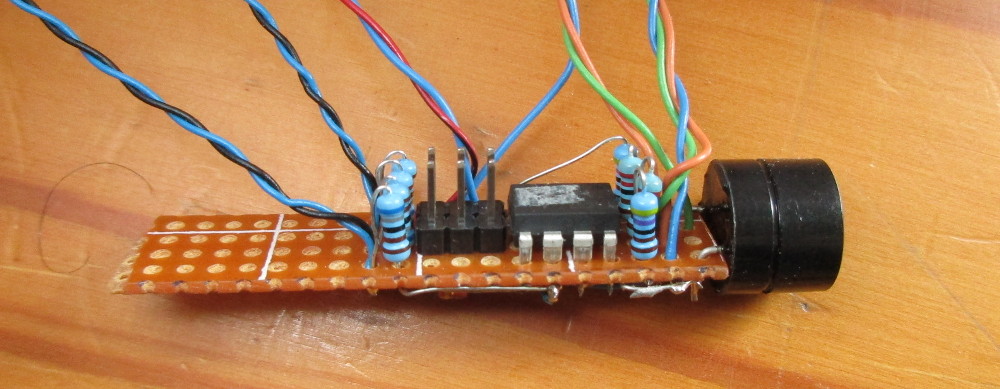
fait à l'arrache... voilà le schéma de principe utilisé :
les traits verts représentent le couplage mécanique entre 02 switchs = montés en vis à vis dans le même bloc de plexiglass
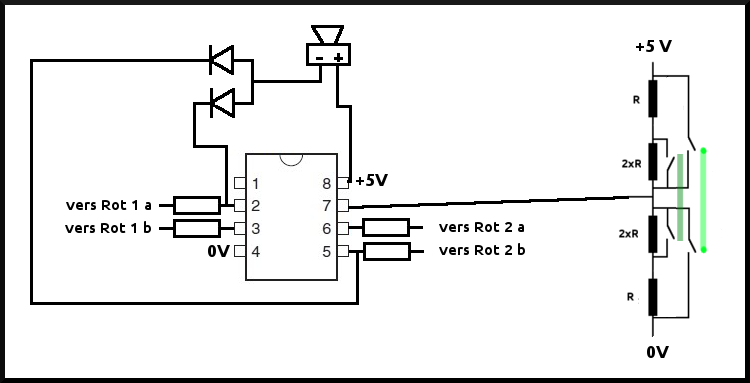
si ça intéresse du monde je ferai un copié-collé des quelques lignes de code pour l'attiny85
dès que je trouve un peu de temps , je poste une vidéo du fonctionnement ----> https://www.dailymotion.com/video/x725pqz
25/10/20
un "repère physique" sur le centre du manche des gaz :
- perso je pilote un moto-planeur en séparant en 3 zones la course des gaz : (voir plus bas )
zone supérieure = sortie AF ou relevé aileron en proportionnel
zone inférieure = courbure en proportionnel
zone centrale = tout en "lisse"
+ démarrage/arrêt moteur sur un inter temporisé
- valable sur une radio dont on peut ouvrir le boîtier facilement/rapidement sur le terrain pour passer du pilotage avion/ multicoptere vers moto-planeur et inversement
un peu de pliage
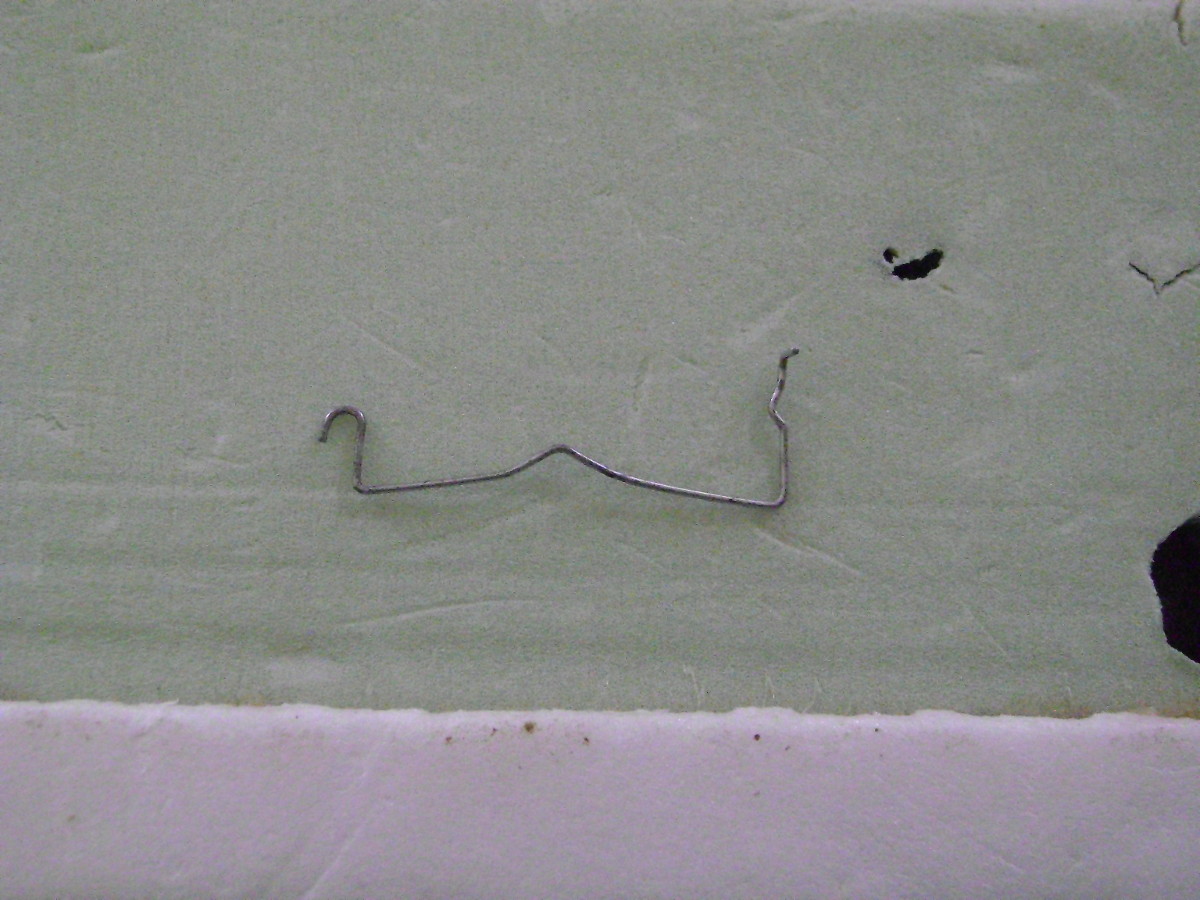
à la lime : une petite encoche au centre et sur le côté ( pas sur le dessus )
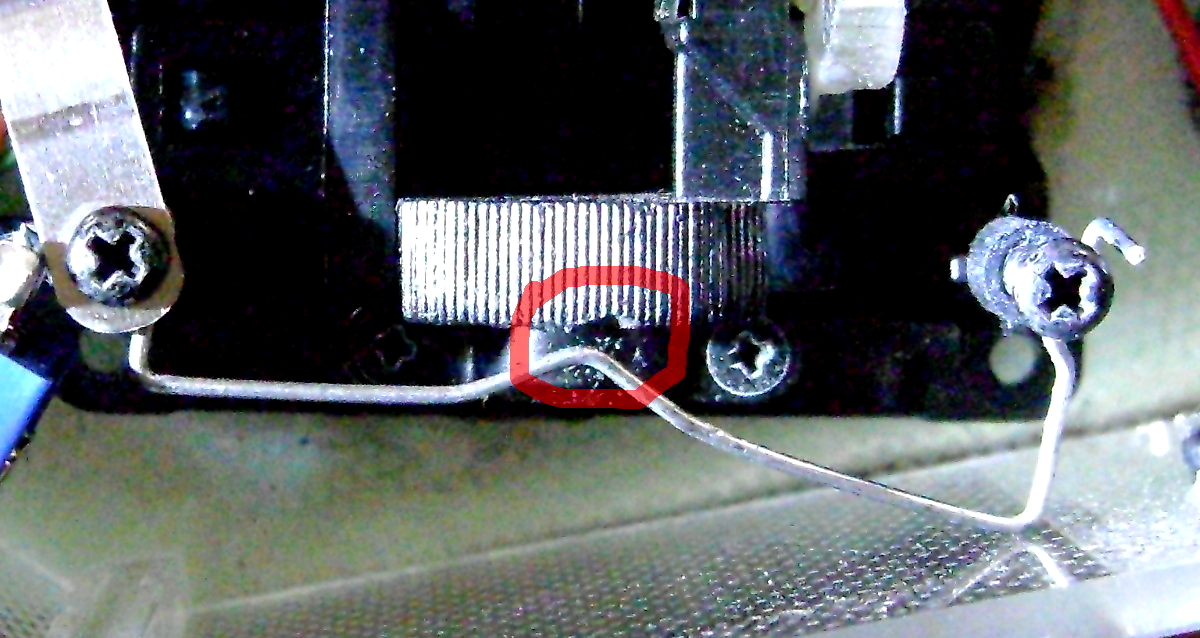
d'un doigt on passe de la position avion ( manche libre ) à la position moto-planeur ( manche avec repère physique central )
désolé pour la définition du GIF animé

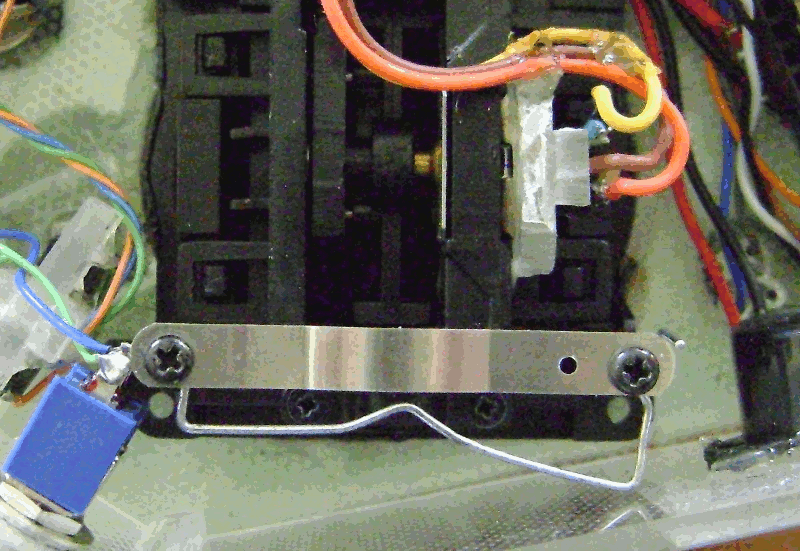
le principe de la prog du manche de gaz et du switch moteur temporisé
+ le trim de gaz qui permet d'ajuster la puissance entre 60% - à la pente - et 100% - en plaine -

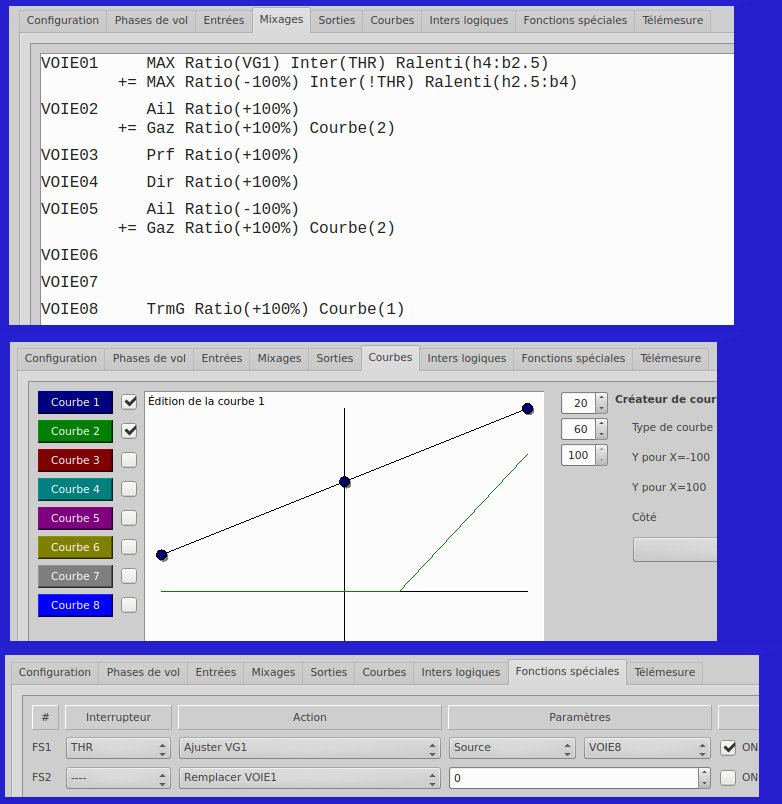
A+ bons vols